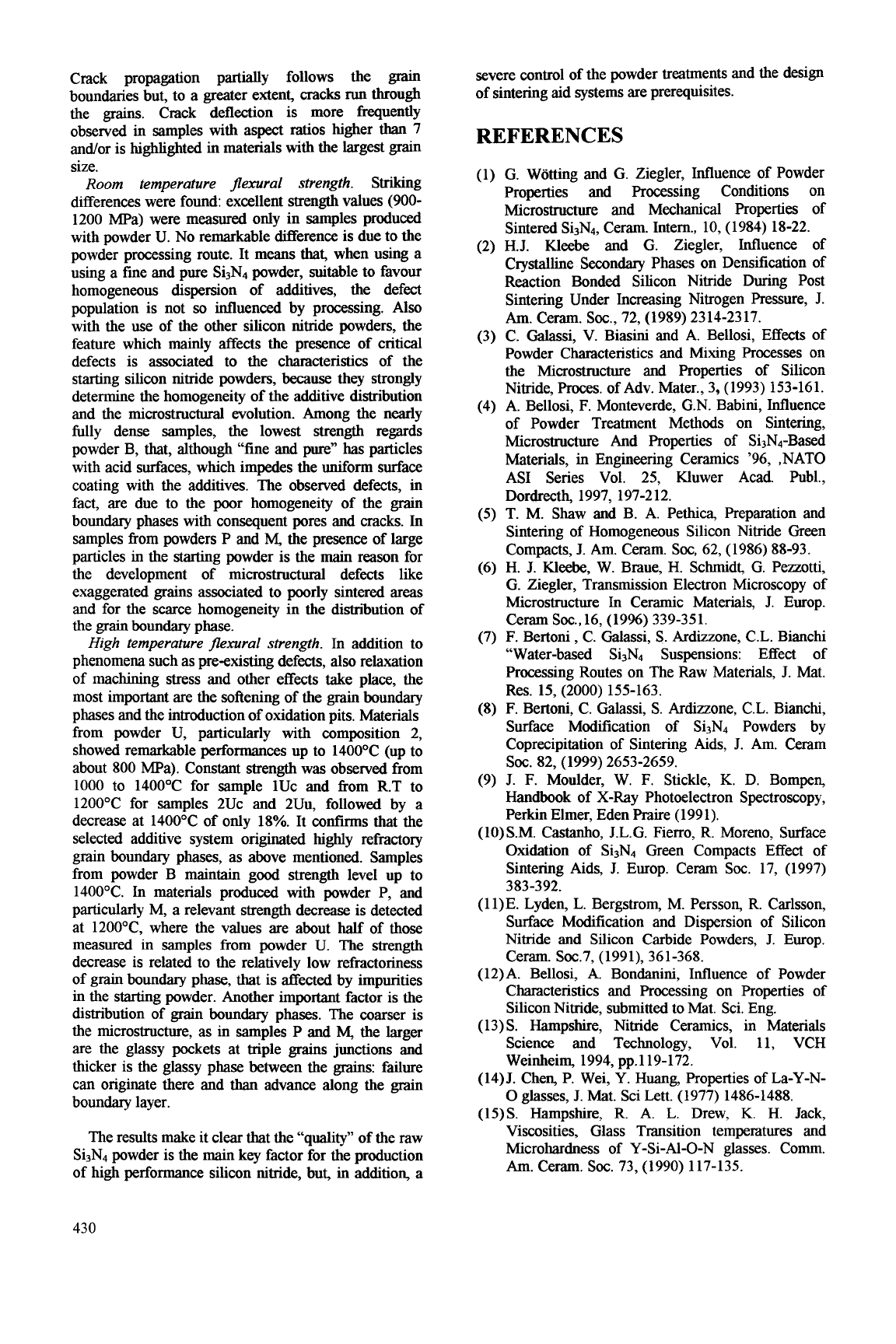
Crack propagation partially follows the
grain
boundaries but, to
a
greater extent, cracks
run
through
the grains. Crack deflection
is
more frequently
observed in samples with aspect
ratios
higher
than
7
andor is highlighted in materials with the largest grain
size.
Room temperature flexural strength.
Striking
differences were found: excellent strength values (900-
1200 MPa) were measured only in samples produced
with powder U. No remarkable difference
is
due to the
powder processing route. It means that, when using
a
using a fine and pure Si3N4 powder, suitable to favour
homogeneous dispersion of additives, the defect
population is not
so
influenced by processing.
Also
with the
use
of the other silicon nitride powders, the
feature which
mainly
affects the presence of critical
defects is associated to the characteristics of the
starting silicon nitride powders,
because.
they
strongly
determine the homogeneity
of
the additive distribution
and the microstructural evolution. Among the nearly
fully dense samples, the lowest strength regards
powder B, that, although “fine
and
pure”
has
particles
with acid surfaces, which impedes the
uniform
surface
coating with the additives. The observed defects, in
fact, are due to the poor homogeneity of the
grain
boundary phases with consequent pores
and
cracks.
In
samples from powders P and
M,
the presence of large
particles in the starting powder
is
the
main
reason for
the development of microstructural defects like
exaggerated grains associated to poorly sintered areas
and for the scarce homogeneity in the distribution of
the grain boundary phase.
