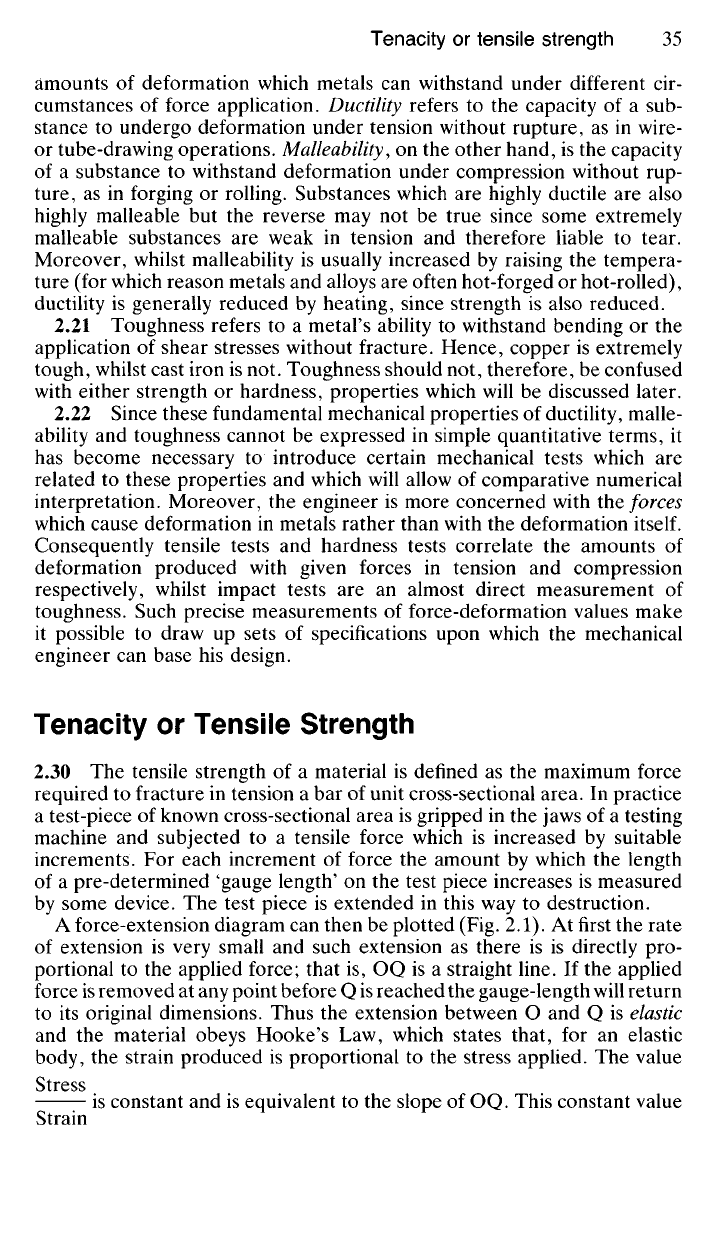
amounts of deformation which metals can withstand under different cir-
cumstances of force application. Ductility refers to the capacity of a sub-
stance to undergo deformation under tension without rupture, as in wire-
or tube-drawing operations. Malleability, on the other hand, is the capacity
of a substance to withstand deformation under compression without rup-
ture,
as in forging or rolling. Substances which are highly ductile are also
highly malleable but the reverse may not be true since some extremely
malleable substances are weak in tension and therefore liable to tear.
Moreover, whilst malleability is usually increased by raising the tempera-
ture (for which reason metals and alloys are often hot-forged or hot-rolled),
ductility is generally reduced by heating, since strength is also reduced.
2.21 Toughness refers to a metal's ability to withstand bending or the
application of shear stresses without fracture. Hence, copper is extremely
tough, whilst cast iron is not. Toughness should not, therefore, be confused
with either strength or hardness, properties which will be discussed later.
2.22 Since these fundamental mechanical properties of ductility, malle-
ability and toughness cannot be expressed in simple quantitative terms, it
has become necessary to introduce certain mechanical tests which are
related to these properties and which will allow of comparative numerical
interpretation. Moreover, the engineer is more concerned with the forces
which cause deformation in metals rather than with the deformation
itself.
Consequently tensile tests and hardness tests correlate the amounts of
deformation produced with given forces in tension and compression
respectively, whilst impact tests are an almost direct measurement of
toughness. Such precise measurements of force-deformation values make
it possible to draw up sets of specifications upon which the mechanical
engineer can base his design.
Tenacity or Tensile Strength
2.30 The tensile strength of a material is defined as the maximum force
required to fracture in tension a bar of unit cross-sectional area. In practice
a test-piece of known cross-sectional area is gripped in the jaws of a testing
machine and subjected to a tensile force which is increased by suitable
increments. For each increment of force the amount by which the length
of a pre-determined 'gauge length' on the test piece increases is measured
by some device. The test piece is extended in this way to destruction.
A force-extension diagram can then be plotted (Fig. 2.1). At first the rate
of extension is very small and such extension as there is is directly pro-
portional to the applied force; that is, OQ is a straight line. If the applied
force is removed at any point before Q is reached the gauge-length will return
to its original dimensions. Thus the extension between O and Q is elastic
and the material obeys Hooke's Law, which states that, for an elastic
body, the strain produced is proportional to the stress applied. The value
Stress
—
is constant and is equivalent to the slope of OQ. This constant value
Strain