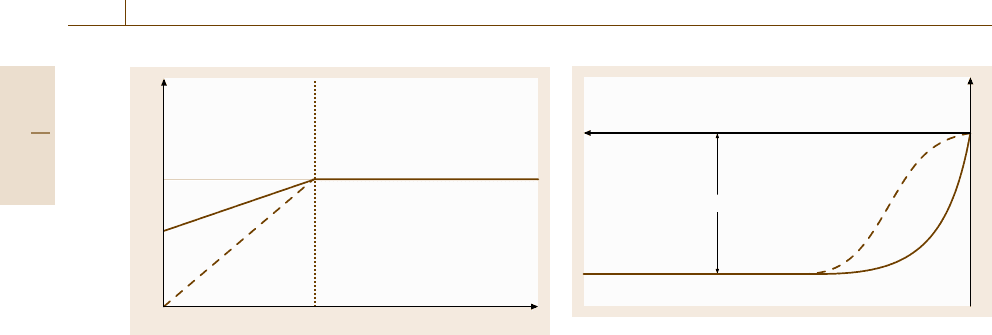
684 Part D Materials Performance Testing
C
δ
C
B
x
Fig. 12.17 Concentration profile in front of an electrode
with Nernst diffusion layer of thickness δ, maximum cur-
rent density i
D
for c =0
much higher rates, thus promoting zinc dissolution. The
common rest potential is positive when compared to that
of pure zinc. These local elements often cause serious
corrosion damage. Another well-known example is the
corrosion of Cu-containing commercial aluminum. Cu
inclusions prevent the total protection of the Al surface
by a passivating Al
2
O
3
film. Cu acts as a local cath-
ode, which compensates the dissolution of Al by local
oxygen reduction. Well-passivated Al does not permit
the reduction of redox systems such as oxygen due
to the isolating electronic properties of the pure pro-
tecting Al
2
O
3
film. For similar reasons one should not
combine reactive metals such as Fe with Cu in water-
containing supplies. The close vicinity of both metals
and some Cu dissolution and its redeposition on a re-
active metal surface will cause local elements. Effective
oxygen reduction at these Cu deposits causes increased
Fe dissolution, as described above.
12.2.10 Diffusion Control
of Electrode Processes
In many cases metal corrosion and the compensating
redox process may be under diffusion control, which
leads to a diffusion overvoltage η
D
. Diffusion of H
+
ions in weakly acidic electrolytes during Fe dissolution
is one example that was discussed in the last section.
Oxygen diffusion within electrolytes is another. Low
oxygen concentration in solution and thick layers of
electrolyte are a frequent situation that causes diffusion
overvoltage. In all these cases the concentration of the
oxidizing species reduces at the metal surface due to
its intense consumption by the reduction process, lead-
ing to a concentration profile. Similarly high dissolution
i
η
i
D
Fig. 12.18 i/η dependence for a cathodic reaction un-
der diffusion control without (solid) and with additional
charge-transfer control (dashed line)
rates of a metal cause the accumulation of its cations at
the metal surface and a related increase of its concentra-
tion. As a consequence a concentration profile builds up
which may cause locally saturated or supersaturated so-
lutions and even the precipitation of corrosion products,
such as the formation of salt films.
Figure 12.17 presents the concentration profile of
the oxidized component Ox in front of an electrode
within the Nernst diffusion layer of thickness δ. The
dashed line refers to the maximal concentration gradient
when the concentration of Ox at the surface approaches
zero. For a diffusion-controlled electrode process the
transfer of Ox equals the current density i accord-
ing to (12.49) which is a combination of Fick’s first
diffusion equation and Faraday’s law with Faraday’s
constant F, the diffusion constant D, the concentra-
tion of Ox at the surface c
S
and within the bulk c
B
,
the thickness of the diffusion layer δ and the number
of electrons for the charge-transfer process n. For van-
ishing concentration c
S
= 0 one obtains the maximum
diffusion current density i
D
according to (12.50). The
combination of (12.49)and(12.50) yields (12.51). If
the charge-transfer reaction is fast with respect to diffu-
sion the electrochemical equilibrium is established with
an electrode potential E = E
0
+η
D
. η
D
is given by the
difference of the electrode potentials for the concen-
trations c
S
and c
B
according to the Nernst equation,
which yields (12.52). Introducing the current densities
i and i
D
with (12.49)and(12.50) one obtains (12.53).
Figure 12.19 depicts the change of the current den-
sity with η for a cathodic process which approaches
i
D
for large overvoltages. For small η the reaction be-
comes charge-transfer controlled, which results in the
dashed curve of Fig. 12.18. Similarly metal dissolution
for large positive polarizations becomes diffusion con-
Part D 12.2