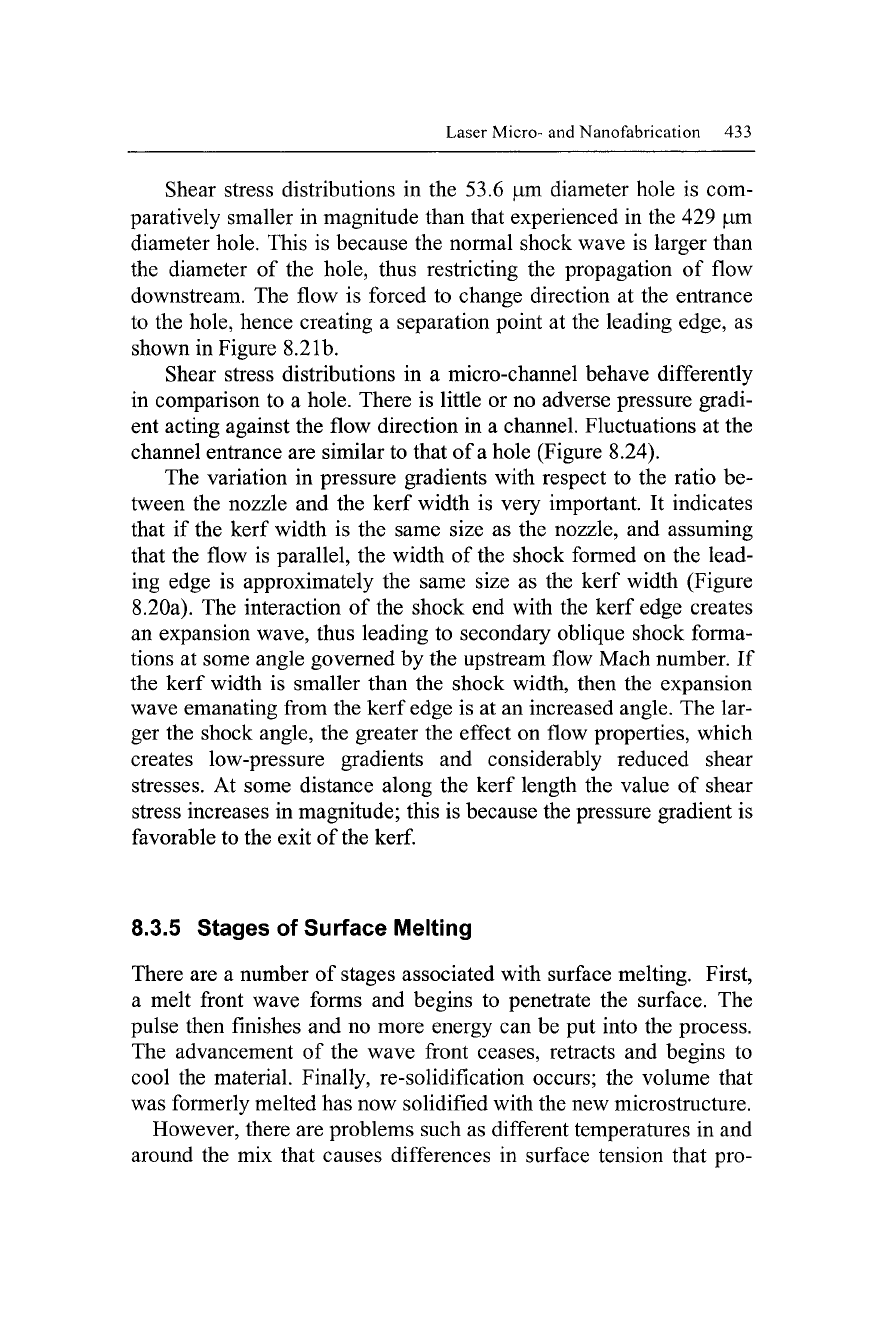
Laser Micro- and Nanofabrication 433
Shear stress distributions in the 53.6 |Lim diameter hole is com-
paratively smaller in magnitude than that experienced in the 429 |Lim
diameter hole. This is because the normal shock wave is larger than
the diameter of the hole, thus restricting the propagation of flow
downstream. The flow is forced to change direction at the entrance
to the hole, hence creating a separation point at the leading edge, as
shown in Figure 8.21b.
Shear stress distributions in a micro-channel behave differently
in comparison to a hole. There is little or no adverse pressure gradi-
ent acting against the flow direction in a channel. Fluctuations at the
channel entrance are similar to that of
a
hole (Figure 8.24).
The variation in pressure gradients with respect to the ratio be-
tween the nozzle and the kerf width is very important. It indicates
that if the kerf width is the same size as the nozzle, and assuming
that the flow is parallel, the width of the shock formed on the lead-
ing edge is approximately the same size as the kerf width (Figure
8.20a). The interaction of the shock end with the kerf edge creates
an expansion wave, thus leading to secondary oblique shock forma-
tions at some angle governed by the upstream flow Mach number. If
the kerf width is smaller than the shock width, then the expansion
wave emanating from the kerf edge is at an increased angle. The lar-
ger the shock angle, the greater the effect on flow properties, which
creates low-pressure gradients and considerably reduced shear
stresses. At some distance along the kerf length the value of shear
stress increases in magnitude; this is because the pressure gradient is
favorable to the exit of
the
kerf.
8.3.5 Stages of Surface Melting
There are a number of stages associated with surface melting. First,
a melt front wave forms and begins to penetrate the surface. The
pulse then finishes and no more energy can be put into the process.
The advancement of the wave front ceases, retracts and begins to
cool the material. Finally, re-solidification occurs; the volume that
was formerly melted has now solidified with the new microstructure.
However, there are problems such as different temperatures in and
around the mix that causes differences in surface tension that pro-