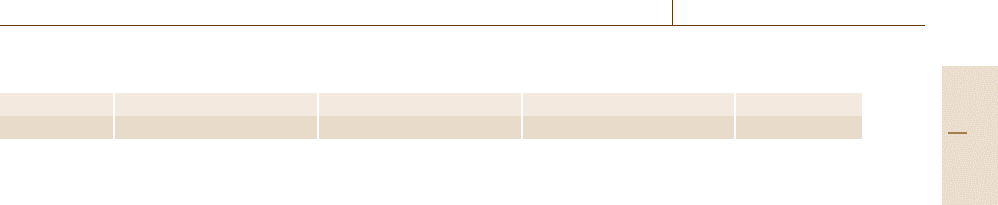
Corrosion 12.8 High-Temperature Corrosion 725
Table 12.5 Permissible tolerance of temperature of test piece [12.97]
T ≤ 573 K 573 K < T ≤873 K 873 K < T ≤1073 K 1073 K < T ≤ 1273 K T > 1273 K
±2K ±3K ±4K ±5K ±7K
02, ASTM E 230-02 and ASTM E 1350-97 [12.104–
106]. If, however, the environment does not allow
the use of such thermocouples in this way the test-
piece temperature has to be deduced from the furnace
calibration using dummy test pieces and appropriate
thermometry in an inert environment. The thermo-
couple should be capable of confirming that the test
temperature is within the range given in Table 12.5.It
should be located at a defined, fixed position as close to
the test pieces as possible.
When a humidifying regulator is used it should be
capable of adjusting to the desired humidity and the
space between the humidifying regulator and the test-
piece chamber should be kept above the dew point to
avoid condensation. The water-vapor content should be
measured, which can be achieved by, e.g., the use of
a hygrometer before the test-piece chamber or mea-
suring the amount of water after condensation of the
exhaust gases. The gas flow has to be high enough to
ensure that no depletion of the reacting species will oc-
cur. At the same time the gas flow must be slow enough
to allow the gas mixture to preheat and in some appli-
cations to reach reaction equilibrium. The TESTCORR
document recommends 1–10 mm/s.
It is recommended that the test pieces have a mini-
mum surface area of 500 mm
2
[12.92]. Their shape can
be a rectangular plate, a disc or a cylinder. Final surface
finishing of the test pieces should be 1200 grit according
to the Federation of European Producers of Abra-
sives (FEPA) standard 43-1984 R 1993 [12.107]and
ISO 6344 [12.108]. Deformation by marking, stamping
or notching of the surface should be avoided. Identifi-
cation of the test pieces should be solely on the basis of
recording their relative position within the test chamber.
In particular for hanging specimens, e.g. for the ther-
mogravimetric test, holes for the test-piece support are
permissible. The test pieces must be dried after degreas-
ing in an ultrasonic bath using isopropanol or ethanol.
Before exposure the mass of the test pieces m
T
(t
0
)has
to be determined by three independent measurements
with the difference between the measurements not ex-
ceeding 0.05 mg.
Several test pieces exposed for different times are
necessary to define the oxidation kinetics of the ma-
terial. Therefore it is recommended that duplicate test
pieces are used with (at least four) exposure times in-
creasing progressively (e.g., 10 h, 30 h, 100 h, 300 h,
...). The material used for the test-piece supports
should not react at the test temperature neither with the
environment nor with the specimen. Examples of rec-
ommended test-piece supports are shown in Fig. 12.52.
Where the possibility of depletion of active species in
the test atmosphere is a concern, the exchange of the
test atmosphere can be improved by the use of holes
or slots in the bottom part of the side walls of the
test-piece support. To remove volatile compounds it is
furthermore recommended that new test-piece supports
should be baked for at least 4 h at 1000
◦
Cinair.In
addition to the mass of the test pieces, that of the test-
piece supports m
s
(t
0
) should be determined prior to
exposure.
Thermal Cycling Oxidation Testing
In the majority of industrial applications temperatures
are never constant. Therefore temperature cycling oxi-
dation/corrosion tests are most often used in industry.
The test equipment is rather similar to that for isother-
mal testing, with the major difference that either the
specimen or the furnace can be moved so that tem-
perature cycles are possible in the test. In Figs. 12.50
and 12.51 the test equipment shown for isothermal test-
ing already allowed for the possibility of moving the
furnace, so that in the same equipment cyclic oxida-
tion testing would also be possible. The advantage of
the equipment shown in Figs. 12.50 and 12.51 is that
these tests can be performed in a defined environment.
In some of the more traditional thermal cycling oxida-
tion test rigs the specimens are moved by some device
out of and into the furnace, which usually requires
that these tests are performed in an open system. As
mentioned above, closed systems with defined environ-
ments are preferred over open systems with laboratory
air.
For completeness it should be mentioned that, as
well as tests with small laboratory specimens, compo-
nent tests, e.g. with complete heat-exchanger tubes, can
even be performed under thermal cycling conditions, as
shown by the schematic in Fig. 12.53. In this case the
furnace consists of two half shells that can be moved
apart on a rail system so that the test-piece chamber is
at ambient temperature when the furnace is open. The
test piece, which in this example is a heat-exchanger
Part D 12.8