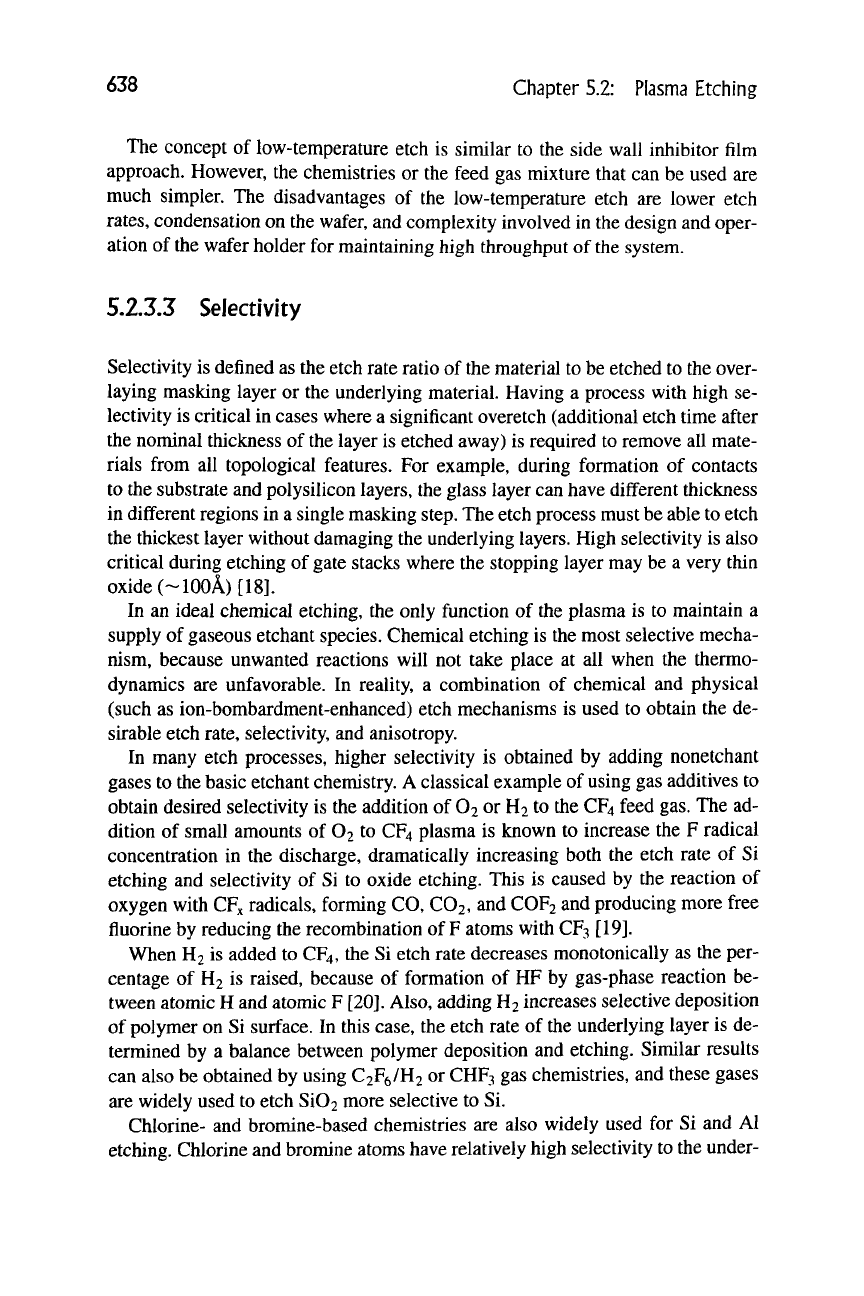
638 Chapter 5.2: Plasma Etching
The concept of low-temperature etch is similar to the side wall inhibitor film
approach. However, the chemistries or the feed gas mixture that can be used are
much simpler. The disadvantages of the low-temperature etch are lower etch
rates,
condensation on the wafer, and complexity involved in the design and oper-
ation of the wafer holder for maintaining high throughput of the system.
5.233 Selectivity
Selectivity is defined as the etch rate ratio of the material to be etched to the over-
laying masking layer or the underlying material. Having a process with high se-
lectivity is critical in cases where a significant overetch (additional etch time after
the nominal thickness of the layer is etched away) is required to remove all mate-
rials from all topological features. For example, during formation of contacts
to the substrate and polysilicon layers, the glass layer can have different thickness
in different regions in a single masking step. The etch process must be able to etch
the thickest layer without damaging the underlying layers. High selectivity is also
critical during etching of gate stacks where the stopping layer may be a very thin
oxide (~100A) [18].
In an ideal chemical etching, the only function of the plasma is to maintain a
supply of gaseous etchant species. Chemical etching is the most selective mecha-
nism, because unwanted reactions will not take place at all when the thermo-
dynamics are unfavorable. In reality, a combination of chemical and physical
(such as ion-bombardment-enhanced) etch mechanisms is used to obtain the de-
sirable etch rate, selectivity, and anisotropy.
In many etch processes, higher selectivity is obtained by adding nonetchant
gases to the basic etchant chemistry. A classical example of using gas additives to
obtain desired selectivity is the addition of
O2
or H2 to the CF4 feed gas. The ad-
dition of small amounts of O2 to CF4 plasma is known to increase the F radical
concentration in the discharge, dramatically increasing both the etch rate of Si
etching and selectivity of Si to oxide etching. This is caused by the reaction of
oxygen with CFx radicals, forming CO, CO2, and COF2 and producing more free
fluorine by reducing the recombination of F atoms with
CF3
[19].
When H2 is added to CF4, the Si etch rate decreases monotonically as the per-
centage of H2 is raised, because of formation of HF by gas-phase reaction be-
tween atomic H and atomic F
[20].
Also, adding H2 increases selective deposition
of polymer on Si surface. In this case, the etch rate of the underlying layer is de-
termined by a balance between polymer deposition and etching. Similar results
can also be obtained by using C2F6/H2 or CHF3 gas chemistries, and these gases
are widely used to etch Si02 more selective to Si.
Chlorine- and bromine-based chemistries are also widely used for Si and Al
etching. Chlorine and bromine atoms have relatively high selectivity to the under-