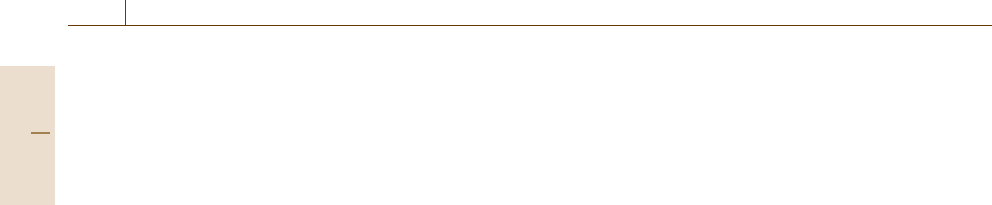
708 Part D Materials Performance Testing
In the case of cracked specimens the limiting condi-
tions are defined by the critical threshold stress intensity
factor K
iscc
.
Tests with Constant Strain
The various types of bending tests that are in use of-
ten belong to this category. These can simulate stresses
from production which are often the cause for failures
in service conditions.
The advantage of bending tests is the use of simple
and hence often cheap specimens and clamping devices.
Problems with this kind of tests usually result from the
low reproducibility of the stress level – if indeed this
can be measured at all. Tests to improve this situation
have led to refined types of bending tests, e.g. four-point
loading instead of three-point loading. But the limita-
tions of the simple bending theory which is usually used
to calculate the stress level can lead to errors, especially
if straining beyond the elastic limit is necessary. The ap-
plication of strain gauges to measure the stresses at the
surface can be useful. The preparation of bend-shaped
parts for U-formed bending specimens introduces sig-
nificant plastic deformation which could affect crack
initiation.
Tensile tests with constant strain are sometimes
preferred to bending tests as the application and calcu-
lation of the stress is simplified. However, more massive
stressing frames are required than for bending speci-
mens of similar cross section.
Apart from affecting the value of the maximum ini-
tial load the stiffness of the frame can also affect the
time to failure of the specimen. In most of the tests with
constant strain, especially when testing ductile mater-
ials, the initial elastic elongation is partly converted into
plastic deformation as the crack formation proceeds.
The magnitude of any loading relaxation can dif-
fer from specimen to specimen and can affect the time
to failure of the specimen depending on the number of
pits or cracks that are present. In the case of specimens
with many cracks or pits considerable relaxation can
be observed while in the presence of only a few cracks
little relaxation can be observed. Thus if only one sin-
gle crack occurs it does not necessarily have to grow
to a considerable size for sudden failure (fracture) of
the specimen to occur as the applied load will remain
high. On the other hand the significant relaxation of the
loading that takes place in the presence of many stress
corrosion cracks means that these cracks have to pro-
ceed further to reach a size that will be sufficient to
generate stress conditions for a sudden fracture to occur
at relatively low loading.
Tests with Constant Load
These tests are more suitable for simulating failures
due to stress corrosion cracking brought about by loads
or stresses occurring in practice. As the effective cross
section of a specimen is reduced by propagating crack
formation tests with constant load include an intensi-
fied stress situation. Hence, it is more probable that such
tests will lead to an earlier failure or fracture compared
to tests with constant total elongation.
Tests with constant load lead to an increasing stress
situation as the initiated cracks continue to grow and
therefore it is more unlikely that cracks, once started,
will be arrested in these tests than those in a constant
strain test below the critical stress threshold. As a conse-
quence, in any particular system the value for the critical
stress threshold is probably lower when determined un-
der constant load than under constant strain.
Tests with Slow Strain Rate
The application of dynamic slow straining, which orig-
inally was only employed as a quick selection test, has
now become more important for simulating conditions
in practice.
This method includes a relatively slow strain or
deformation rate (e.g. 10
−6
s
−1
) of a specimen under
defined environmental conditions, which is continued
until fracture occurs.
For stress corrosion cracking, crack propagation
rates are generally in the range of 10
−3
to 10
−6
mm s
−1
which means that in laboratory tests under constant to-
tal strain or constant loading failure of specimens with
usual dimensions will take place within a few days.
This has also been observed in practice in those systems
where stress corrosion cracking can easily be initiated.
On the other hand it is common experience that speci-
mens do not fail even after very long testing times; for
such situations the test will be stopped after an arbitrary
time period.
The first applications of this test procedure were
aimed at getting data to compare the effects of such vari-
ables as material composition and microstructure or the
addition of inhibitors to stress corrosion cracking initi-
ating environments. It was also used to initiate stress
corrosion cracking for material/environment combi-
nations which did not show crack formation under
constant load or constant total strain in the laboratory.
This means that this test is relatively severe as it often
initiates failure of the specimen due to stress corrosion
cracking where other types of loading of smooth spec-
imens did not lead to crack formation. In view of that
it must be classified in the same category as tests with
Part D 12.6