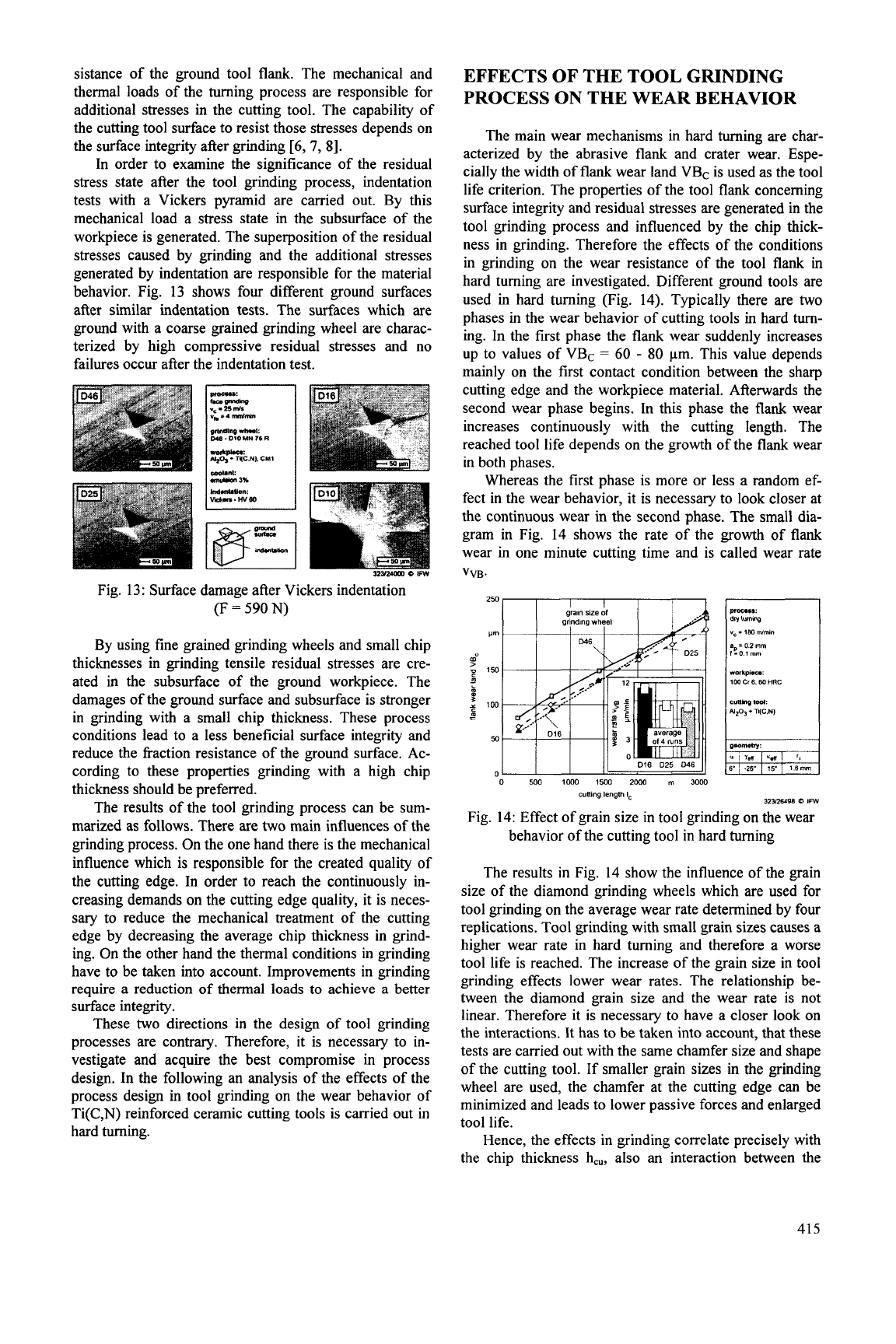
sistance of the ground tool flank. The mechanical and
thermal loads of the turning process are responsible for
additional stresses in the cutting tool. The capability of
the cutting tool surface to resist those stresses depends on
the surface integrity after grinding
[6,
7,
81.
