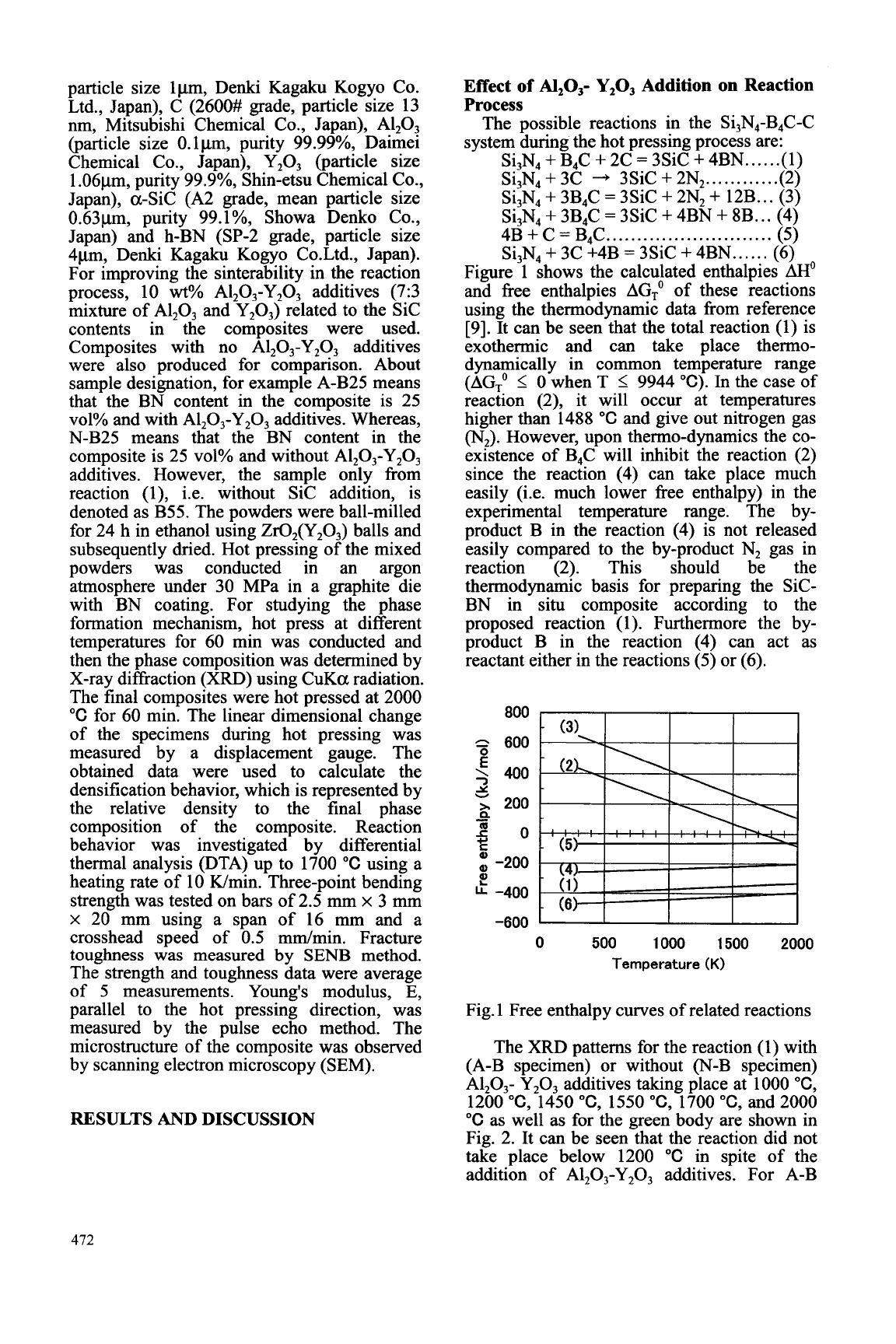
particle size lpm, Denki Kagaku Kogyo Co.
Ltd., Japan), C (2600# grade, particle size 13
nm, Mitsubishi Chemical Co., Japan), A1,0,
(particle size O.lpm, purity 99.99%, Daimei
Chemical Co., Japan), Y203 (particle size
1.06pm, purity 99.9%, Shin-etsu Chemical Co.,
Japan), a-Sic (A2 grade, mean particle size
0.63pm, purity 99.1%, Showa Denko Co.,
Japan) and h-BN (SP-2 grade, particle size
4pm, Denki Kagaku
Kogyo
Co.Ltd., Japan).
