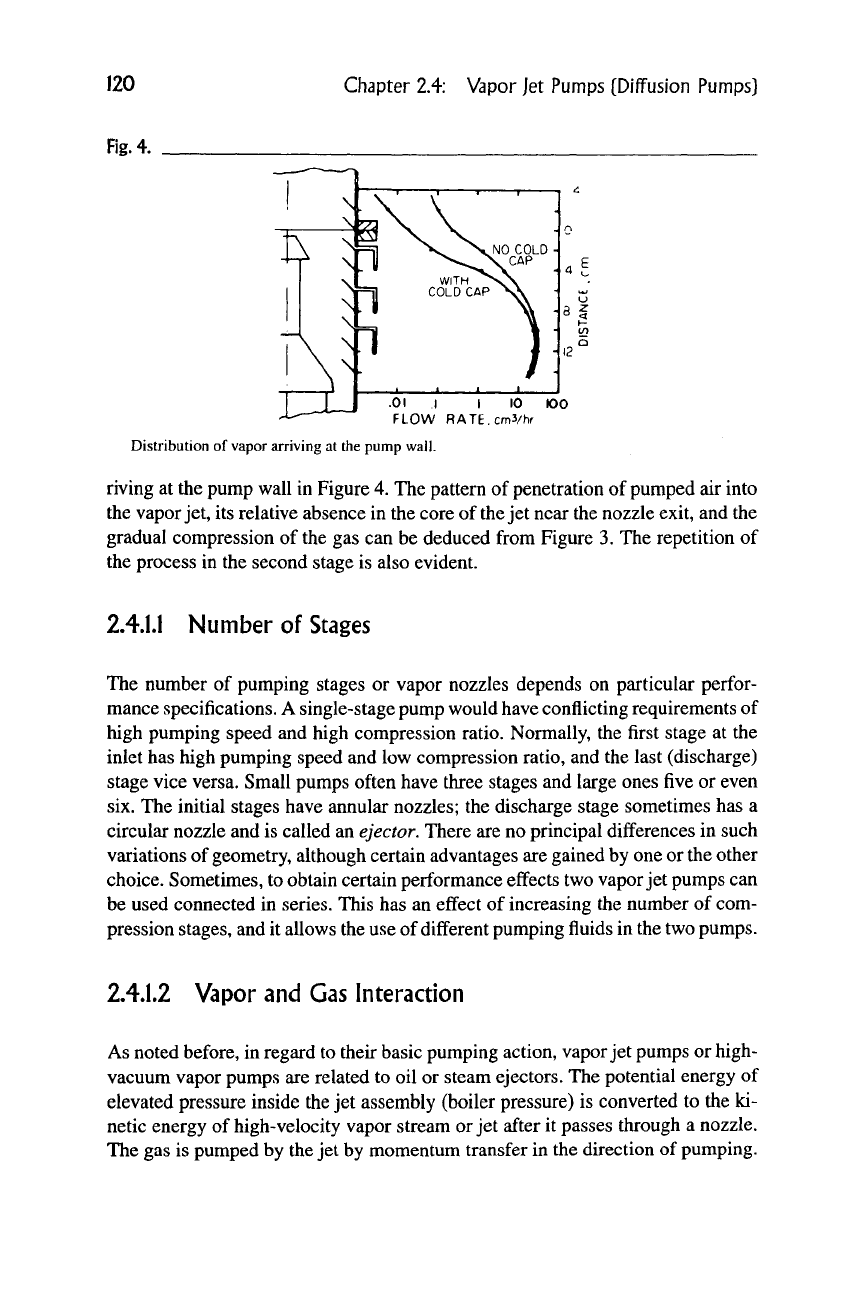
120
Chapter 2.4: Vapor jet Pumps [Diffusion Pumps)
Fig.
4.
8 ^
.01 I I 10 (00
FLOW RATE.cm3/hr
Distribution of vapor arriving at the pump wall.
riving at the pump wall in Figure 4. The pattern of penetration of pumped air into
the vapor jet, its relative absence in the core of
the
jet near the nozzle exit, and the
gradual compression of the gas can be deduced from Figure 3. The repetition of
the process in the second stage is also evident.
2.4.1.1 Number of Stages
The number of pumping stages or vapor nozzles depends on particular perfor-
mance specifications. A single-stage pump would have conflicting requirements of
high pumping speed and high compression ratio. Normally, the first stage at the
inlet has high pumping speed and low compression ratio, and the last (discharge)
stage vice versa. Small pumps often have three stages and large ones five or even
six. The initial stages have annular nozzles; the discharge stage sometimes has a
circular nozzle and is called an ejector. There are no principal differences in such
variations of geometry, although certain advantages are gained by one or the other
choice. Sometimes, to obtain certain performance effects two vapor jet pumps can
be used connected in series. This has an effect of increasing the number of com-
pression stages, and it allows the use of different pumping fluids in the two pumps.
2.4.1.2 Vapor and Gas Interaction
As noted before, in regard to their basic pumping action, vapor jet pumps or high-
vacuum vapor pumps are related to oil or steam ejectors. The potential energy of
elevated pressure inside the jet assembly (boiler pressure) is converted to the ki-
netic energy of high-velocity vapor stream or jet after it passes through a nozzle.
The gas is pumped by the jet by momentum transfer in the direction of pumping.