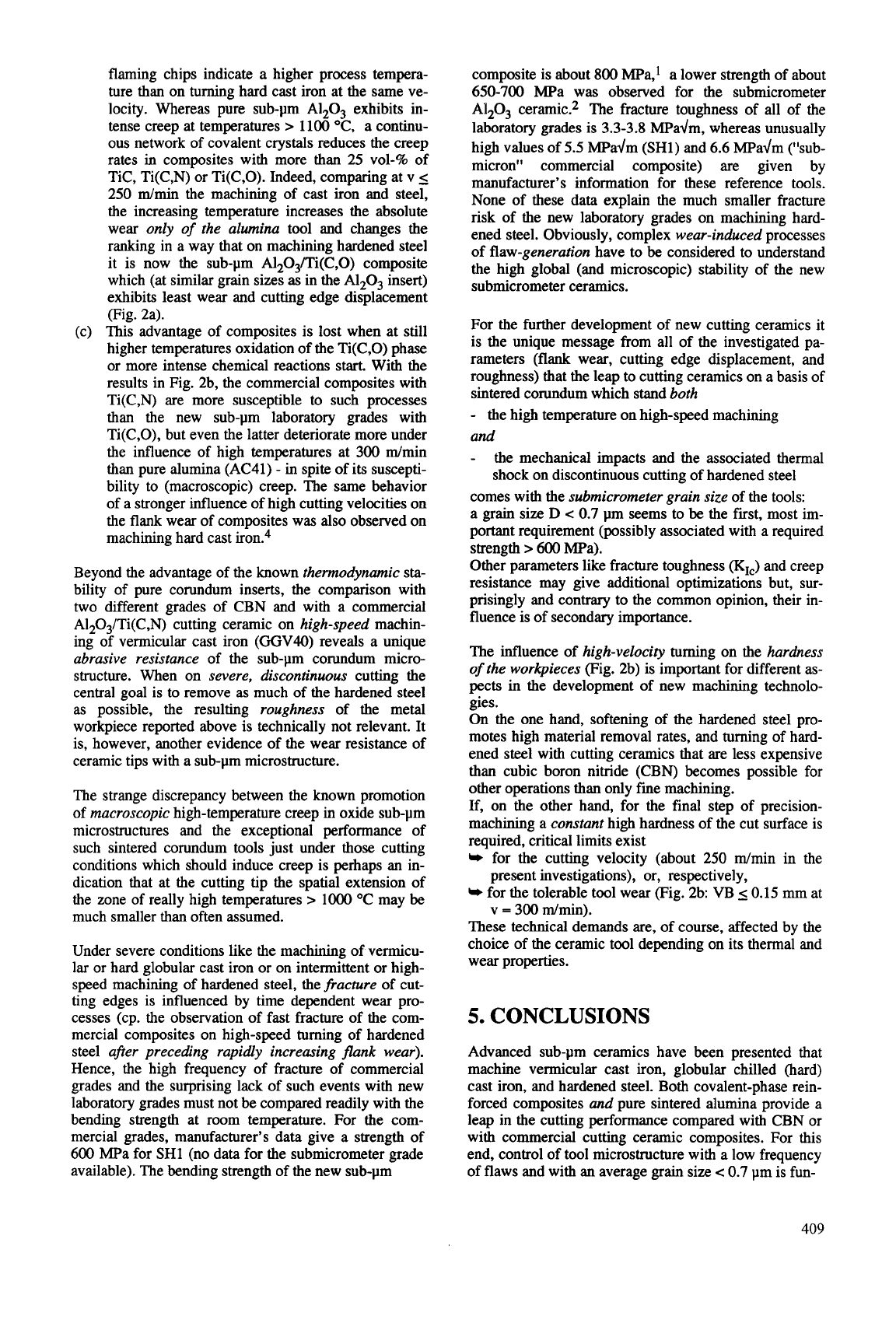
flaming chips indicate a higher process tempera-
ture than on turning hard cast iron at
the
same ve-
locity. Whereas pure sub-pm A1203 exhibits in-
tense creep at temperatures
>
1100
OC, a continu-
ous network of covalent crystals reduces
the
creep
rates in composites with more than 25 vol-% of
Tic, Ti(C,N) or Ti(C,O). Indeed, comparing at v
5
250
dmin
the machining of cast iron and steel,
the increasing temperature increases the absolute
wear
only
of
the alumina
tool and changes the
ranking in a way that on machining hardened steel
it is now the sub-pm A1203/Ti(C,0) composite
which (at similar grain sizes
as
in the A1203 insert)
exhibits least wear and cutting edge displacement
(Fig. 2a).
(c) This advantage of composites is lost when at still
higher temperatures oxidation of the Ti(C,O) phase
or more intense chemical reactions
start.