For improving the sinterability in the reaction
process, 10
wt%
A1,03-Y203 additives (7:3
mixture of Al,03 and Y203) related to the Sic
contents in the composites were used.
Composites with no A1203-Y203 additives
were also produced for companson. About
sample designation, for example A-B25 means
that the BN content in the composite is 25
vol% and with A1203-Y,03 additives. Whereas,
N-B25 means that the BN content in the
composite is 25 vol% and without Al,03-Y,03
additives. However, the sample only from
reaction (l), i.e. without Sic addition, is
denoted as B55. The powders were ball-milled
for 24
h
in ethanol using Zr02(Y203) balls and
subsequently dried. Hot pressing of the mixed
powders was conducted in an argon
atmosphere under 30 MPa in a graphite die
with BN coating. For studying the phase
formation mechanism, hot press at different
temperatures for 60 min was conducted and
then the phase composition was determined by
X-ray diffraction (XRD) using CuKa radiation.
The final composites were hot pressed at
2000
"C for 60 min. The linear dimensional change
of the specimens during hot pressing was
measured by a displacement gauge. The
obtained data were used to calculate the
densification behavior, which is represented by
the relative density to the final phase
composition of the composite. Reaction
behavior was investigated by differential
thermal analysis (DTA) up to 1700 "C using a
heating rate
of
10 Wmin. Three-point bending
strength was tested on bars of 2.5 mm
x
3 mm
x
20
mm using a span of 16
mm
and a
crosshead speed of 0.5 mdmin. Fracture
toughness was measured
by
SENB method.
The strength and toughness data were average
of 5 measurements. Young's modulus, E,
parallel to the hot pressing direction, was
measured by the pulse echo method. The
microstructure of the composite was observed
by scanning electron microscopy (SEM).
RESULTS AND DISCUSSION
Effect
of
AI2O3-
Y203
Addition on Reaction
Process
The possible reactions in the Si3N4-B4C-C
system during the hot pressing process are:
Si3N4
+
B,C
+
2C
=
3SiC
+
4BN..
. . .
.(
1)
Si3N4
+
3B4C
=
3SiC
+
2N2
+
12B..
.
(3)
Si3N,
+
3B4C
=
3SiC
+
4BN
+
8B..
.
(4)
Si3N4
+
3C +4B
=
3SiC
+
4BN..
. . . .
(6)
Si3N4
+
3C
+
3SiC
+
2N2
............
(2)
4B
+
C
=
B4C
...
.
. .
.
.
.
. . . .
.
. . . .
.
. .
.
. .
.
.
.
(5)
Figure 1 shows the calculated enthalpies
AHo
and free enthalpies
AG:
of these reactions
using the thermodynamic data from reference
[9]. It can be seen that the total reaction (1) is
exothermic and can take place thermo-
dynamically in common temperature range
(AG;
I
0
when T
I
9944 "C). In the case of
reaction (2), it will occur at temperatures
higher than 1488
"C
and give out nitrogen gas
(N,).
However, upon thenno-dynamics the co-
existence of B4C will inhibit the reaction (2)
since the reaction (4) can take place much
easily (i.e. much lower free enthalpy) in the
experimental temperature range. The by-
product B in the reaction (4) is not released
easily compared to the by-product N, gas in
reaction (2). This should be the
thermodynamic basis for preparing the SiC-
BN in situ composite according to the
proposed reaction (1). Furthermore the by-
product B in the reaction (4) can act as
reactant either in the reactions (5) or (6).
800
c
600
\
400
E
2
200
$0
3
v
-
C
Q)
Q)
-200
e!
LL
-400
Fig. 1 Free enthalpy curves of related reactions
The
XRD
patterns for the reaction
(1)
with
(A-B specimen) or without (N-B specimen)
A1203- Y203 additives taking place at 1000 "C,
1200"C, 1450"C, 1550"C, 1700"C, and2000
"C as well as for the green body are shown in
Fig. 2. It can be seen that the reaction did not
take place below 1200 "C in spite of the
addition of A1203-Y@3 additives. For A-B
472