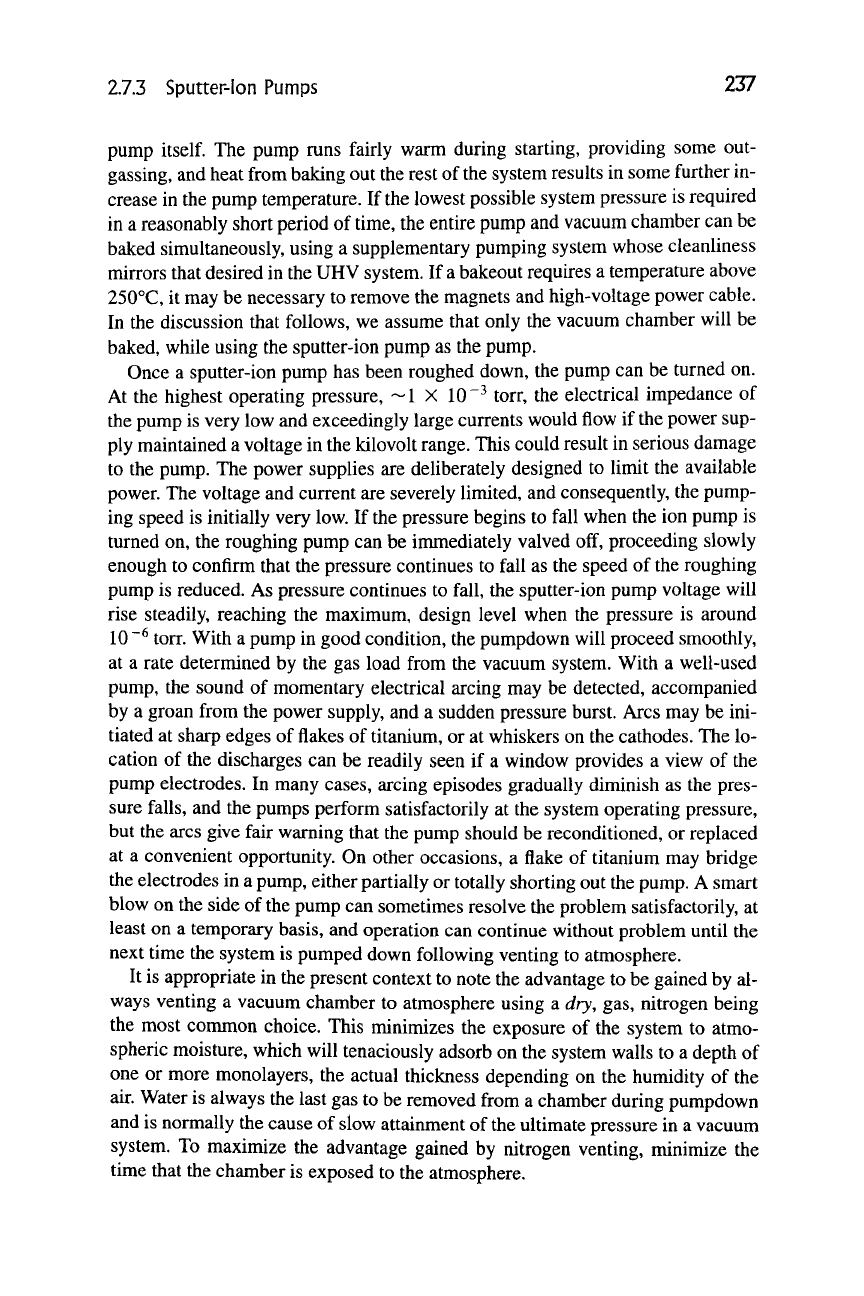
2.7.3 Sputter-Ion Pumps 237
pump
itself.
The pump runs fairly warm during starting, providing some out-
gassing, and heat from baking out the rest of
the
system results in some further in-
crease in the pump temperature. If the lowest possible system pressure is required
in a reasonably short period of
time,
the entire pump and vacuum chamber can be
baked simultaneously, using a supplementary pumping system whose cleanliness
mirrors that desired in the UHV system. If
a
bakeout requires a temperature above
250°C, it may be necessary to remove the magnets and high-voltage power cable.
In the discussion that follows, we assume that only the vacuum chamber will be
baked, while using the sputter-ion pump as the pump.
Once a sputter-ion pump has been roughed down, the pump can be turned on.
At the highest operating pressure, ~1 X 10"^ torr, the electrical impedance of
the pump is very low and exceedingly large currents would flow if the power sup-
ply maintained a voltage in the kilovolt range. This could result in serious damage
to the pump. The power supplies are deliberately designed to limit the available
power. The voltage and current are severely limited, and consequently, the pump-
ing speed is initially very low. If the pressure begins to fall when the ion pump is
turned on, the roughing pump can be immediately valved off, proceeding slowly
enough to confirm that the pressure continues to fall as the speed of the roughing
pump is reduced. As pressure continues to fall, the sputter-ion pump voltage will
rise steadily, reaching the maximum, design level when the pressure is around
10 ~^
torr. With a pump in good condition, the pumpdown will proceed smoothly,
at a rate determined by the gas load from the vacuum system. With a well-used
pump, the sound of momentary electrical arcing may be detected, accompanied
by a groan from the power supply, and a sudden pressure burst. Arcs may be ini-
tiated at sharp edges of flakes of titanium, or at whiskers on the cathodes. The lo-
cation of the discharges can be readily seen if a window provides a view of the
pump electrodes. In many cases, arcing episodes gradually diminish as the pres-
sure falls, and the pumps perform satisfactorily at the system operating pressure,
but the arcs give fair warning that the pump should be reconditioned, or replaced
at a convenient opportunity. On other occasions, a flake of titanium may bridge
the electrodes in a pump, either partially or totally shorting out the pump. A smart
blow on the side of the pump can sometimes resolve the problem satisfactorily, at
least on a temporary basis, and operation can continue without problem until the
next time the system is pumped down following venting to atmosphere.
It is appropriate in the present context to note the advantage to be gained by al-
ways venting a vacuum chamber to atmosphere using a dry, gas, nitrogen being
the most conmion choice. This minimizes the exposure of the system to atmo-
spheric moisture, which will tenaciously adsorb on the system walls to a depth of
one or more monolayers, the actual thickness depending on the humidity of the
air. Water is always the last gas to be removed from a chamber during pumpdown
and is normally the cause of slow attainment of the ultimate pressure in a vacuum
system. To maximize the advantage gained by nitrogen venting, minimize the
time that the chamber is exposed to the atmosphere.