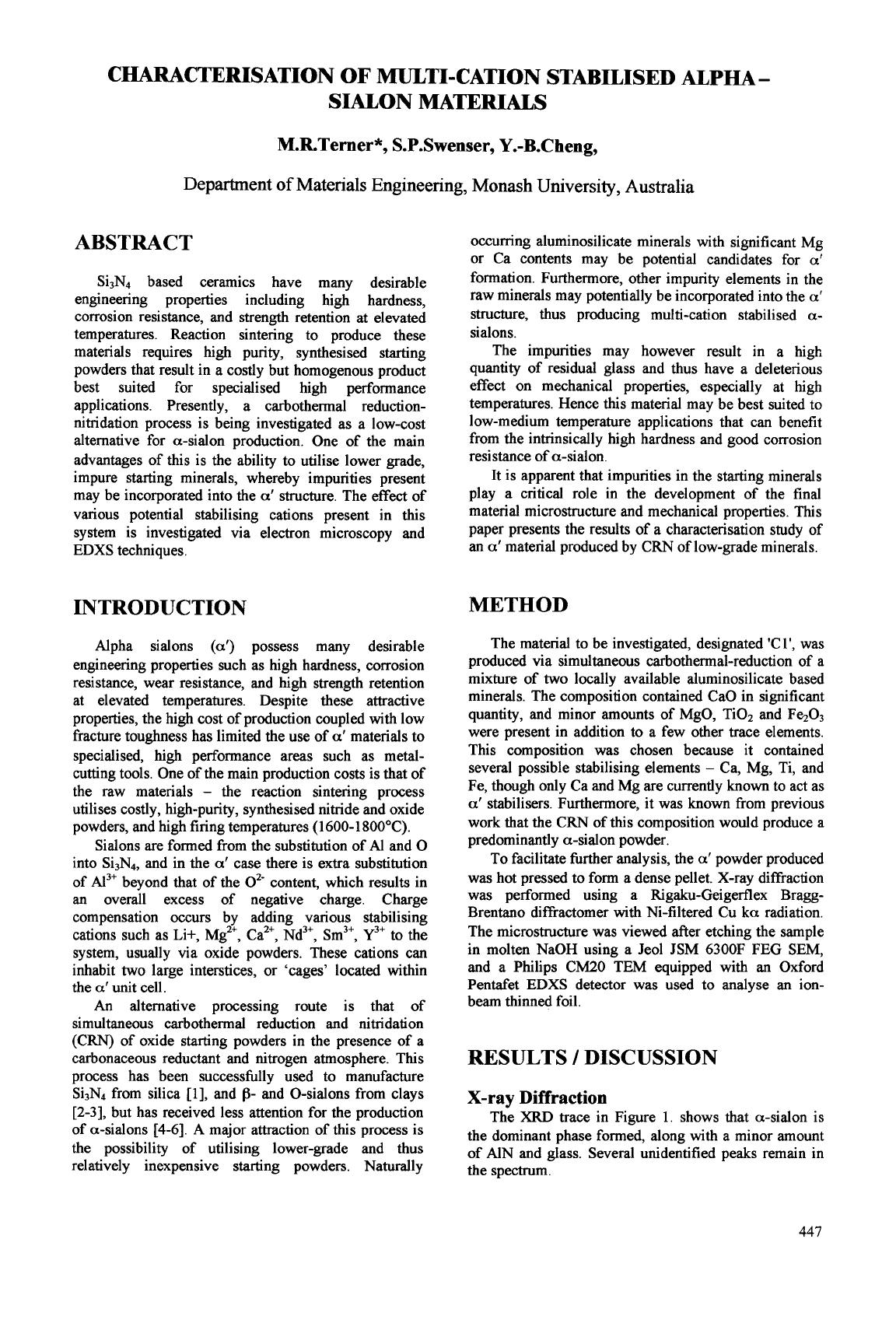
CHARACTERISATION
OF
MULTI-CATION STABILISED ALPHA
-
SIALON
MATERIALS
M.RTerner*, S.P.Swenser, Y.-B.Cheng,
Department
of
Materials Engineering, Monash University, Australia
ABSTRACT
Si3N4 based ceramics have many desirable
engineering properties including high hardness,
corrosion resistance, and strength retention at elevated
temperatures. Reaction sintering to produce these
materials requires high purity, synthesised starting
powders that result in a costly but homogenous product
best suited for specialised high performance
applications. Presently, a carbothermal reduction-
nitridation process is being investigated as a low-cost
alternative for a-sialon production. One of the main
advantages of this is the ability to utilise lower grade,
impure starting minerals, whereby impurities present
may be incorporated into the a’ structure. The effect of
various potential stabilising cations present in this
system is investigated via electron microscopy and
EDXS techniques.