In order to examine the significance of the residual
stress state after the tool grinding process, indentation
tests with a Vickers pyramid are carried out. By this
mechanical load a stress state in the subsurface of the
workpiece is generated. The superposition of the residual
stresses caused by grinding and the additional stresses
generated by indentation are responsible for the material
behavior. Fig. 13 shows four different ground surfaces
after similar indentation tests. The surfaces which are
ground with a coarse grained grinding wheel are charac-
terized by high compressive residual stresses and no
failures occur after the indentation test.
-1
Fig. 13: Surface damage after Vickers indentation
(F
=
590
N)
By using fine grained grinding wheels and small chip
thicknesses in grinding tensile residual stresses are cre-
ated in the subsurface of the ground workpiece. The
damages of the ground surface and subsurface is stronger
in grinding with a small chip thickness. These process
conditions lead to a less beneficial surface integrity and
reduce the fraction resistance of the ground surface. Ac-
cording to these properties grinding with a high chip
thickness should be preferred.
The results of the tool grinding process can be sum-
marized as follows. There are
two
main influences of the
grinding process. On the one hand there is the mechanical
influence which is responsible for the created quality of
the cutting edge. In order to reach the continuously in-
creasing demands on the cutting edge quality, it is neces-
sary
to reduce the mechanical treatment of the cutting
edge by decreasing the average chip thickness in grind-
ing. On the other hand the thermal conditions in grinding
have to be taken into account. Improvements in grinding
require a reduction
of
thermal loads to achieve
a
better
surface integrity.
These two directions in the design of tool grinding
processes are contrary. Therefore, it is necessary to in-
vestigate and acquire the best compromise in process
design. In the following an analysis
of
the effects of the
process design in tool grinding on the wear behavior of
Ti(C,N)
reinforced ceramic cutting tools is carried out in
hard turning.
EFFECTS
OF
THE TOOL
GRINDING
PROCESS
ON THE WEAR BEHAVIOR
The main wear mechanisms in hard turning are char-
acterized by the abrasive flank and crater wear. Espe-
cially the width of flank wear land VBc is used as the tool
life criterion. The properties of the tool flank concerning
surface integrity and residual stresses are generated in the
tool grinding process and influenced by the chip thick-
ness
in
grinding. Therefore the effects of the conditions
in grinding on the wear resistance of the tool flank in
hard turning are investigated. Different ground tools are
used in hard turning (Fig.
14).
Typically there are two
phases in the wear behavior of cutting tools in hard
turn-
ing. In the first phase the flank wear suddenly increases
up to values of VBc
=
60
-
80
pm.
This value depends
mainly on the first contact condition between the sharp
cutting edge and the workpiece material. Afterwards the
second wear phase begins. In this phase the flank wear
increases continuously with the cutting length. The
reached tool life depends on the growth of the flank wear
in both phases.
Whereas the first phase is more or less a random ef-
fect in the wear behavior, it is necessary to look closer at
the continuous wear in the second phase. The small dia-
gram in Fig.
14
shows the rate of the growth of flank
wear in one minute cutting time and is called wear rate
VVB.
250,
I I
I
1
I-
0
500
1WO
15W
2wO
m
3000
culling
length
lc
3ZYXd98
0
IFW
Fig. 14: Effect of grain size in tool grinding on the wear
behavior of the cutting tool in hard turning
The results in Fig. 14 show the influence of the grain
size of the diamond grinding wheels which are used for
tool grinding on the average wear rate determined by four
replications. Tool grinding with small grain sizes causes a
higher wear rate in hard turning and therefore a worse
tool life is reached. The increase of the grain size in tool
grinding effects lower wear rates. The relationship be-
tween the diamond grain size and the wear rate
is
not
linear. Therefore it is necessary to have a closer look on
the interactions. It has to be taken into account, that these
tests are carried out with the same chamfer size and shape
of the cutting tool. If smaller grain sizes
in
the grinding
wheel are used, the chamfer at the cutting edge can be
minimized and leads to lower passive forces and enlarged
tool life.
Hence, the effects in grinding correlate precisely with
the chip thickness h,,, also an interaction between the
415