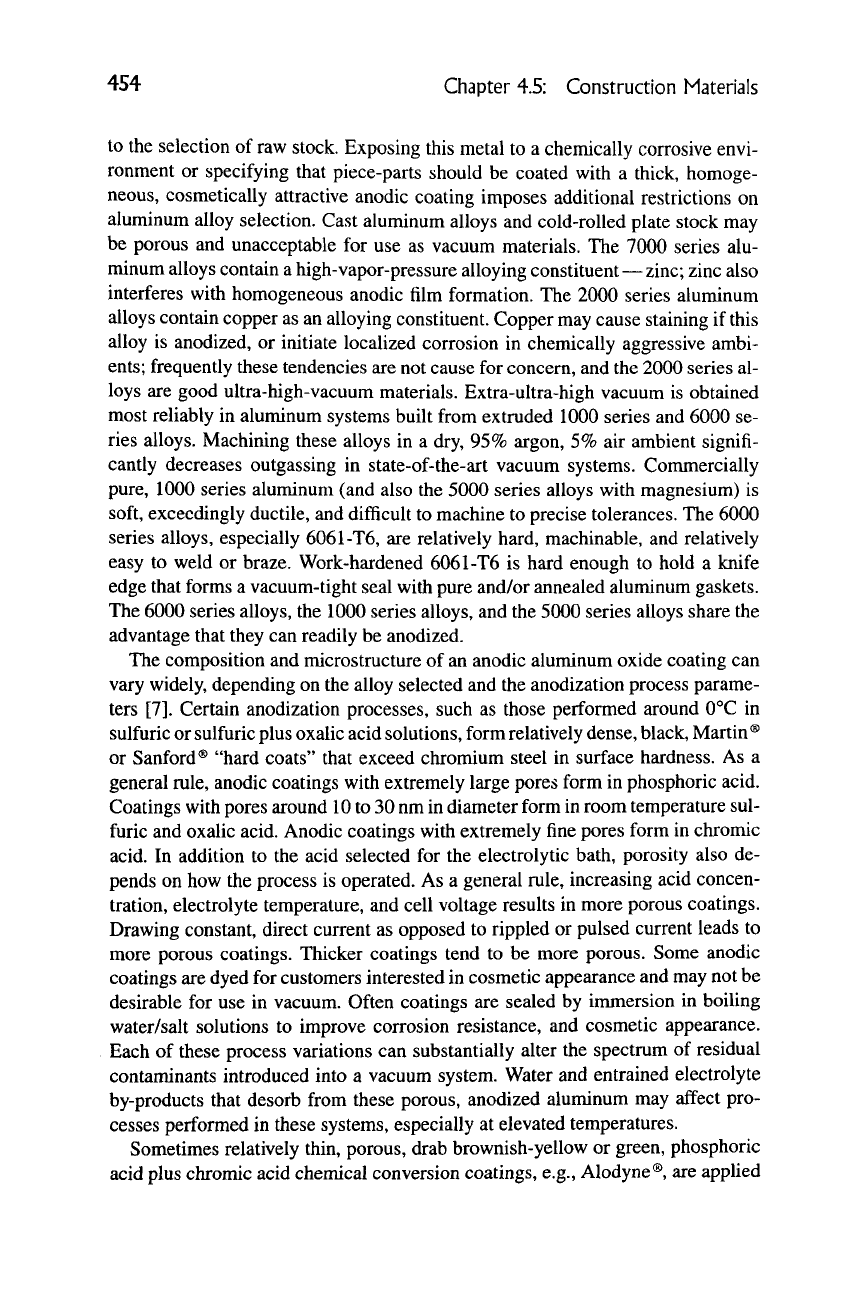
454 Chapter 4.5: Construction Materials
to the selection of raw stock. Exposing this metal to a chemically corrosive envi-
ronment or specifying that piece-parts should be coated with a thick, homoge-
neous,
cosmetically attractive anodic coating imposes additional restrictions on
aluminum alloy selection. Cast aluminum alloys and cold-rolled plate stock may
be porous and unacceptable for use as vacuum materials. The 7000 series alu-
minum alloys contain a high-vapor-pressure alloying constituent—zinc; zinc also
interferes with homogeneous anodic film formation. The 2000 series aluminum
alloys contain copper as an alloying constituent. Copper may cause staining if this
alloy is anodized, or initiate localized corrosion in chemically aggressive ambi-
ents;
frequently these tendencies are not cause for concern, and the 2000 series al-
loys are good ultra-high-vacuum materials. Extra-ultra-high vacuum is obtained
most reliably in aluminum systems built from extruded 1000 series and 6000 se-
ries alloys. Machining these alloys in a dry, 95% argon, 5% air ambient signifi-
cantly decreases outgassing in state-of-the-art vacuum systems. Commercially
pure,
1000 series aluminum (and also the 5000 series alloys with magnesium) is
soft, exceedingly ductile, and difficult to machine to precise tolerances. The 6000
series alloys, especially 6061-T6, are relatively hard, machinable, and relatively
easy to weld or braze. Work-hardened 6061-T6 is hard enough to hold a knife
edge that forms a vacuum-tight seal with pure and/or annealed aluminum gaskets.
The 6000 series alloys, the 1000 series alloys, and the 5000 series alloys share the
advantage that they can readily be anodized.
The composition and microstructure of an anodic aluminum oxide coating can
vary widely, depending on the alloy selected and the anodization process parame-
ters [7]. Certain anodization processes, such as those performed around 0°C in
sulfuric or sulfuric plus oxalic acid solutions, form relatively dense, black, Martin®
or Sanford® "hard coats" that exceed chromium steel in surface hardness. As a
general rule, anodic coatings with extremely large pores form in phosphoric acid.
Coatings with pores around 10 to 30 nm in diameter form in room temperature sul-
furic and oxalic acid. Anodic coatings with extremely fine pores form in chromic
acid. In addition to the acid selected for the electrolytic bath, porosity also de-
pends on how the process is operated. As a general rule, increasing acid concen-
tration, electrolyte temperature, and cell voltage results in more porous coatings.
Drawing constant, direct current as opposed to rippled or pulsed current leads to
more porous coatings. Thicker coatings tend to be more porous. Some anodic
coatings are dyed for customers interested in cosmetic appearance and may not be
desirable for use in vacuum. Often coatings are sealed by immersion in boiling
water/salt solutions to improve corrosion resistance, and cosmetic appearance.
Each of these process variations can substantially alter the spectrum of residual
contaminants introduced into a vacuum system. Water and entrained electrolyte
by-products that desorb from these porous, anodized aluminum may affect pro-
cesses performed in these systems, especially at elevated temperatures.
Sometimes relatively thin, porous, drab brownish-yellow or green, phosphoric
acid plus chromic acid chemical conversion coatings, e.g., Alodyne®, are applied