INTRODUCTION
Alpha sialons (a’) possess many desirable
engineering properties such as high hardness, corrosion
resistance, wear resistance, and high strength retention
at elevated temperatures. Despite these attractive
properties, the high cost of production coupled with low
fracture toughness has limited the use of a’ materials to
specialised, high performance areas such as metal-
cutting tools. One of the main production costs is that of
the raw materials
-
the reaction sintering process
utilises costly, high-purity, synthesised nitride and oxide
powders, and high firing temperatures
(1
600-
1
SOOOC).
Sialons are formed from the substitution of
Al
and
0
into Si3N4, and in the a’ case there is extra substitution
of
A13+
beyond that of the
0’-
content, which results in
an overall excess of negative charge. Charge
compensation occurs by adding various stabilising
cations such as Li+, Mg2+, Ca”, Nd3+, Sm3+, Y” to the
system, usually via oxide powders. These cations can
inhabit
two
large interstices, or ‘cages’ located within
the a’ unit cell.
An
alternative processing route is that of
simultaneous carbothermal reduction and nitridation
(CRN) of oxide starting powders in the presence of a
carbonaceous reductant and nitrogen atmosphere. This
process has been successhlly used to manufacture
Si3N4 from silica [l], and
f3-
and 0-sialons from clays
[Z-31,
but has received less attention for the production
of a-sialons
[4-61.
A
major attraction of this process is
the possibility of utilising lower-grade and thus
relatively inexpensive starting powders. Naturally
occumng aluminosilicate minerals with significant Mg
or Ca contents may be potential candidates for
a’
formation. Furthermore, other impurity elements in the
raw minerals may potentially be incorporated into the
a‘
structure, thus producing multi-cation stabilised
a-
sialons.
The impurities may however result in a high
quantity of residual glass and thus have a deleterious
effect on mechanical properties, especially at high
temperatures. Hence
this
material may be best suited to
low-medium temperature applications that can benefit
from the intrinsically high hardness and good corrosion
resistance of a-sialon.
It is apparent that impurities in the starting minerals
play a critical role in the development of the final
material microstructure and mechanical properties. This
paper presents the results of a characterisation study of
an
a’
material produced by CRN of low-grade minerals.
METHOD
The material to be investigated, designated ‘Cl’, was
produced via simultaneous carbothennal-reduction of a
mixture of
two
locally available aluminosilicate based
minerals. The composition contained CaO in significant
quantity, and minor amounts of MgO, Ti02 and F@O3
were present in addition to a few other trace elements.
This composition was chosen because it contained
several possible stabilising elements
-
Ca, Mg, Ti, and
Fe, though only Ca and Mg are currently
known
to act as
a’ stabilisers. Furthermore, it was known from previous
work that the CRN of this composition would produce a
predominantly a-sialon powder.
To facilitate hrther analysis, the
a’
powder produced
was hot pressed to form a dense pellet. X-ray diffraction
was performed using a Rigaku-Geigerflex Bragg-
Brentano difiactomer with Ni-filtered Cu ka radiation.
The microstructure was viewed after etching the sample
in molten NaOH using a Jeol JSM 6300F FEG SEM,
and a Philips CM20 TEM equipped with an Oxford
Pentafet
EDXS
detector was used to analyse an ion-
beam thinned foil.
RESULTS
/
DISCUSSION
X-ray Diffraction
The
XRD
trace in Figure 1. shows that a-sialon is
the dominant phase formed, along with a minor amount
of
AlN
and glass. Several unidentified peaks remain in
the spectrum.
447