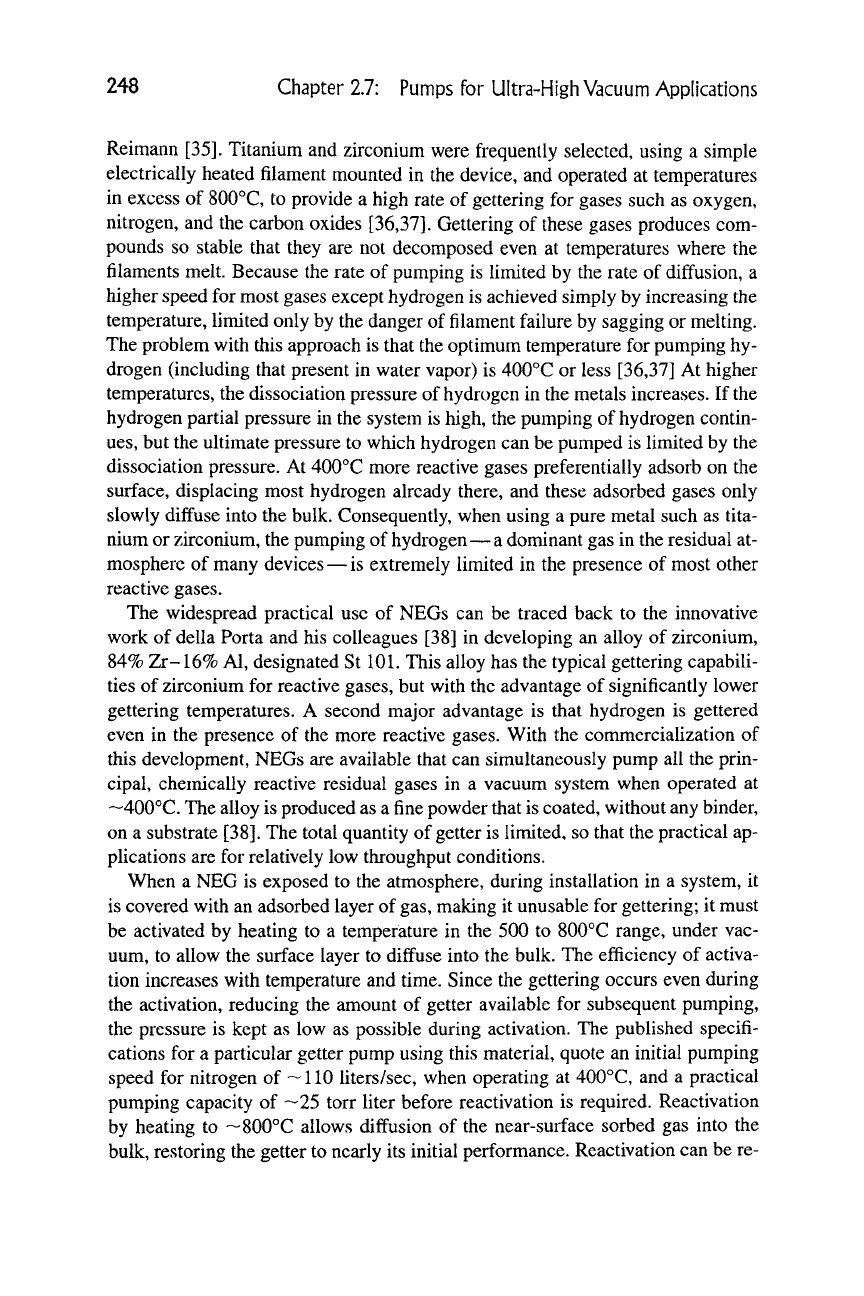
248 Chapter 2.7: Pumps for Ultra-High Vacuum Applications
Reimann [35]. Titanium and zirconium were frequently selected, using a simple
electrically heated filament mounted in the device, and operated at temperatures
in excess of 800°C, to provide a high rate of gettering for gases such as oxygen,
nitrogen, and the carbon oxides [36,37]. Gettering of these gases produces com-
pounds so stable that they are not decomposed even at temperatures where the
filaments melt. Because the rate of pumping is limited by the rate of diffusion, a
higher speed for most gases except hydrogen is achieved simply by increasing the
temperature, limited only by the danger of filament failure by sagging or melting.
The problem with this approach is that the optimum temperature for pumping hy-
drogen (including that present in water vapor) is 400°C or less [36,37] At higher
temperatures, the dissociation pressure of hydrogen in the metals increases. If the
hydrogen partial pressure in the system is high, the pumping of hydrogen contin-
ues,
but the ultimate pressure to which hydrogen can be pumped is limited by the
dissociation pressure. At 400°C more reactive gases preferentially adsorb on the
surface, displacing most hydrogen already there, and these adsorbed gases only
slowly diffuse into the bulk. Consequently, when using a pure metal such as tita-
nium or zirconium, the pumping of hydrogen —
a
dominant gas in the residual at-
mosphere of many devices—is extremely limited in the presence of most other
reactive gases.
The widespread practical use of NEGs can be traced back to the innovative
work of della Porta and his colleagues [38] in developing an alloy of zirconium,
84%
Zr-16% Al, designated St
101.
This alloy has the typical gettering capabili-
ties of zirconium for reactive gases, but with the advantage of significantly lower
gettering temperatures. A second major advantage is that hydrogen is gettered
even in the presence of the more reactive gases. With the commercialization of
this development, NEGs are available that can simultaneously pump all the prin-
cipal, chemically reactive residual gases in a vacuum system when operated at
~400°C. The alloy is produced as a fine powder that is coated, without any binder,
on a substrate [38]. The total quantity of getter is limited, so that the practical ap-
plications are for relatively low throughput conditions.
When a NEG is exposed to the atmosphere, during installation in a system, it
is covered with an adsorbed layer of
gas,
making it unusable for gettering; it must
be activated by heating to a temperature in the 500 to 800°C range, under vac-
uum, to allow the surface layer to diffuse into the bulk. The efficiency of activa-
tion increases with temperature and time. Since the gettering occurs even during
the activation, reducing the amount of getter available for subsequent pumping,
the pressure is kept as low as possible during activation. The published specifi-
cations for a particular getter pump using this material, quote an initial pumping
speed for nitrogen of —110 liters/sec, when operating at 400''C, and a practical
pumping capacity of ~25 torr liter before reactivation is required. Reactivation
by heating to ~800°C allows diffusion of the near-surface sorbed gas into the
bulk, restoring the getter to nearly its initial performance. Reactivation can be re-