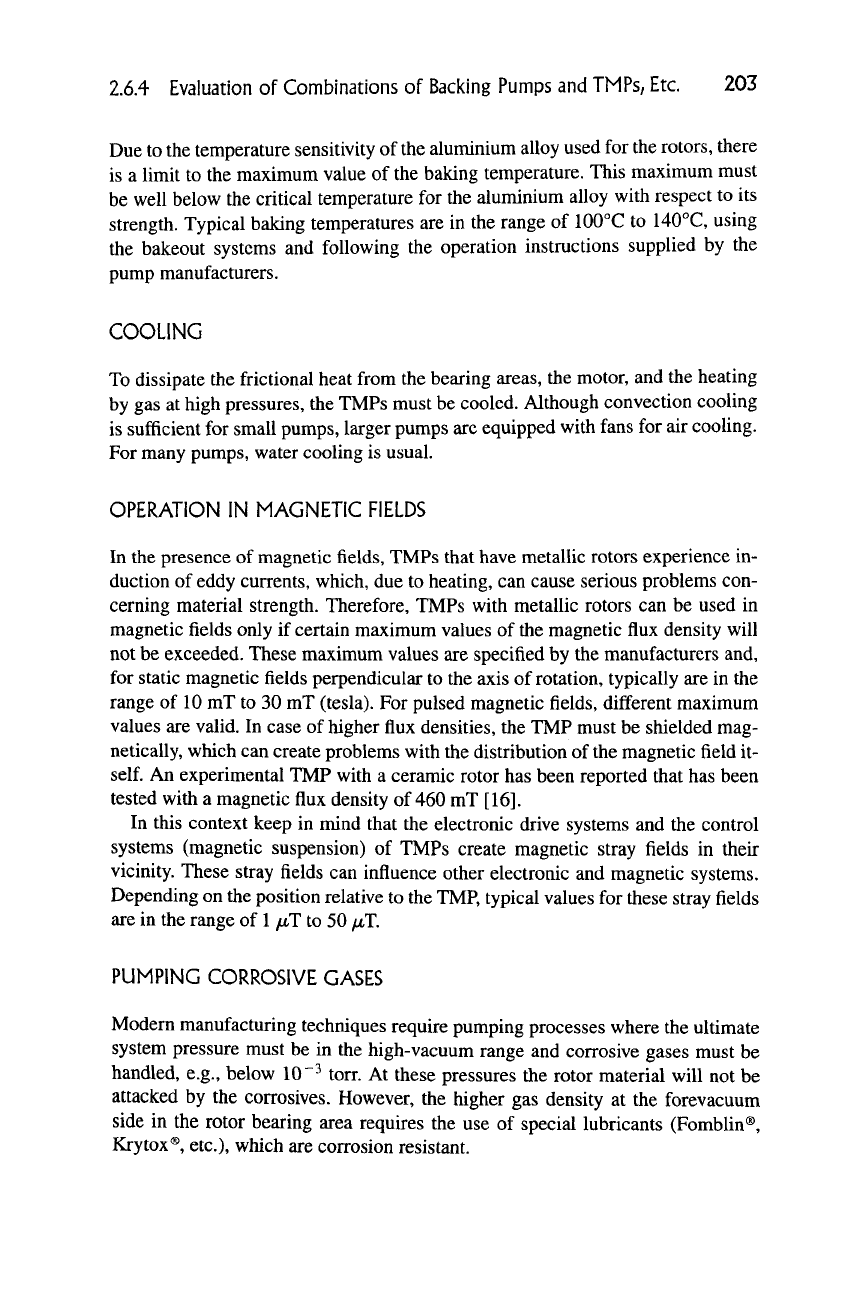
2.6.4 Evaluation of Combinations of Backing Pumps and TMPs, Etc. 203
Due to the temperature sensitivity of
the
aluminium alloy used for the rotors, there
is a limit to the maximum value of the baking temperature. This maximum must
be well below the critical temperature for the aluminium alloy with respect to its
strength. Typical baking temperatures are in the range of 100°C to 140°C, using
the bakeout systems and following the operation instructions supplied by the
pump manufacturers.
COOLING
To dissipate the frictional heat from the bearing areas, the motor, and the heating
by gas at high pressures, the TMPs must be cooled. Although convection cooling
is sufficient for small pumps, larger pumps are equipped with fans for air cooling.
For many pumps, water cooling is usual.
OPERATION IN MAGNETIC FIELDS
In the presence of magnetic fields, TMPs that have metallic rotors experience in-
duction of eddy currents, which, due to heating, can cause serious problems con-
cerning material strength. Therefore, TMPs with metallic rotors can be used in
magnetic fields only if certain maximum values of the magnetic flux density will
not be exceeded. These maximum values are specified by the manufacturers and,
for static magnetic fields perpendicular to the axis of rotation, typically are in the
range of 10 mT to 30 mT (tesla). For pulsed magnetic fields, different maximum
values are valid. In case of higher flux densities, the TMP must be shielded mag-
netically, which can create problems with the distribution of the magnetic field it-
self.
An experimental TMP with a ceramic rotor has been reported that has been
tested with a magnetic flux density of 460 mT [16].
In this context keep in mind that the electronic drive systems and the control
systems (magnetic suspension) of TMPs create magnetic stray fields in their
vicinity. These stray fields can influence other electronic and magnetic systems.
Depending on the position relative to the TMP, typical values for these stray fields
are in the
range
of
1
JULT
to 50
/JLT.
PUMPING CORROSIVE GASES
Modern manufacturing techniques require pumping processes where the ultimate
system pressure must be in the high-vacuum range and corrosive gases must be
handled, e.g., below 10"^ torr. At these pressures the rotor material will not be
attacked by the corrosives. However, the higher gas density at the forevacuum
side in the rotor bearing area requires the use of special lubricants (Fomblin®,
Krytox®, etc.), which are corrosion resistant.