High temperature flexural strength.
In
addition to
phenomena such as preexisting defects, also relaxation
of machining stress and other effects take place, the
most important are the softening of the
grain
boundary
phases and the introduction of oxidation pits. Materials
from powder U, particularly with composition 2,
showed remarkable performances up to 140OOC (up to
about 800 MPa). Constant strength was observed from
1000 to 140OOC for sample 1Uc and from R.T to
12OO0C for samples 2Uc and 2Uu, followed by a
decrease at 140OOC of
only
18%. It
confirms
that
the
selected additive system originated highly refractory
grain boundary phases, as above mentioned. Samples
from powder B maintain good strength level up to
1400OC. In materials produced with powder
P,
and
particularly M, a relevant strength decrease
is
detected
at 12OO0C, where the values are about
half
of those
measured in samples from powder U. The strength
decrease is related to the relatively low refractoriness
of grain boundary phase, that
is
affected by impurities
in the
starting
powder. Another important factor is the
distribution of
grain
boundary phases. The coarser is
the microstructure, as in samples
P
and
M,
the larger
are the glassy pockets at triple
grains
junctions and
thicker is the glassy phase between the
grains:
failure
can originate there and
than
advance along the
grain
boundary layer.
The results make it clear that the “quality”
of
the raw
Si3N4 powder
is
the
main
key factor for the production
of high performance silicon nitride, but, in addition,
a
severe control
of
the powder treatments and the design
of sintering aid systems are prerequisites.
REFERENCES
(1)
G. Wotting and G. Ziegler, Influence of Powder
Properties and Processing Conditions on
Microstructure and Mechanical Properties of
Sintered Si3N4, Ceram. Intern., 10, (1984) 18-22.
(2) H.J. Kleebe and G. Ziegler, Influence of
Crystalline Secondary Phases on Densification of
Reaction Bonded Silicon Nitride During Post
Sintering Under Increasing Nitrogen Pressure, J.
(3) C. Galassi,
V.
Biasini and A. Bellosi, Effects of
Powder Characteristics and Mixing Processes on
the Microstructure and Properties of Silicon
Nitride, Proces. of Adv. Mater., 3, (1993) 153-161.
(4) A. Bellosi,
F.
Monteverde, G.N. Babini, Influence
of Powder Treatment Methods on Sintering,
Microshucture And Properties of Si3N4-Based
Materials, in Engineering Ceramics ’96, ,NATO
AS1 Series Vol. 25, Kluwer Acad. Publ.,
Dordrecth, 1997, 197-212.
(5)
T. M. Shaw and B. A. Pethica, Preparation and
Sintering of Homogeneous Silicon Nitride Green
Compacts, J.
Am.
Ceram.
Soc,
62, (1986) 88-93.
(6) H. J. Kleebe, W. Braue,
H.
Schmidt, G. Pezzotti,
G. Ziegler, Transmission Electron Microscopy of
Microstructure In Ceramic Materials,
J. Europ.
Ceram
Soc.,
16, (19%) 339-351.
(7)
F.
Bertoni, C. Galassi,
S.
Ardizzone, C.L. Bianchi
“Water-based Si3N4 Suspensions: Effect of
Processing Routes on
The
Raw Materials, J. Mat.
Res. 15, (2000) 155-163.
(8)
F.
Bertoni, C. Galassi,
S.
Ardizzone,
C.L.
Bianchi,
Surface Modification of Si3N4 Powders by
Coprecipitation of Sintering Aids, J. Am.
Gram
(9) J. F. Moulder, W. F. Stickle,
K.
D. Bompen,
Handbook of X-Ray Photoelectron Spectroscopy,
Perkin Elmer, Eden Praire (1 99 1).
(10) S.M. Castanho, J.L.G. Fierro, R. Moreno, Surface
Oxidation of Si3N4 Green Compacts Effect of
Sintering Aids, J. Europ. Ceram
SOC.
17, (1997)
(1
l)E. Lyden, L. Bergstrom, M. Persson,
R.
Carlsson,
Surface Modification and Dispersion of Silicon
Nitride
and
Silicon Carbide Powders,
J.
Europ.
Ceram. Soc.7, (1991), 361-368.
(12)A. Bellosi, A. Bondanini, Influence of Powder
Characteristics and Processing on Properties of
Silicon Nitride, submitted to Mat. Sci. Eng.
(13)s. Hampshire, Nitride Ceramics, in Materials
Science and Technology, Vol. 11, VCH
Weinheim, 1994, pp.119-172.
(14)J. Chen, P. Wei, Y. Huang, Properties of La-Y-N-
0
glasses,
J. Mat. Sci Lett. (1977) 1486-1488.
(15)s. Hampshire, R. A. L. Drew,
K.
H. Jack,
Viscosities, Glass Transition temperatures and
Microhardness of Y-Si-Al-0-N glasses. Comm.
Am.
Ceram.
Soc.
73, (1990) 117-135.
Am.
C-.
SOC.,
72, (1989) 2314-2317.
SOC.
82, (1999) 2653-2659.
383-392.
430