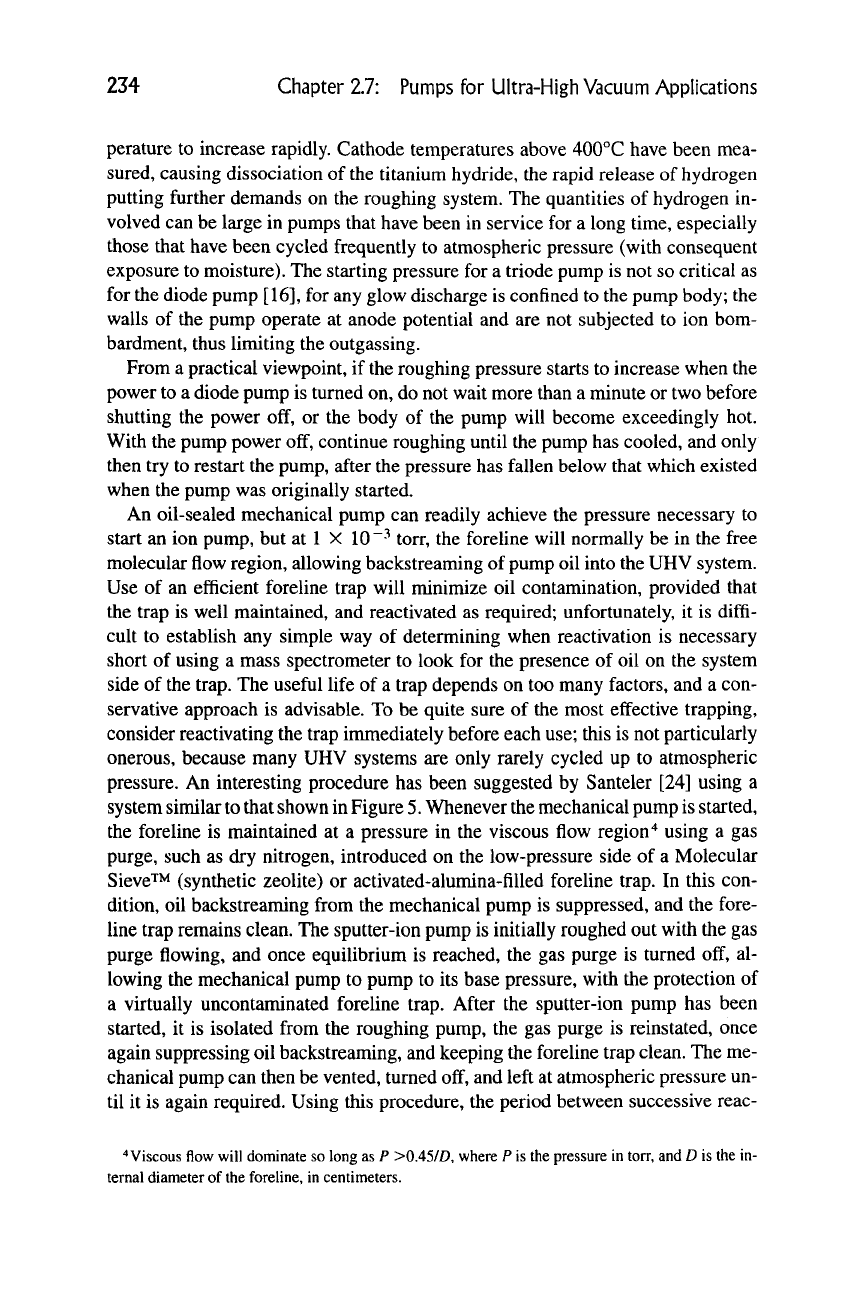
234 Chapter 2.7: Pumps for Ultra-High Vacuum Applications
perature to increase rapidly. Cathode temperatures above 400°C have been mea-
sured, causing dissociation of the titanium hydride, the rapid release of hydrogen
putting further demands on the roughing system. The quantities of hydrogen in-
volved can be large in pumps that have been in service for a long time, especially
those that have been cycled frequently to atmospheric pressure (with consequent
exposure to moisture). The starting pressure for a triode pump is not so critical as
for the diode pump [16], for any glow discharge is confined to the pump body; the
walls of the pump operate at anode potential and are not subjected to ion bom-
bardment, thus limiting the outgassing.
From a practical viewpoint, if the roughing pressure starts to increase when the
power to a diode pump is turned on, do not wait more than a minute or two before
shutting the power off, or the body of the pump will become exceedingly hot.
With the pump power off, continue roughing until the pump has cooled, and only
then try to restart the pump, after the pressure has fallen below that which existed
when the pump was originally started.
An oil-sealed mechanical pump can readily achieve the pressure necessary to
start an ion pump, but at 1 X
10 ~^
torr, the foreline will normally be in the free
molecular flow region, allowing backstreaming of pump oil into the UHV system.
Use of an efficient foreline trap will minimize oil contamination, provided that
the trap is well maintained, and reactivated as required; unfortunately, it is diffi-
cult to establish any simple way of determining when reactivation is necessary
short of using a mass spectrometer to look for the presence of oil on the system
side of the trap. The useful life of a trap depends on too many factors, and a con-
servative approach is advisable. To be quite sure of the most effective trapping,
consider reactivating the trap immediately before each use; this is not particularly
onerous, because many UHV systems are only rarely cycled up to atmospheric
pressure. An interesting procedure has been suggested by Santeler [24] using a
system similar
to
that shown in Figure
5.
Whenever the mechanical pump is started,
the foreline is maintained at a pressure in the viscous flow region"^ using a gas
purge, such as dry nitrogen, introduced on the low-pressure side of a Molecular
Sieve^M (synthetic zeolite) or activated-alumina-filled foreline trap. In this con-
dition, oil backstreaming from the mechanical pump is suppressed, and the fore-
line trap remains clean. The sputter-ion pump is initially roughed out with the gas
purge flowing, and once equilibrium is reached, the gas purge is turned off, al-
lowing the mechanical pump to pump to its base pressure, with the protection of
a virtually uncontaminated foreline trap. After the sputter-ion pump has been
started, it is isolated from the roughing pump, the gas purge is reinstated, once
again suppressing oil backstreaming, and keeping the foreline trap clean. The me-
chanical pump can then be vented, turned off, and left at atmospheric pressure un-
til it is again required. Using this procedure, the period between successive reac-
'* Viscous flow will dominate so long as P >0.45/D, where P is the pressure in torr, and D is the in-
ternal diameter of the foreline, in centimeters.