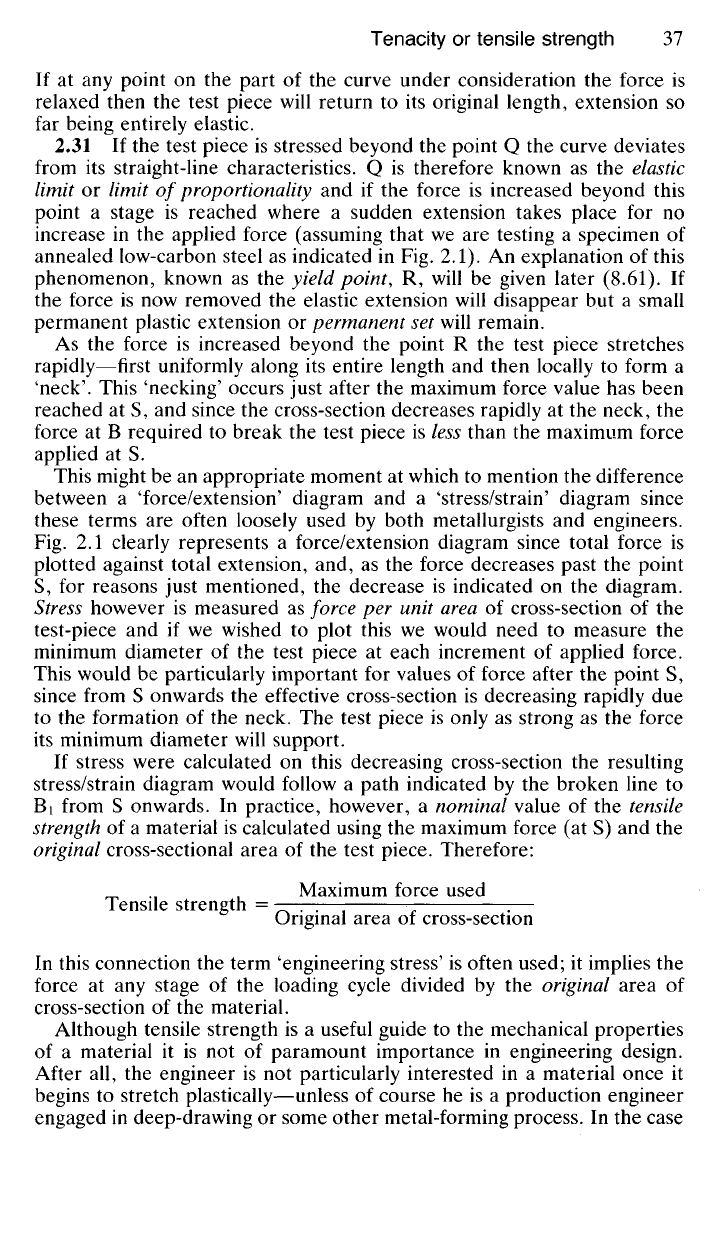
If at any point on the part of the curve under consideration the force is
relaxed then the test piece will return to its original length, extension so
far being entirely elastic.
2.31 If the test piece is stressed beyond the point O the curve deviates
from its straight-line characteristics. Q is therefore known as the elastic
limit or limit of proportionality and if the force is increased beyond this
point a stage is reached where a sudden extension takes place for no
increase in the applied force (assuming that we are testing a specimen of
annealed low-carbon steel as indicated in Fig. 2.1). An explanation of this
phenomenon, known as the yield point, R, will be given later (8.61). If
the force is now removed the elastic extension will disappear but a small
permanent plastic extension or permanent set will remain.
As the force is increased beyond the point R the test piece stretches
rapidly—first uniformly along its entire length and then locally to form a
'neck'. This 'necking' occurs just after the maximum force value has been
reached at S, and since the cross-section decreases rapidly at the neck, the
force at B required to break the test piece is less than the maximum force
applied at S.
This might be an appropriate moment at which to mention the difference
between a 'force/extension' diagram and a 'stress/strain' diagram since
these terms are often loosely used by both metallurgists and engineers.
Fig. 2.1 clearly represents a force/extension diagram since total force is
plotted against total extension, and, as the force decreases past the point
S, for reasons just mentioned, the decrease is indicated on the diagram.
Stress however is measured as force per unit area of cross-section of the
test-piece and if we wished to plot this we would need to measure the
minimum diameter of the test piece at each increment of applied force.
This would be particularly important for values of force after the point S,
since from S onwards the effective cross-section is decreasing rapidly due
to the formation of the neck. The test piece is only as strong as the force
its minimum diameter will support.
If stress were calculated on this decreasing cross-section the resulting
stress/strain diagram would follow a path indicated by the broken line to
Bi from S onwards. In practice, however, a nominal value of the tensile
strength of a material is calculated using the maximum force (at S) and the
original cross-sectional area of the test piece. Therefore:
Maximum force used
Tensile strength = _ . .—
:
—
Original area or cross-section
In this connection the term 'engineering stress' is often used; it implies the
force at any stage of the loading cycle divided by the original area of
cross-section of the material.
Although tensile strength is a useful guide to the mechanical properties
of a material it is not of paramount importance in engineering design.
After all, the engineer is not particularly interested in a material once it
begins to stretch plastically—unless of course he is a production engineer
engaged in deep-drawing or some other metal-forming process. In the case