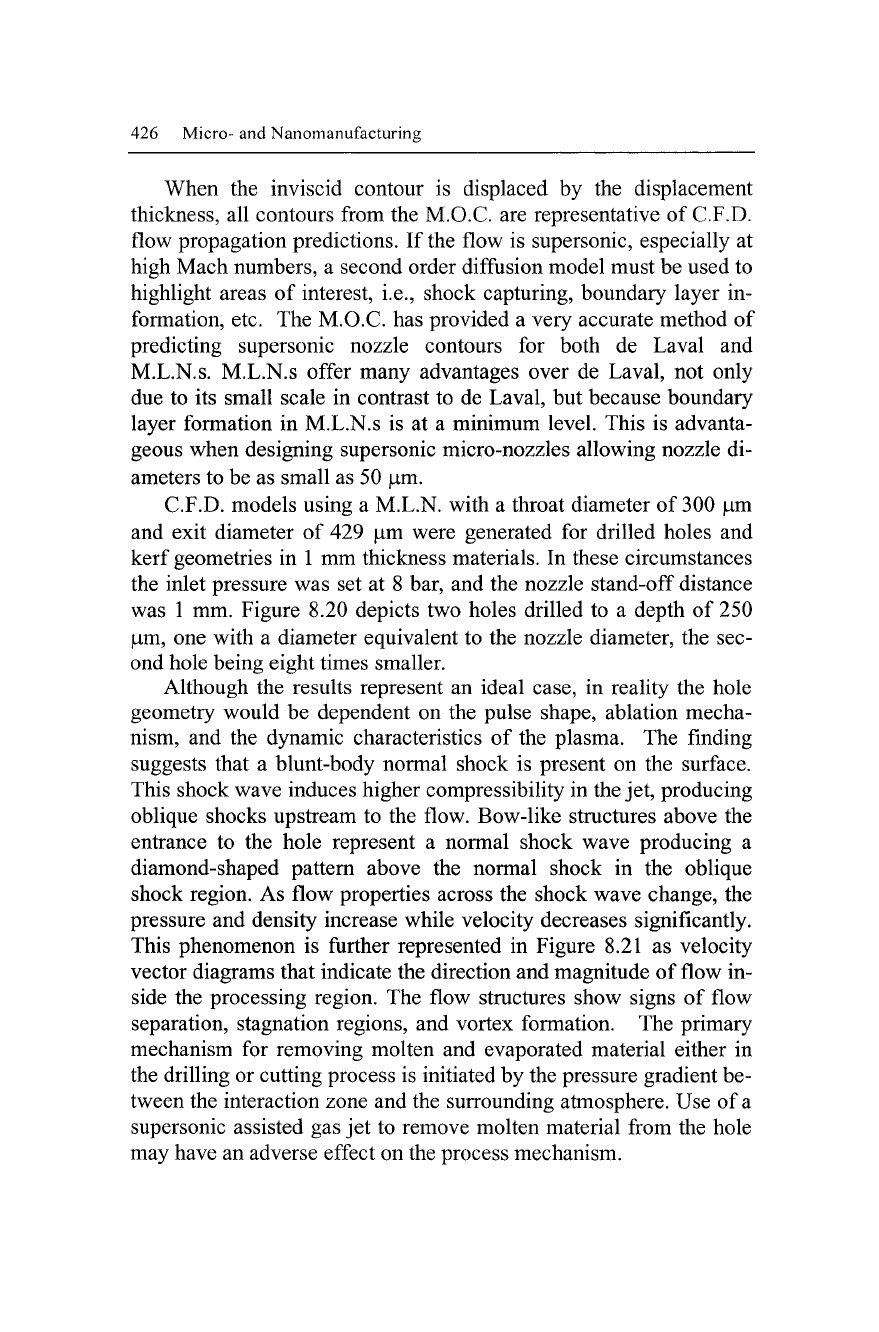
426 Micro- and Nanomanufacturing
When the inviscid contour is displaced by the displacement
thickness, all contours from the M.O.C. are representative of C.F.D.
flow propagation predictions. If the flow is supersonic, especially at
high Mach numbers, a second order diffusion model must be used to
highlight areas of interest, i.e., shock capturing, boundary layer in-
formation, etc. The M.O.C. has provided a very accurate method of
predicting supersonic nozzle contours for both de Laval and
M.L.N.s. M.L.N.s offer many advantages over de Laval, not only
due to its small scale in contrast to de Laval, but because boundary
layer formation in M.L.N.s is at a minimum level. This is advanta-
geous when designing supersonic micro-nozzles allowing nozzle di-
ameters to be as small as 50 |Lim.
C.F.D. models using a M.L.N, with a throat diameter of 300 |Lim
and exit diameter of 429 |Lim were generated for drilled holes and
kerf geometries in 1 mm thickness materials. In these circumstances
the inlet pressure was set at 8 bar, and the nozzle stand-off distance
was 1 mm. Figure 8.20 depicts two holes drilled to a depth of 250
|um, one with a diameter equivalent to the nozzle diameter, the sec-
ond hole being eight times smaller.
Although the results represent an ideal case, in reality the hole
geometry would be dependent on the pulse shape, ablation mecha-
nism, and the dynamic characteristics of the plasma. The finding
suggests that a blunt-body normal shock is present on the surface.
This shock wave induces higher compressibility in the jet, producing
oblique shocks upstream to the flow. Bow-like structures above the
entrance to the hole represent a normal shock wave producing a
diamond-shaped pattern above the normal shock in the oblique
shock region. As flow properties across the shock wave change, the
pressure and density increase while velocity decreases significantly.
This phenomenon is further represented in Figure 8.21 as velocity
vector diagrams that indicate the direction and magnitude of flow in-
side the processing region. The flow structures show signs of flow
separation, stagnation regions, and vortex formation. The primary
mechanism for removing molten and evaporated material either in
the drilling or cutting process is initiated by the pressure gradient be-
tween the interaction zone and the surrounding atmosphere. Use of
a
supersonic assisted gas jet to remove molten material from the hole
may have an adverse effect on the process mechanism.