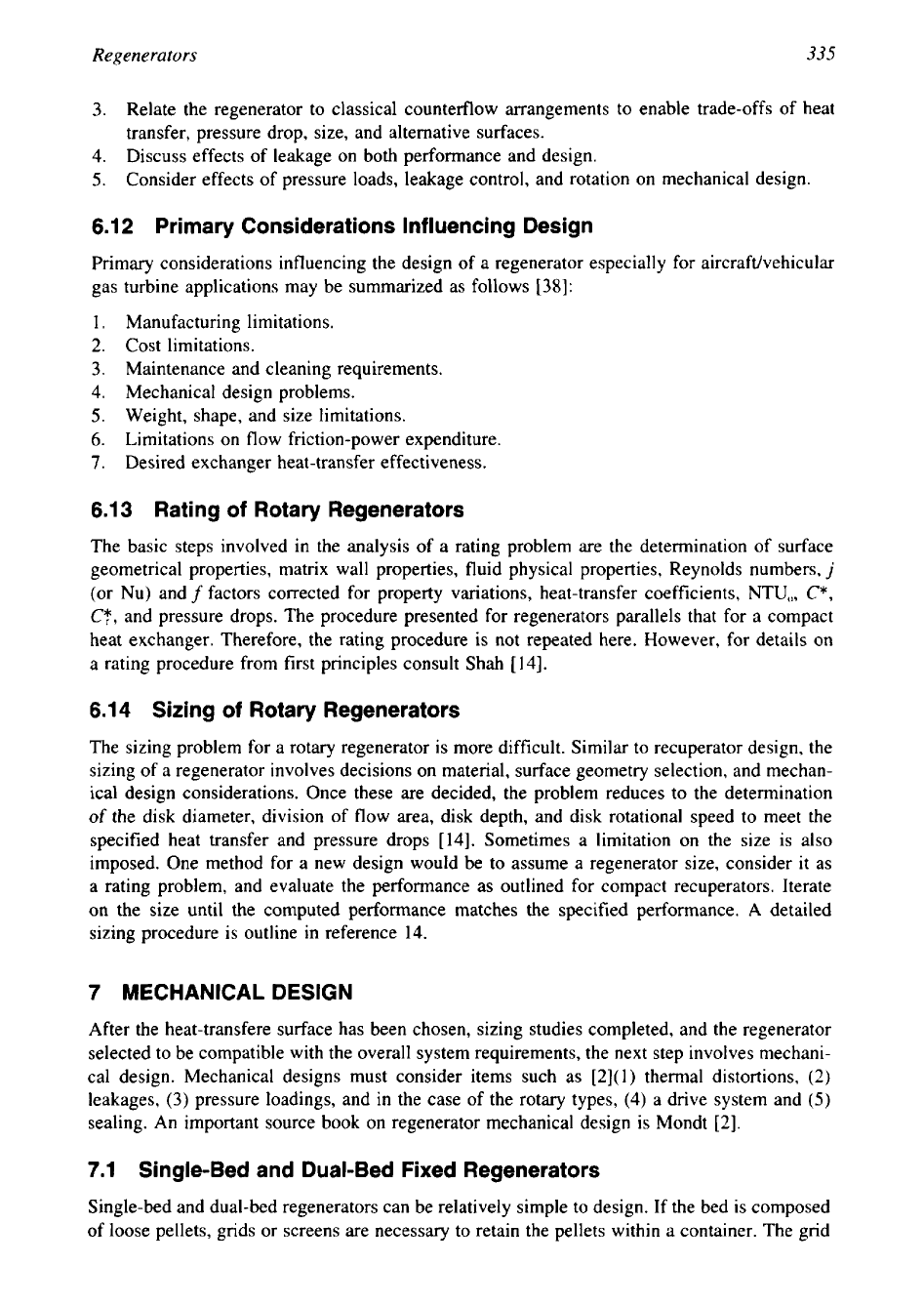
Regenerators
335
3.
Relate the regenerator to classical counterflow arrangements to enable trade-offs of heat
transfer, pressure drop, size, and alternative surfaces.
4.
Discuss effects of leakage on both performance and design.
5.
Consider effects of pressure loads, leakage control, and rotation on mechanical design.
6.1
2
Primary Considerations Influencing Design
Primary considerations influencing the design of a regenerator especially for aircraftlvehicular
gas turbine applications may be summarized as follows [38]:
1.
Manufacturing limitations.
2. Cost limitations.
3. Maintenance and cleaning requirements.
4. Mechanical design problems.
5.
Weight, shape, and size limitations.
6.
Limitations on flow friction-power expenditure.
7.
Desired exchanger heat-transfer effectiveness.
6.13 Rating
of
Rotary Regenerators
The basic steps involved in the analysis of a rating problem are the determination of surface
geometrical properties, matrix wall properties, fluid physical properties, Reynolds numbers,
j
(or Nu) and
f
factors corrected for property variations, heat-transfer coefficients,
NTU,,,
C*,
CT,
and pressure drops. The procedure presented for regenerators parallels that for a compact
heat exchanger. Therefore, the rating procedure is not repeated here. However, for details on
a rating procedure from first principles consult Shah
[
141.
6.14 Sizing of Rotary Regenerators
The sizing problem for a rotary regenerator is more difficult. Similar to recuperator design, the
sizing of a regenerator involves decisions on material, surface geometry selection, and mechan-
ical design considerations. Once these are decided, the problem reduces to the determination
of
the disk diameter, division of flow area, disk depth, and disk rotational speed to meet the
specified heat transfer and pressure drops [14]. Sometimes a limitation on the size is also
imposed. One method for a new design would be to assume a regenerator size, consider
it
as
a rating problem, and evaluate the performance as outlined for compact recuperators. Iterate
on
the size until the computed performance matches the specified performance.
A
detailed
sizing procedure is outline in reference 14.
7 MECHANICAL DESIGN
After the heat-transfere surface has been chosen, sizing studies completed, and the regenerator
selected to be compatible with the overall system requirements, the next step involves mechani-
cal design. Mechanical designs must consider items such as [2](1) thermal distortions,
(2)
leakages, (3) pressure loadings, and in the case of the rotary types, (4) a drive system and
(5)
sealing. An important source book on regenerator mechanical design is Mondt
[2].
7.1 Single-Bed and Dual-Bed Fixed Regenerators
Single-bed and dual-bed regenerators can be relatively simple to design. If the bed is composed
of loose pellets, grids or screens are necessary to retain the pellets within a container. The grid