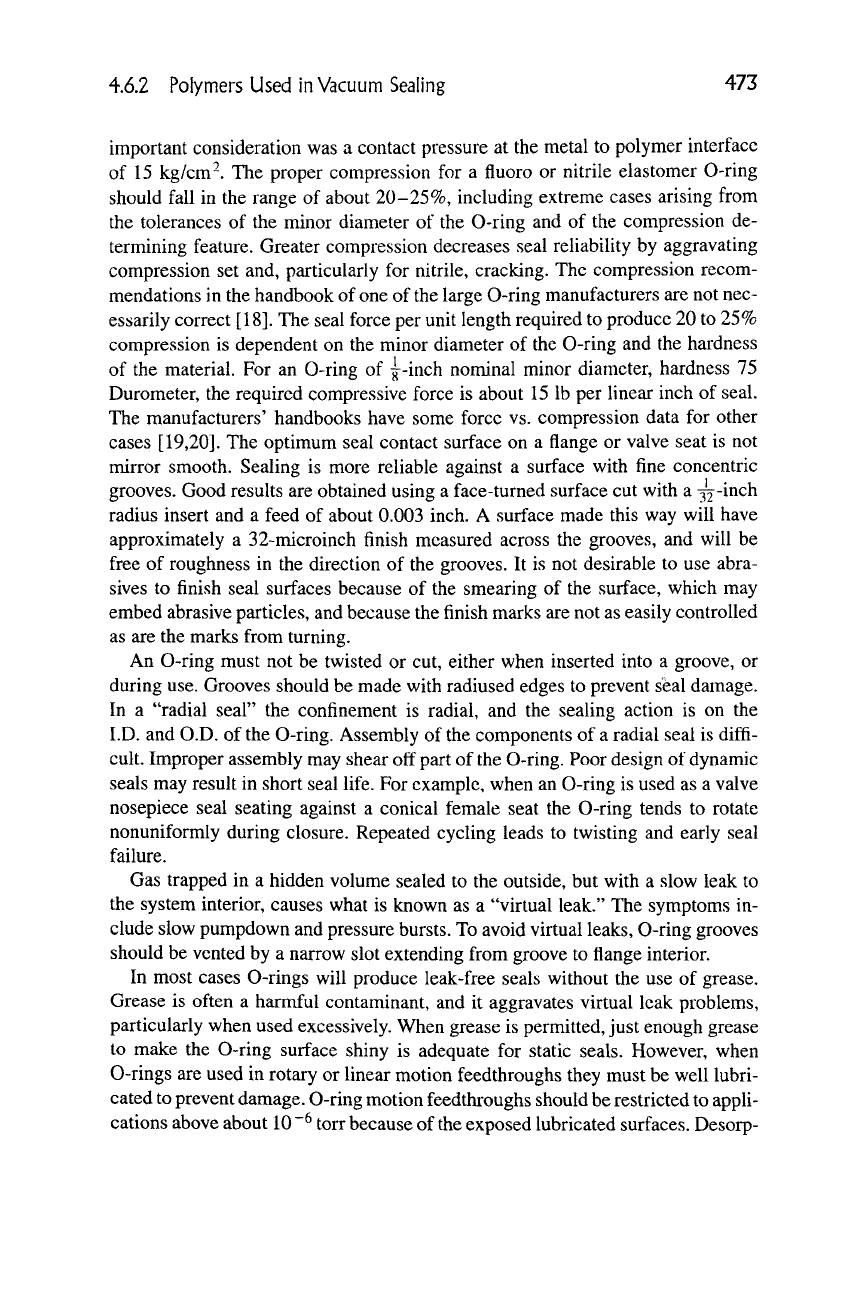
4.6.2 Polymers Used in Vacuum Sealing 473
important consideration was a contact pressure at the metal to polymer interface
of 15 kg/cm-. The proper compression for a fluoro or nitrile elastomer 0-ring
should fall in the range of about 20-25%, including extreme cases arising from
the tolerances of the minor diameter of the 0-ring and of the compression de-
termining feature. Greater compression decreases seal reliability by aggravating
compression set and, particularly for nitrile, cracking. The compression recom-
mendations in the handbook of one of the large 0-ring manufacturers are not nec-
essarily correct
[18].
The seal force per unit length required to produce 20 to 25%
compression is dependent on the minor diameter of the 0-ring and the hardness
of the material. For an 0-ring of -|--inch nominal minor diameter, hardness 75
Durometer, the required compressive force is about 15 lb per linear inch of seal.
The manufacturers' handbooks have some force vs. compression data for other
cases [19,20]. The optimum seal contact surface on a flange or valve seat is not
mirror smooth. Sealing is more reliable against a surface with fine concentric
grooves. Good results are obtained using a face-turned surface cut with a ^-inch
radius insert and a feed of about 0.003 inch. A surface made this way will have
approximately a 32-microinch finish measured across the grooves, and will be
free of roughness in the direction of the grooves. It is not desirable to use abra-
sives to finish seal surfaces because of the smearing of the surface, which may
embed abrasive particles, and because the finish marks are not as easily controlled
as are the marks from turning.
An 0-ring must not be twisted or cut, either when inserted into a groove, or
during use. Grooves should be made with radiused edges to prevent seal damage.
In a "radial seal" the confinement is radial, and the sealing action is on the
I.D. and O.D. of the 0-ring. Assembly of the components of a radial seal is diffi-
cult. Improper assembly may shear off part of the 0-ring. Poor design of dynamic
seals may result in short seal life. For example, when an 0-ring is used as a valve
nosepiece seal seating against a conical female seat the 0-ring tends to rotate
nonuniformly during closure. Repeated cycling leads to twisting and early seal
failure.
Gas trapped in a hidden volume sealed to the outside, but with a slow leak to
the system interior, causes what is known as a "virtual leak." The symptoms in-
clude slow pumpdown and pressure bursts. To avoid virtual leaks, 0-ring grooves
should be vented by a narrow slot extending from groove to flange interior.
In most cases 0-rings will produce leak-free seals without the use of grease.
Grease is often a harmful contaminant, and it aggravates virtual leak problems,
particularly when used excessively. When grease is permitted, just enough grease
to make the O-ring surface shiny is adequate for static seals. However, when
0-rings are used in rotary or linear motion feedthroughs they must be well lubri-
cated to prevent
damage.
0-ring motion feedthroughs should be restricted to appli-
cations above about
10
"^ torr because of
the
exposed lubricated surfaces. Desorp-