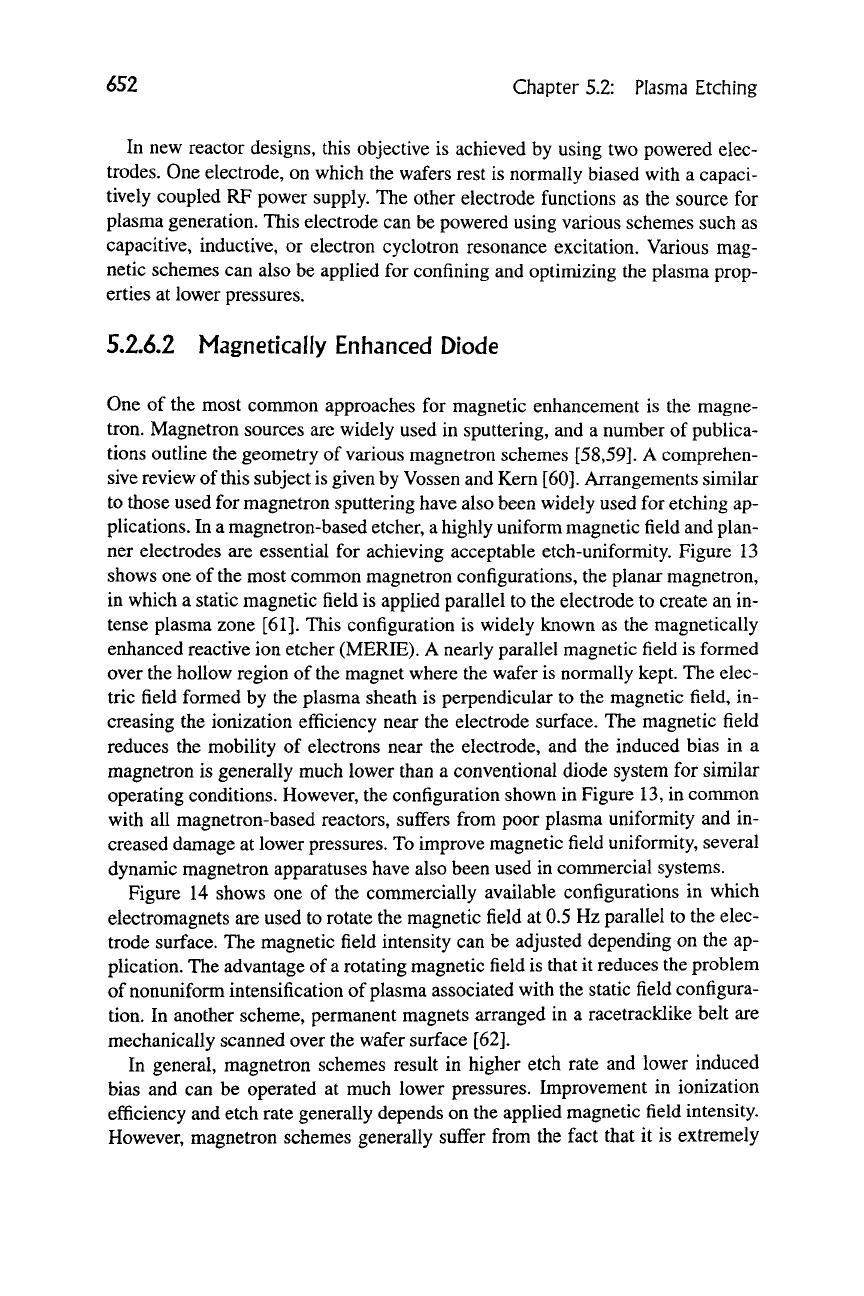
652 Chapter 5.2: Plasma Etching
In new reactor designs, this objective is achieved by using two powered elec-
trodes. One electrode, on which the wafers rest is normally biased with a capaci-
tively coupled RP power supply. The other electrode functions as the source for
plasma generation. This electrode can be powered using various schemes such as
capacitive, inductive, or electron cyclotron resonance excitation. Various mag-
netic schemes can also be applied for confining and optimizing the plasma prop-
erties at lower pressures.
5.2.6.2 Magnetically Enhanced Diode
One of the most common approaches for magnetic enhancement is the magne-
tron. Magnetron sources are widely used in sputtering, and a number of publica-
tions outline the geometry of various magnetron schemes [58,59]. A comprehen-
sive review of
this
subject is given by Vossen and Kern [60]. Arrangements similar
to those used for magnetron sputtering have also been widely used for etching ap-
plications. In a magnetron-based etcher, a highly uniform magnetic field and plan-
ner electrodes are essential for achieving acceptable etch-uniformity. Figure 13
shows one of the most common magnetron configurations, the planar magnetron,
in which a static magnetic field is applied parallel to the electrode to create an in-
tense plasma zone [61]. This configuration is widely known as the magnetically
enhanced reactive ion etcher (MERIE). A nearly parallel magnetic field is formed
over the hollow region of the magnet where the wafer is normally kept. The elec-
tric field formed by the plasma sheath is perpendicular to the magnetic field, in-
creasing the ionization efficiency near the electrode surface. The magnetic field
reduces the mobility of electrons near the electrode, and the induced bias in a
magnetron is generally much lower than a conventional diode system for similar
operating conditions. However, the configuration shown in Figure
13,
in conunon
with all magnetron-based reactors, suffers from poor plasma uniformity and in-
creased damage at lower pressures. To improve magnetic field uniformity, several
dynamic magnetron apparatuses have also been used in commercial systems.
Figure 14 shows one of the commercially available configurations in which
electromagnets are used to rotate the magnetic field at 0.5 Hz parallel to the elec-
trode surface. The magnetic field intensity can be adjusted depending on the ap-
plication. The advantage of
a
rotating magnetic field is that it reduces the problem
of nonuniform intensification of plasma associated with the static field configura-
tion. In another scheme, permanent magnets arranged in a racetracklike belt are
mechanically scanned over the wafer surface [62].
In general, magnetron schemes result in higher etch rate and lower induced
bias and can be operated at much lower pressures. Improvement in ionization
efficiency and etch rate generally depends on the applied magnetic field intensity.
However, magnetron schemes generally suffer from the fact that it is extremely