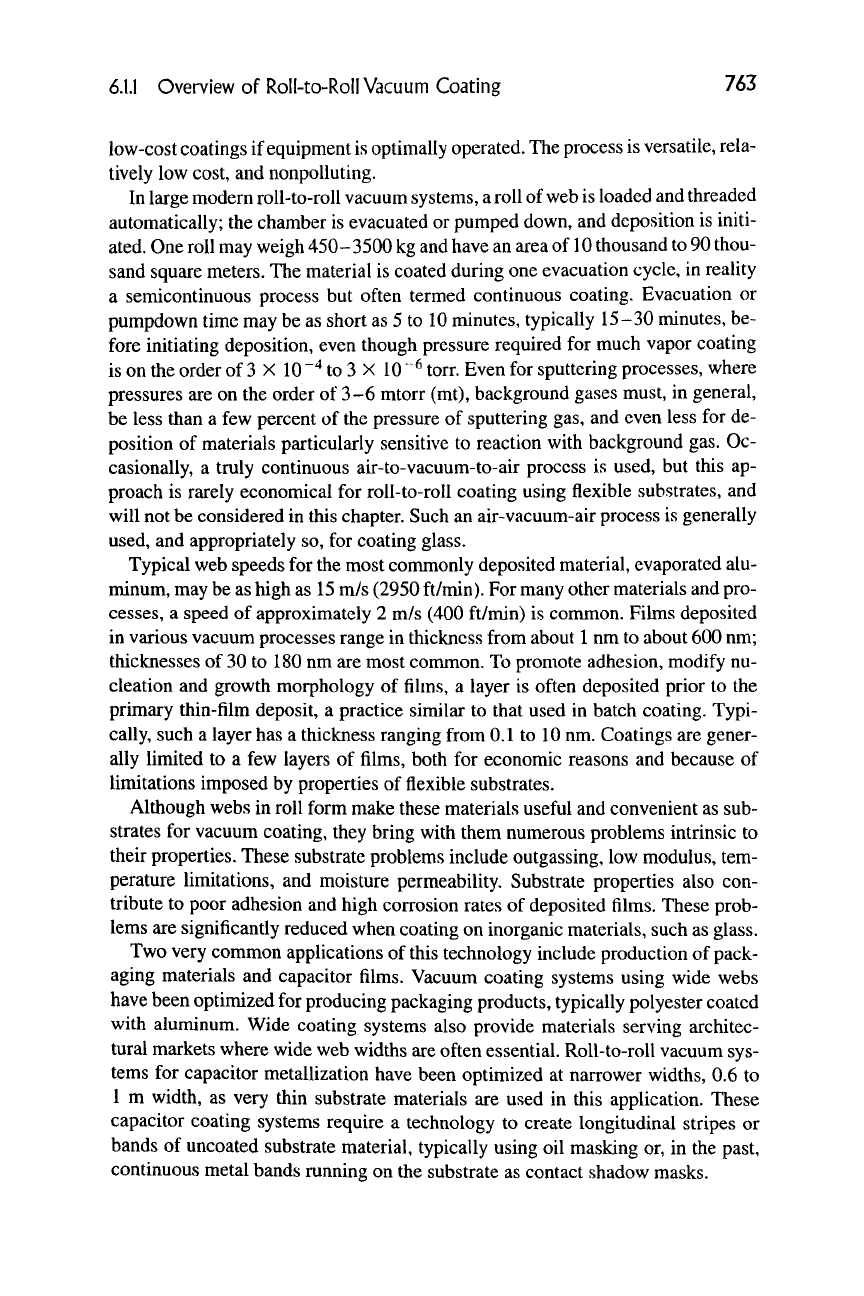
6.1.1 Overview of Roll-to-Roll Vacuum Coating 763
low-cost coatings if equipment
is
optimally operated. The process is versatile, rela-
tively low cost, and nonpolluting.
In large modern roll-to-roll vacuum systems,
a
roll of web is loaded and threaded
automatically; the chamber is evacuated or pumped down, and deposition is initi-
ated. One roll may weigh 450-3500 kg and have an area of
10
thousand to 90 thou-
sand square meters. The material is coated during one evacuation cycle, in reality
a semicontinuous process but often termed continuous coating. Evacuation or
pumpdown time may be as short as 5 to 10 minutes, typically 15-30 minutes, be-
fore initiating deposition, even though pressure required for much vapor coating
is on the order of
3
X
10
"^ to 3 X 10 ^ torr. Even for sputtering processes, where
pressures are on the order of 3-6 mtorr (mt), background gases must, in general,
be less than a few percent of the pressure of sputtering gas, and even less for de-
position of materials particularly sensitive to reaction with background gas. Oc-
casionally, a truly continuous air-to-vacuum-to-air process is used, but this ap-
proach is rarely economical for roll-to-roll coating using flexible substrates, and
will not be considered in this chapter. Such an air-vacuum-air process is generally
used, and appropriately so, for coating glass.
Typical web speeds for the most commonly deposited material, evaporated alu-
minum, may be as high as 15 m/s (2950 ft/min). For many other materials and pro-
cesses, a speed of approximately 2 m/s (400 ft/min) is common. Films deposited
in various vacuum processes range in thickness from about
1
nm to about 600 nm;
thicknesses of 30 to 180 nm are most common. To promote adhesion, modify nu-
cleation and growth morphology of films, a layer is often deposited prior to the
primary thin-film deposit, a practice similar to that used in batch coating. Typi-
cally, such a layer has a thickness ranging from 0.1 to 10 nm. Coatings are gener-
ally limited to a few layers of films, both for economic reasons and because of
limitations imposed by properties of flexible substrates.
Although webs in roll form make these materials useful and convenient as sub-
strates for vacuum coating, they bring with them numerous problems intrinsic to
their properties. These substrate problems include outgassing, low modulus, tem-
perature limitations, and moisture permeability. Substrate properties also con-
tribute to poor adhesion and high corrosion rates of deposited films. These prob-
lems are significantly reduced when coating on inorganic materials, such as glass.
Two very common applications of this technology include production of pack-
aging materials and capacitor films. Vacuum coating systems using wide webs
have been optimized for producing packaging products, typically polyester coated
with aluminum. Wide coating systems also provide materials serving architec-
tural markets where wide web widths are often essential. Roll-to-roll vacuum sys-
tems for capacitor metallization have been optimized at narrower widths, 0.6 to
1 m width, as very thin substrate materials are used in this application. These
capacitor coating systems require a technology to create longitudinal stripes or
bands of uncoated substrate material, typically using oil masking or, in the past,
continuous metal bands running on the substrate as contact shadow masks.