With the
results in Fig. 2b, the commercial composites with
Ti(C,N) are more susceptible to such processes
than the new sub-pm laboratory grades with
Ti(C,O), but even
the
latter deteriorate more under
the influence of high temperatures at
300
dmin
than pure alumina (AC41)
-
in spite of its suscepti-
bility to (macroscopic) creep. The same behavior
of a stronger influence of high cutting velocities on
the flank wear of composites was also observed on
machining hard cast iron.4
Beyond the advantage of the known
thermodynamic
sta-
bility of pure corundum inserts, the comparison with
two different grades of CBN and with a commercial
Al20,/Ti(C,N) cutting ceramic on
high-speed
machin-
ing of vermicular cast iron (GGV40) reveals a unique
abrasive resistance
of the sub-pm corundum micro-
structure. When on
severe, discontinuous
cutting the
central goal is to remove as much of the hardened steel
as possible, the resulting
roughness
of the metal
workpiece reported above is technically not relevant. It
is, however, another evidence of the wear resistance of
ceramic tips with a sub-pm microstructure.
The strange discrepancy between the known promotion
of
macroscopic
high-temperature creep in oxide sub-pm
microstructures and the exceptional performance of
such sintered corundum tools just under those cutting
conditions which should induce creep is perhaps
an
in-
dication that at the cutting tip
the
spatial extension of
the zone of really high temperatures
>
lo00
OC may
be
much smaller than often assumed.
Under severe conditions like the machining of vermicu-
lar or hard globular cast iron or on intermittent or high-
speed machining of hardened steel, the
fracture
of cut-
ting edges is influenced by time dependent wear pro-
cesses (cp. the observation of fast fracture of the com-
mercial composites on high-speed turning of hardened
steel
afer preceding rapidly increasing
flunk
wear).
Hence, the high frequency of fracture of commercial
grades and the surprising lack of such events with new
laboratory grades must not be compared readily with the
bending strength at room temperature. For
the
com-
mercial grades, manufacturer's data give a strength of
600
MPa for SH1 (no data for the submicrometer grade
available). The bending strength of the new sub-pm
composite is about
800
MPa,' a lower strength of about
650-700
MPa was observed for the submicrometer
A120, ceramic.2 The fracture toughness of all of the
laboratory grades is
3.3-3.8
MPadm, whereas unusually
high values of 5.5 MPadm
(SH1)
and
6.6
MPadm ("sub-
micron" commercial composite) are given by
manufacturer's information for these reference tools.
None of these data explain the much smaller fracture
risk of
the
new laboratory grades on machining hard-
ened steel. Obviously, complex
wear-induced
processes
of
flaw-generation
have to
be
considered to understand
the high global (and microscopic) stability of the new
submicrometer ceramics.
For
the
further development of new cutting ceramics it
is the unique message from all of the investigated pa-
rameters (flank wear, cutting edge displacement, and
roughness) that the leap to cutting ceramics on a basis of
sintered corundum which stand
both
-
the high temperature on high-speed machining
and
-
the mechanical impacts and
the
associated thermal
shock on discontinuous cutting of hardened steel
comes with the
submicrometer grain size
of the tools:
a grain size
D
<
0.7
pm seems to
be
the first, most im-
portant requirement (possibly associated with a required
strength
>
600
MPa).
Other parameters like fracture toughness
(KI,)
and creep
resistance may give additional optimizations but, sur-
prisingly and contrary to the common opinion, their in-
fluence
is
of secondary importance.
The influence of
high-velocity
turning on the
hardness
ofthe workpieces
(Fig. 2b) is important for different as-
pects
in
the
development of new machining technolo-
gies.
On
the one hand, softening of the hardened steel pro-
motes high material removal rates, and turning of hard-
ened steel with cutting ceramics that
are
less expensive
than cubic boron nitride (CBN) becomes possible for
other operations than only
fie
machining.
If, on the other hand, for the final step of precision-
machining a
constant
high hardness of the cut surface is
required, critical limits exist
W
for the cutting velocity (about 250 dmin
in
the
W
for the tolerable tool wear (Fig. 2b: VB
5
0.15
mm
at
These technical demands are, of course, affected by the
choice of the ceramic tool depending on its thermal and
wear properties.
present investigations), or, respectively,
v
=
300
dmin).
5.
CONCLUSIONS
Advanced sub-pm ceramics have been presented that
machine vermicular cast iron, globular chilled (hard)
cast iron, and hardened steel. Both covalent-phase rein-
forced composites
und
pure sintered alumina provide a
leap in the cutting performance compared with CBN or
with commercial cutting ceramic composites. For this
end, control of tool microstructure with a low frequency
of flaws and with an average grain size
<
0.7
pm is fun-
409