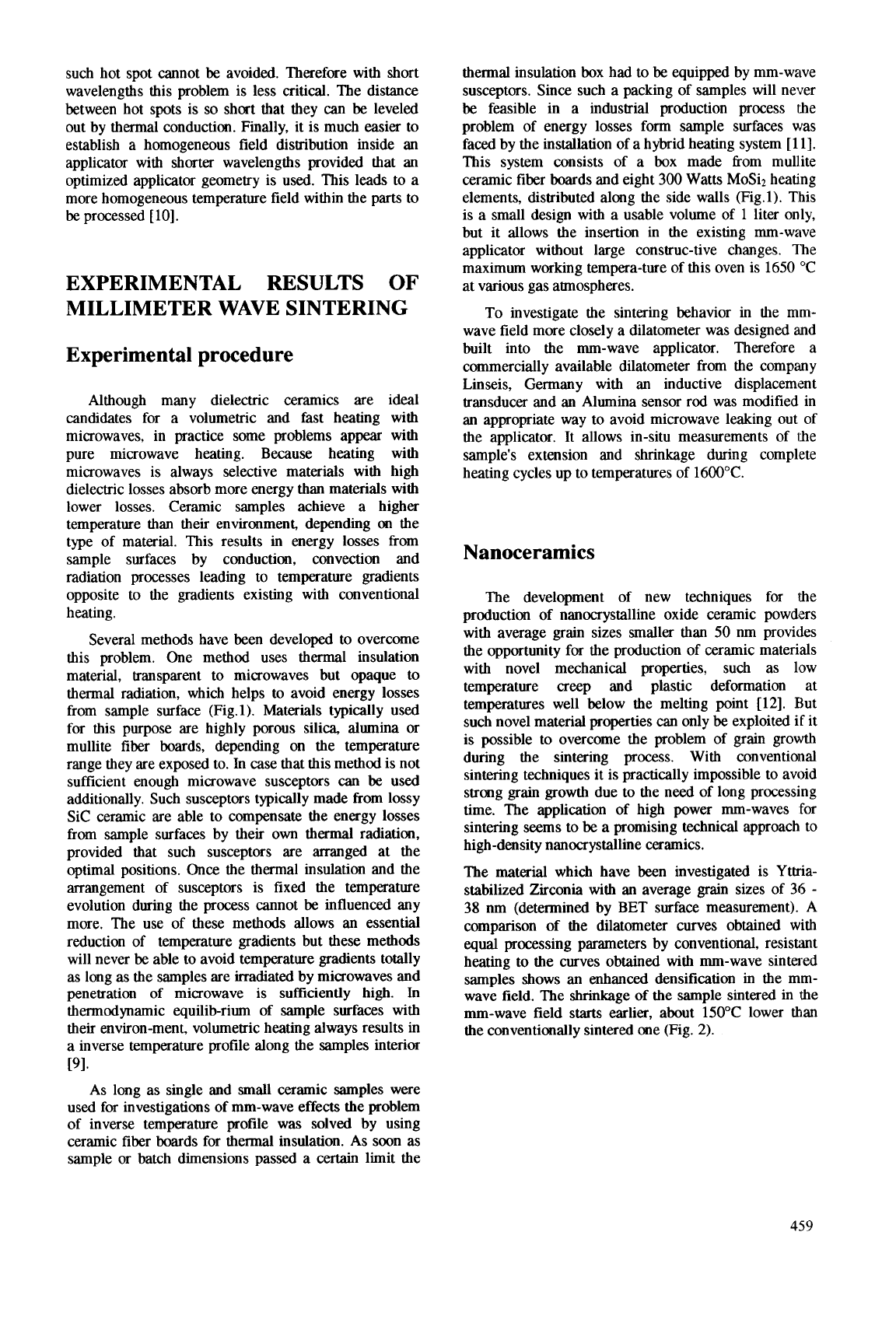
such hot spot cannot be avoided. Therefore with short
wavelengths this problem is less critical. The distance
between hot spots is
so
short that they can be leveled
out by thermal conduction. Finally, it is much easier to
establish a homogeneous field distribution inside an
applicator with shorter wavelengths provided that an
optimized applicator geometry is used. This leads to a
more homogeneous temperature field within the parts to
be processed
[
101.
