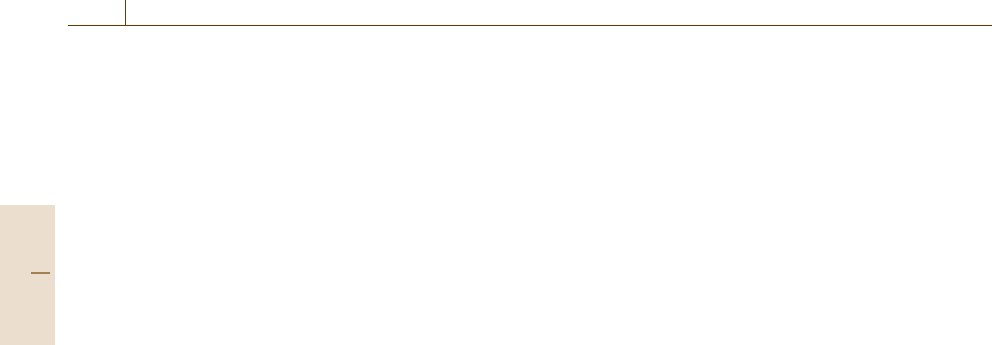
750 Part D Materials Performance Testing
wear mechanism from the initial high-stress regime to
a subsequent low-stress, larger contact area regime. An
approach that reduces this effect is to use one triboele-
ment with a large contact radius so that although the
initial contact geometry is still well defined, the initial
contact pressure is lower, and changes in mechanism are
less likely.
The temperatures of the contacting triboelements
can affect the tribological behavior through changes in
their mechanical and chemical properties. As well as
these bulk effects, the areas of the samples in contact
become hotter through frictional heating; the power dis-
sipated in the contact is given by μNv where μ is the
friction coefficient, N is the normal load, and v is the
relative sliding velocity. The local temperatures at the
contact areas can therefore become much higher than
the bulk temperatures [13.6]. This factor needs to be
taken into account when designing wear tests or inter-
preting test results.
As outlined in Sect. 13.1.3, lubrication of the con-
tacts will also affect the wear, often in terms of
mechanism as well as amount. Under certain condi-
tions of sliding speed, load and lubricant viscosity,
the two surfaces become separated by a continuous,
hydrodynamically-generated lubricant film, and the
wear rate can fall to a very low level, as indicated
in Fig. 13.3. Hydrodynamic lubrication (a thick lubri-
cant film) is favored by low normal pressure, high
lubricant viscosity, and high sliding speed. For con-
ditions where the lubricant film thickness becomes
comparable with the roughness of the triboelements,
elastic deformation of these bodies becomes important
and the pressure in the lubricant is high enough to
cause a significant local increase in viscosity; this is
the regime of elastohydrodynamic lubrication (EHL).
For even thinner films (at low speeds or high contact
pressure), the system enters the regime of boundary lu-
brication, where appreciable interaction occurs between
asperities on the two surfaces. Here the chemical com-
position of the lubricant has a major effect on the nature
and properties of the chemically formed surface films
and on the wear that occurs.
13.2.3 Interaction with Other Degradation
Mechanisms
Other degradation mechanisms such as chemical reac-
tion and fatigue can also make a major contribution to
the overall loss of material from moving contacting sur-
faces. Interactions often occur with the test environment
through chemical reactions of the test materials. In wear
corrosion, the triboelements are exposed to an aqueous
medium, and corrosion of the materials acts in conjunc-
tion with mechanical processes to alter the amount of
material lost. There is positive synergy in most cases,
so that the mass loss is greater than the sum of the con-
tributions expected from pure corrosion or pure wear
alone. Exceptionally, in negative synergy, corrosion can
form a mechanically stronger layer on the surface which
acts to protect the surface and thus reduce the total wear
rate. Tribochemical reactions of materials may also oc-
cur; ceramics, for example, can react with water vapor
to form hydroxides that reduce friction and protect the
wearing surface.
When metals are heated, either through a bulk
increase in temperature or by frictional heating, con-
siderable oxidation can occur. At first this may reduce
wear, as seen in the mild wear of steels, but as the
temperature increases further, the production of weak
oxide may increase to such an extent that the wear rate
increases once more [13.4].
In many tribological systems, the surfaces of
the contacting materials are subjected to alternating
stresses. These stresses may be high enough to initi-
ate and grow fatigue cracks in the material that may
contribute to the material loss caused by other wear
processes. Rolling contact fatigue is an important degra-
dation mechanism in certain applications of materials,
but lies outside the scope of this chapter.
13.2.4 Experimental Planning
and Presentation of Results
When planning a program of tribological tests, the
choice of test conditions must be determined, either
by the relevant engineering application, or in order to
achieve the appropriate mechanism of wear in more
fundamental studies. In the development of materials,
a range of conditions can be chosen to represent those
likely to occur during actual use of the material.
There are many test factors that need to be con-
trolled during a test. These can be grouped into those
concerned with the mechanical test conditions (such
as contact load or pressure, speed, motion type and
test environment), and sample parameters (such as
material composition, microstructure and the initial
surface finish of the samples). A full program of test-
ing under all combinations of these factors would be
time-consuming and costly, and may not be required.
Often a single factor can be identified as key to the
material response, and in this case a good approach
is to set all the other factors at constant values and
Part D 13.2