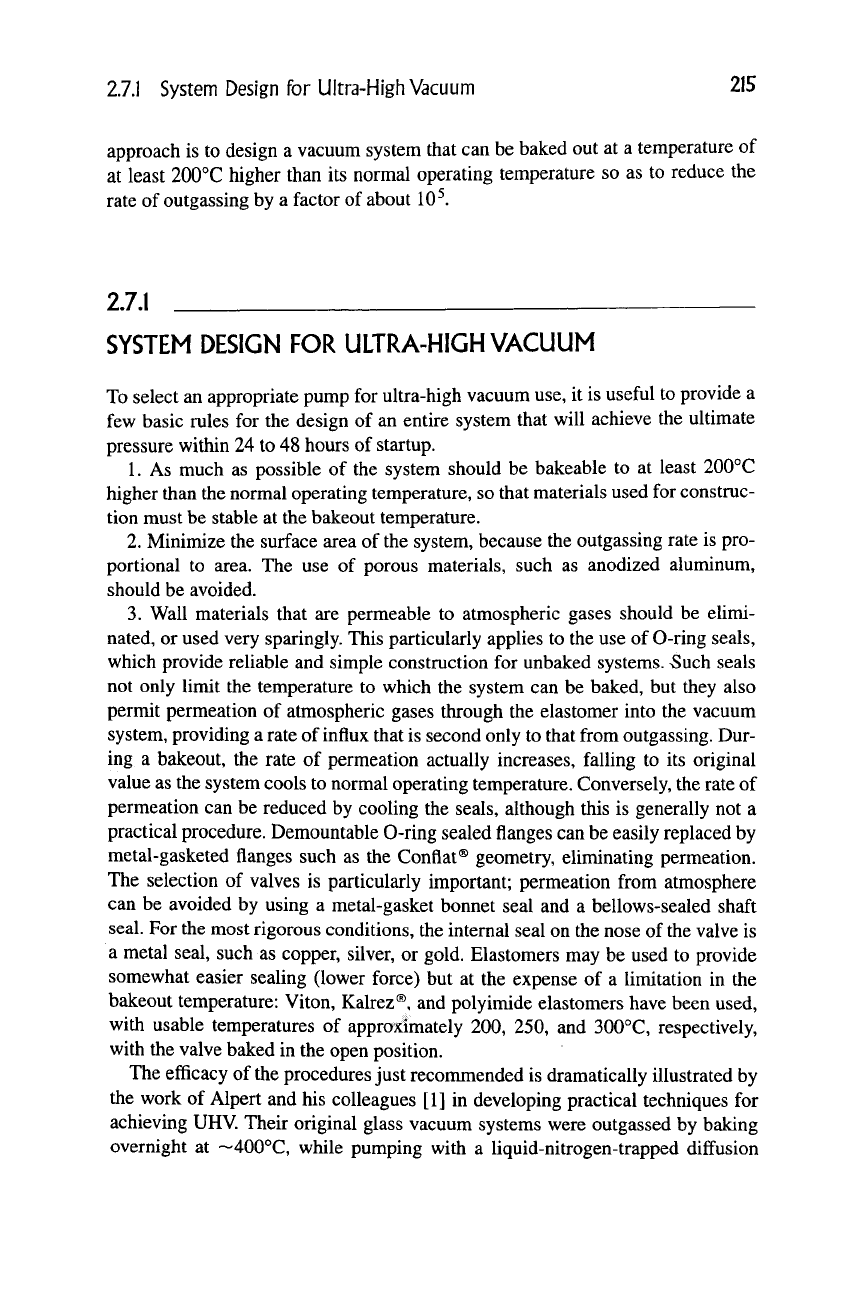
2.7.1 System Design
for
Ultra-High Vacuum
215
approach is to design a vacuum system that can be baked out at a temperature of
at least 200°C higher than its normal operating temperature so as to reduce the
rate of outgassing by a factor of about 10^.
2.7.1
SYSTEM DESIGN FOR ULTRA-HIGH VACUUM
To select an appropriate pump for ultra-high vacuum use, it is useful to provide a
few basic rules for the design of an entire system that will achieve the ultimate
pressure within 24 to 48 hours of startup.
1.
As much as possible of the system should be bakeable to at least 200°C
higher than the normal operating temperature, so that materials used for construc-
tion must be stable at the bakeout temperature.
2.
Minimize the surface area of the system, because the outgassing rate is pro-
portional to area. The use of porous materials, such as anodized aluminum,
should be avoided.
3.
Wall materials that are permeable to atmospheric gases should be elimi-
nated, or used very sparingly. This particularly applies to the use of 0-ring seals,
which provide reliable and simple construction for unbaked systems, ^uch seals
not only limit the temperature to which the system can be baked, but they also
permit permeation of atmospheric gases through the elastomer into the vacuum
system, providing a rate of influx that is second only to that from outgassing. Dur-
ing a bakeout, the rate of permeation actually increases, falling to its original
value as the system cools to normal operating temperature. Conversely, the rate of
permeation can be reduced by cooling the seals, although this is generally not a
practical procedure. Demountable 0-ring sealed flanges can be easily replaced by
metal-gasketed flanges such as the Conflat® geometry, eliminating permeation.
The selection of valves is particularly important; permeation from atmosphere
can be avoided by using a metal-gasket bonnet seal and a bellows-sealed shaft
seal. For the most rigorous conditions, the internal seal on the nose of the valve is
a metal seal, such as copper, silver, or gold. Elastomers may be used to provide
somewhat easier sealing (lower force) but at the expense of a limitation in the
bakeout temperature: Viton, Kakez®, and polyimide elastomers have been used,
with usable temperatures of approrfmately 200, 250, and 300°C, respectively,
with the valve baked in the open position.
The efficacy of the procedures just recommended is dramatically illustrated by
the work of Alpert and his colleagues [1] in developing practical techniques for
achieving UHV. Their original glass vacuum systems were outgassed by baking
overnight at ~400°C, while pumping with a liquid-nitrogen-trapped diffusion