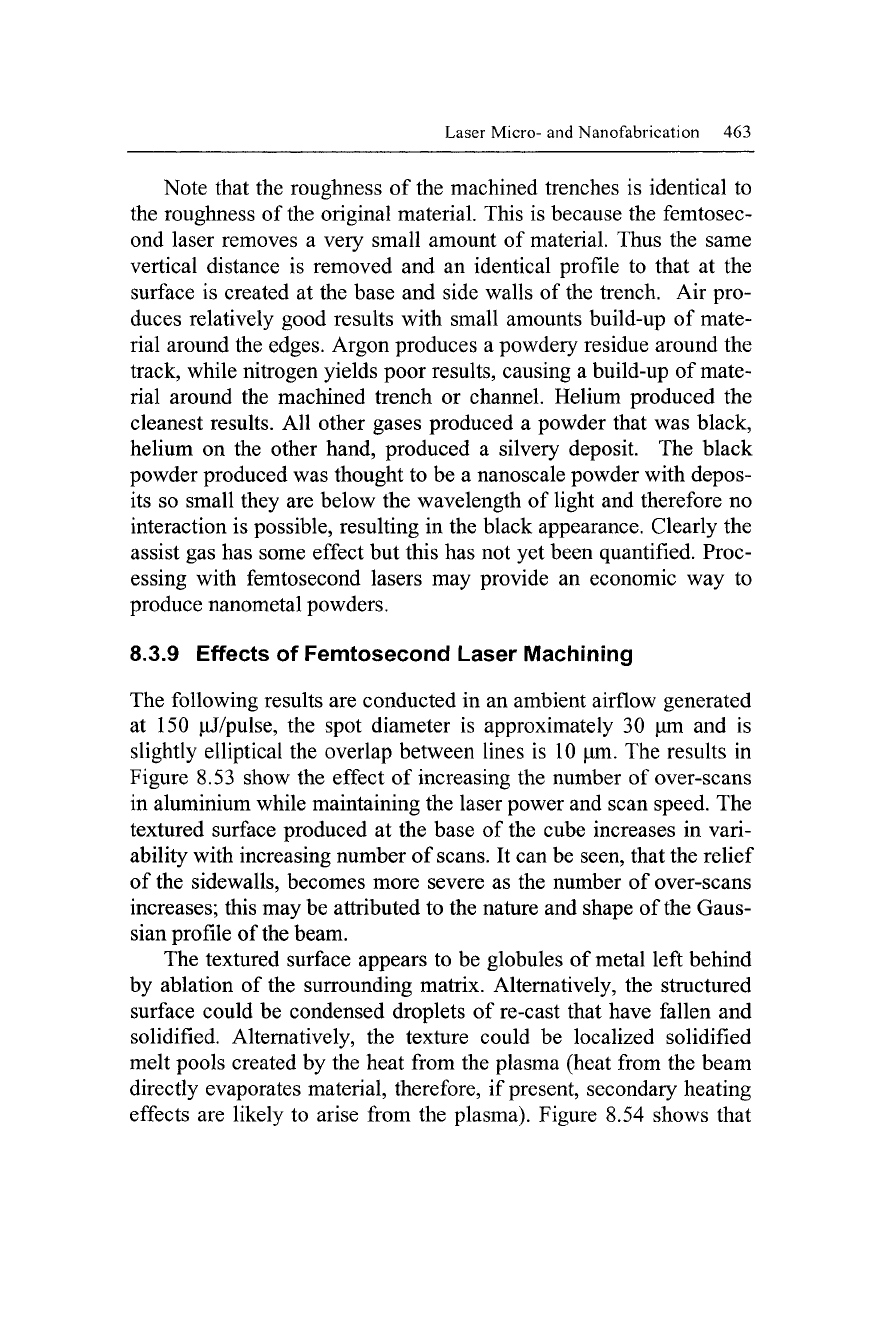
Laser Micro- and Nanofabrication 463
Note that the roughness of the machined trenches is identical to
the roughness of the original material. This is because the femtosec-
ond laser removes a very small amount of material. Thus the same
vertical distance is removed and an identical profile to that at the
surface is created at the base and side walls of the trench. Air pro-
duces relatively good results with small amounts build-up of mate-
rial around the edges. Argon produces a powdery residue around the
track, while nitrogen yields poor results, causing a build-up of mate-
rial around the machined trench or channel. Helium produced the
cleanest results. All other gases produced a powder that was black,
helium on the other hand, produced a silvery deposit. The black
powder produced was thought to be a nanoscale powder with depos-
its so small they are below the wavelength of light and therefore no
interaction is possible, resulting in the black appearance. Clearly the
assist gas has some effect but this has not yet been quantified. Proc-
essing with femtosecond lasers may provide an economic way to
produce nanometal powders.
8.3.9 Effects of Femtosecond Laser Machining
The following results are conducted in an ambient airflow generated
at 150 |LJ/pulse, the spot diameter is approximately 30 |Lim and is
slightly elliptical the overlap between lines is 10 |Lim. The results in
Figure 8.53 show the effect of increasing the number of over-scans
in aluminium while maintaining the laser power and scan speed. The
textured surface produced at the base of the cube increases in vari-
ability with increasing number of
scans.
It can be seen, that the relief
of the sidewalls, becomes more severe as the number of over-scans
increases; this may be attributed to the nature and shape of the Gaus-
sian profile of the beam.
The textured surface appears to be globules of metal left behind
by ablation of the surrounding matrix. Alternatively, the structured
surface could be condensed droplets of re-cast that have fallen and
solidified. Alternatively, the texture could be localized solidified
melt pools created by the heat from the plasma (heat from the beam
directly evaporates material, therefore, if present, secondary heating
effects are likely to arise from the plasma). Figure 8.54 shows that