EXPERIMENTAL RESULTS
OF
MILLIMETER WAVE SINTERING
Experimental procedure
Although many dielectric ceramics are ideal
candidates for a volumetric and fast heating with
microwaves, in practice some problems appear with
pure microwave heating. Because heating with
microwaves is always selective materials with high
dielectric losses absorb more energy than materials with
lower losses. Ceramic samples achieve a higher
temperature than their environment, depending
on
the
type of material. This results in energy losses from
sample surfaces by conduction, convection and
radiation processes leading to temperature gradients
opposite to the gradients existing with conventional
heating.
Several methods have been developed to overcome
this problem. One method uses thermal insulation
material, transparent to microwaves but opaque to
thermal radiation, which helps to avoid energy losses
from sample surface (Fig.1). Materials typically used
for this purpose are highly porous silica, alumina
or
mullite fiber boards, depending on the temperature
range they are exposed to. In case that this method is not
sufficient enough microwave susceptors
can
be used
additionally. Such susceptors typically made from lossy
Sic ceramic are able to compensate the energy losses
from sample surfaces by their
own
thennal radiation,
provided that such susceptors are arranged at the
optimal positions. Once the thermal insulation and the
arrangement of susceptors is fixed the temperature
evolution during the process cannot be influenced any
more. The use of these methods allows an essential
reduction of temperature gradients but these methods
will never be able to avoid temperature gradients totally
as long as the samples are irradiated by microwaves and
penetration
of
microwave
is
sufficiently high. In
thermodynamic equilib-rium of sample surfaces
with
their environ-ment, volumetric heating always results in
a inverse temperature profile along the samples interior
As long as single and small ceramic samples were
used for investigations of mm-wave effects the problem
of inverse temperature profile was solved by using
ceramic fiber boards for thermal insulation.
As
soon as
sample or batch dimensions passed a certain limit the
[91.
thermal insulation box had to be equipped by mm-wave
susceptors. Since such a packing of samples will never
be
feasible in a industrial production process the
problem of energy losses form sample surfaces was
faced by the installation
of
a hybrid heating system
[
111.
This system consists of a box made f?om mullite
ceramic fiber boards and eight 300 Watts MoSiz heating
elements, distributed along the side walls (Fig.1). This
is a small design with a usable volume of 1 liter only,
but it allows the insertion in the existing mm-wave
applicator without large construc-tive changes. The
maximum working tempera-ture of this oven is 1650
"C
at various gas atmospheres.
To investigate the sintering behavior in the mm-
wave field more closely a dilatometer was designed and
built into the mm-wave applicator. Therefore a
commercially available dilatometer from the company
Linseis, Germany with an inductive displacement
transducer and an Alumina sensor rod was modified in
an appropriate way to avoid microwave leaking out of
the applicator. It allows in-situ measurements of Ihe
sample's extension and shrinkage during complete
heating cycles up to temperatures of 1600°C.
Nanoceramics
The development of new techniques for the
production of nanocrystalline oxide ceramic powders
with average grain sizes smaller than
50
nm provides
the opportunity for the production of ceramic materials
with novel mechanical properties, such as low
temperature creep and plastic deformation at
temperatures well below the melting point [12].
But
such novel material properties
can
only
be
exploited if it
is possible to overcome the problem of grain growth
during the sintering process. With conventional
sintering techniques it is practically impossible to avoid
strong
grain
growth due to the need of long processing
time. The application of high power mm-waves for
sintering seems to be a promising technical approach
to
high-density nanocrystalline ceramics.
The material which have been investigated is Yttria-
stabilized Zirconia with
an
average grain sizes of 36
-
38 nm (determined by BET surface measurement).
A
comparison of the dilatometer curves obtained with
equal processing parameters by conventional, resistant
heating to the curves obtained with mm-wave sintered
samples shows an enhanced densification in the mm-
wave field. The shrinkage of the sample sintered in the
mm-wave field
starts
earlier, about 150°C lower than
the conventionally sintered one (Fig. 2).
459