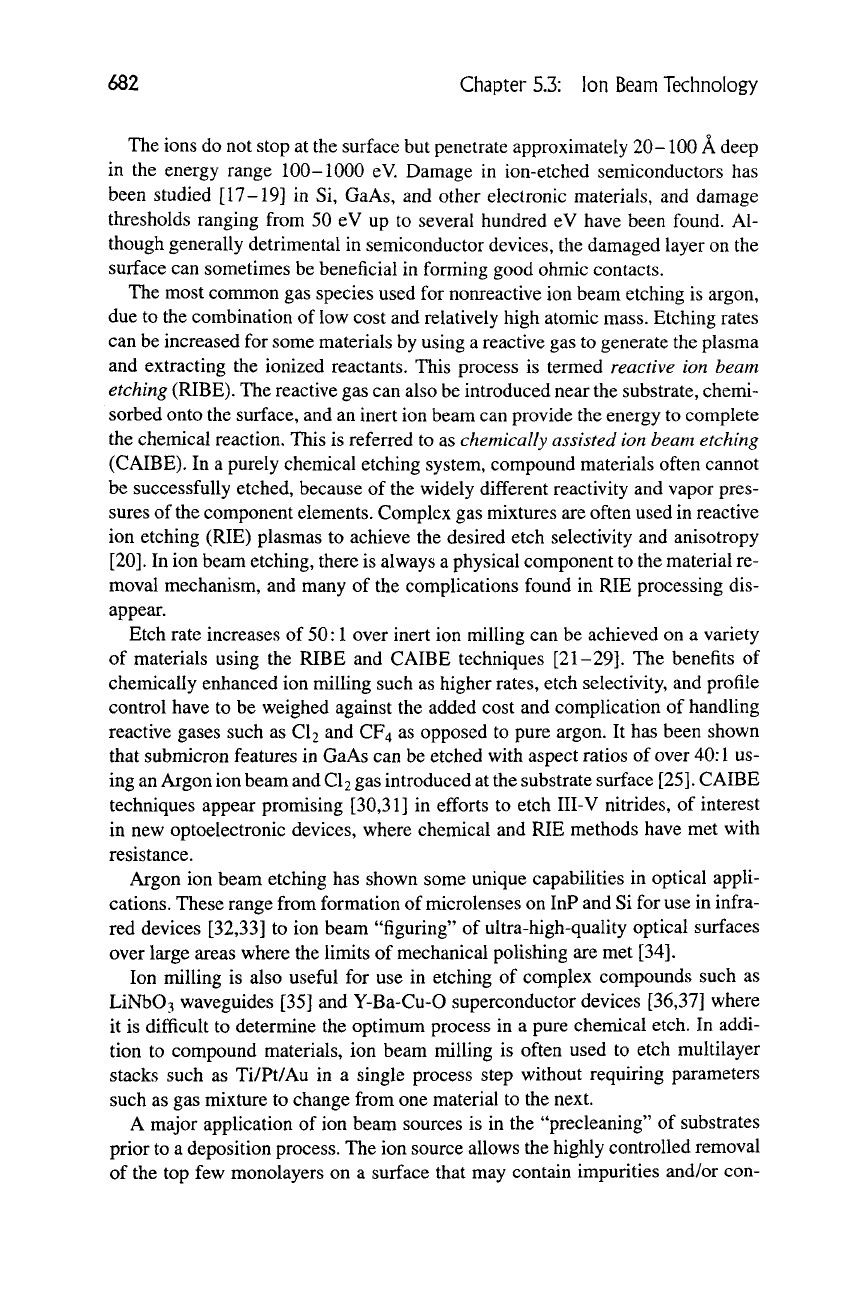
682 Chapter 5.3: Ion
Beam
Technology
The ions do not stop at the surface but penetrate approximately 20-100 A deep
in the energy range 100-1000 eV. Damage in ion-etched semiconductors has
been studied [17-19] in Si, GaAs, and other electronic materials, and damage
thresholds ranging from 50 eV up to several hundred eV have been found. Al-
though generally detrimental in semiconductor devices, the damaged layer on the
surface can sometimes be beneficial in forming good ohmic contacts.
The most common gas species used for nonreactive ion beam etching is argon,
due to the combination of low cost and relatively high atomic mass. Etching rates
can be increased for some materials by using a reactive gas to generate the plasma
and extracting the ionized reactants. This process is termed reactive ion beam
etching (RIBE). The reactive gas can also be introduced near the substrate, chemi-
sorbed onto the surface, and an inert ion beam can provide the energy to complete
the chemical reaction. This is referred to as chemically assisted ion beam etching
(CAIBE). In a purely chemical etching system, compound materials often cannot
be successfully etched, because of the widely different reactivity and vapor pres-
sures of
the
component elements. Complex gas mixtures are often used in reactive
ion etching (RIE) plasmas to achieve the desired etch selectivity and anisotropy
[20].
In ion beam etching, there is always a physical component to the material re-
moval mechanism, and many of the complications found in RIE processing dis-
appear.
Etch rate increases of 50:1 over inert ion milling can be achieved on a variety
of materials using the RIBE and CAIBE techniques [21-29]. The benefits of
chemically enhanced ion milling such as higher rates, etch selectivity, and profile
control have to be weighed against the added cost and complication of handling
reactive gases such as CI2 and CF4 as opposed to pure argon. It has been shown
that submicron features in GaAs can be etched with aspect ratios of over
40:1
us-
ing an Argon ion beam and
CI2
gas introduced at the substrate surface
[25].
CAIBE
techniques appear promising [30,31] in efforts to etch III-V nitrides, of interest
in new optoelectronic devices, where chemical and RIE methods have met with
resistance.
Argon ion beam etching has shown some unique capabilities in optical appli-
cations. These range from formation of microlenses on InP and Si for use in infra-
red devices [32,33] to ion beam "figuring" of ultra-high-quality optical surfaces
over large areas where the limits of mechanical polishing are met [34].
Ion milling is also useful for use in etching of complex compounds such as
LiNbO^ waveguides [35] and Y-Ba-Cu-0 superconductor devices [36,37] where
it is difficult to determine the optimum process in a pure chemical etch. In addi-
tion to compound materials, ion beam milling is often used to etch multilayer
stacks such as Ti/Pt/Au in a single process step without requiring parameters
such as gas mixture to change from one material to the next.
A major application of ion beam sources is in the "precleaning" of substrates
prior to a deposition process. The ion source allows the highly controlled removal
of the top few monolayers on a surface that may contain impurities and/or con-