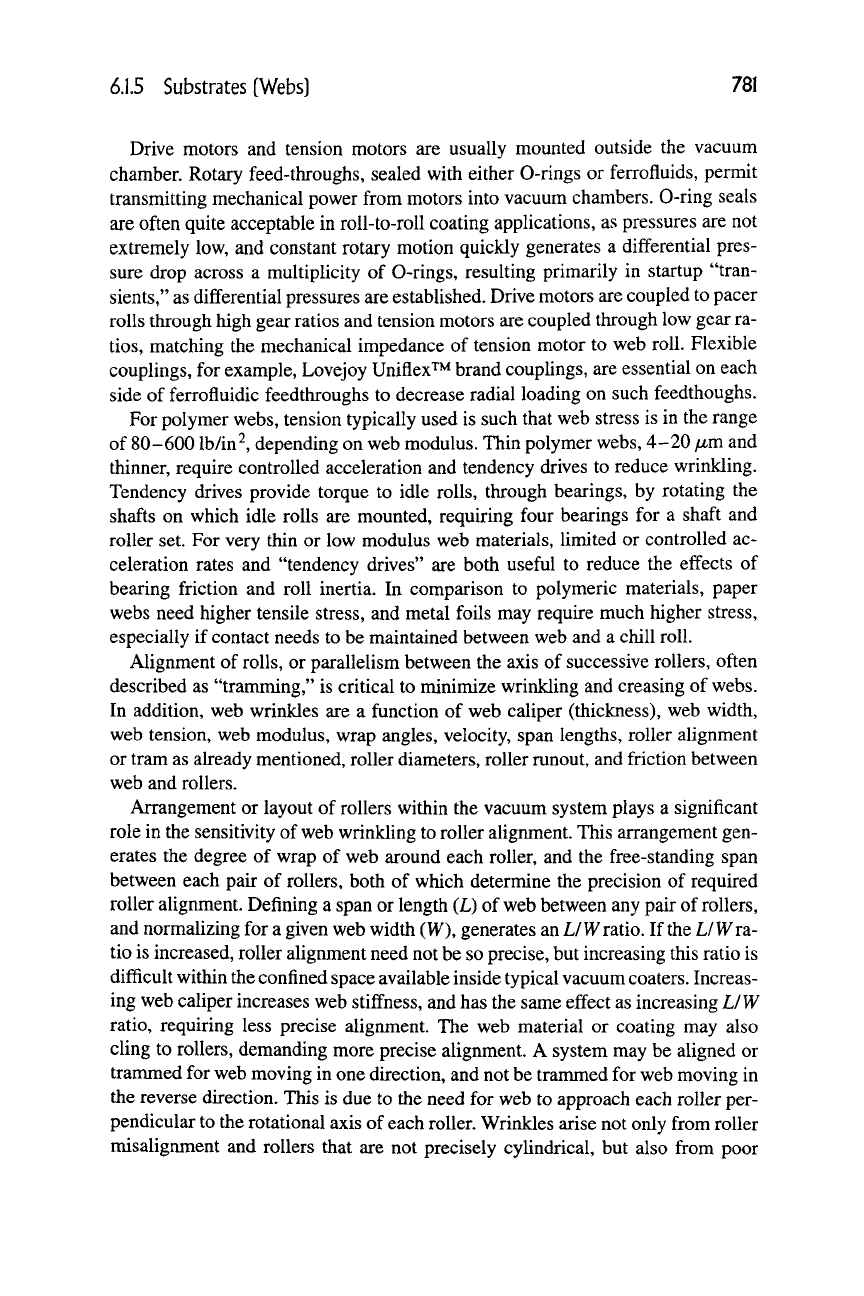
6.1.5
Substrates [Webs]
781
Drive motors and tension motors are usually mounted outside the vacuum
chamber. Rotary feed-throughs, sealed with either 0-rings or ferrofluids, permit
transmitting mechanical power from motors into vacuum chambers. 0-ring seals
are often quite acceptable in roll-to-roll coating applications, as pressures are not
extremely low, and constant rotary motion quickly generates a differential pres-
sure drop across a multiplicity of 0-rings, resulting primarily in startup "tran-
sients,"
as differential pressures are established. Drive motors are coupled to pacer
rolls through high gear ratios and tension motors are coupled through low gear ra-
tios,
matching the mechanical impedance of tension motor to web roll. Flexible
couplings, for example, Lovejoy Uniflex^^ brand couplings, are essential on each
side of ferrofluidic feedthroughs to decrease radial loading on such feedthoughs.
For polymer webs, tension typically used is such that web stress is in the range
of 80-600 lb/in^, depending on web modulus. Thin polymer webs, 4-20
jmrn
and
thinner, require controlled acceleration and tendency drives to reduce wrinkling.
Tendency drives provide torque to idle rolls, through bearings, by rotating the
shafts on which idle rolls are mounted, requiring four bearings for a shaft and
roller set. For very thin or low modulus web materials, limited or controlled ac-
celeration rates and "tendency drives" are both useful to reduce the effects of
bearing friction and roll inertia. In comparison to polymeric materials, paper
webs need higher tensile stress, and metal foils may require much higher stress,
especially if contact needs to be maintained between web and a chill roll.
Alignment of rolls, or parallelism between the axis of successive rollers, often
described as "tramming," is critical to minimize wrinkling and creasing of webs.
In addition, web wrinkles are a function of web caliper (thickness), web width,
web tension, web modulus, wrap angles, velocity, span lengths, roller alignment
or tram as already mentioned, roller diameters, roller runout, and friction between
web and rollers.
Arrangement or layout of rollers within the vacuum system plays a significant
role in the sensitivity of
web
wrinkling to roller alignment. This arrangement gen-
erates the degree of wrap of web around each roller, and the free-standing span
between each pair of rollers, both of which determine the precision of required
roller alignment. Defining a span or length (L) of web between any pair of rollers,
and normalizing for a given web width (W), generates an L/Wiaiio. If
the
L/Vi^ra-
tio is increased, roller alignment need not be so precise, but increasing this ratio is
difficult within the confined space available inside typical vacuum
coaters.
Increas-
ing web caliper increases web stiffness, and has the same effect as increasing L/W
ratio,
requiring less precise alignment. The web material or coating may also
cling to rollers, demanding more precise alignment. A system may be aligned or
tranuned for web moving in one direction, and not be tranuned for web moving in
the reverse direction. This is due to the need for web to approach each roller per-
pendicular to the rotational axis of each roller. Wrinkles arise not only from roller
misalignment and rollers that are not precisely cylindrical, but also from poor