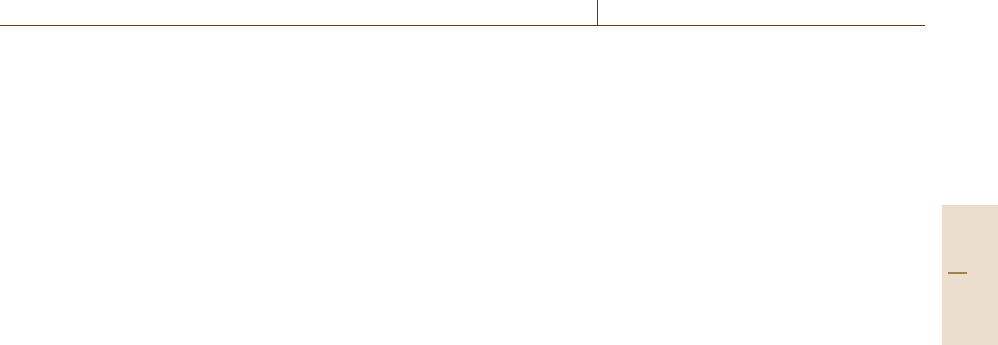
Friction and Wear 13.6 Characterization of Surfaces and Debris 765
stopped, to avoid possible additional corrosion, which
might for example be enhanced by the condensation
of water in a system which cools below the dew point
after running at a higher temperature. Organic lubri-
cants can be removed with organic solvents, and visual
and low-magnification optical inspection should reveal
the presence of any gross solid contaminants. Corro-
sion products may not be readily distinguishable from
wear debris, and indeed in many cases the wear de-
bris will result from chemical reaction of the substrate
material with the environment; but any debris which is
localized in and around the worn region is more likely
to result from the wear process than material which is
more widely distributed on the sample and thus proba-
bly a product of general corrosion. When preparing the
surface, a balance must be struck regarding the amount
of debris to remove to allow the material surface to be
studied. Solvent cleaning in a gentle ultrasonic bath, for
example with ethanol, isopropanol or propanone, fol-
lowed by hot-air drying, should produce a surface which
is clean enough for microscopic examination, but such
a process may remove debris, which can provide valu-
able information about the wear mechanism. It is some-
times possible to retrieve such debris by careful filtra-
tion of the solvent, and to examine the debris on the fil-
ter, or to further classify it, for example by ferrography.
Replication involves the preservation of the sam-
ple’s surface topography by casting or molding a repli-
cating medium against the surface, and then removing
it. Careful experimental technique and the use of an
appropriate replicating medium can lead to excellent
results, and the reproduction of surface features on
a submicrometer scale. Replication allows techniques
such as SEM and profilometry to be applied to regions
of large tribological contacts in the field from which
conventional samples cannot be cut, or to which access
is very difficult. It also allows a sequence of records
to be made from a single specimen at intervals during
a wear test, showing the evolution of surface features,
since it is a nondestructive technique. The ability to
build up a library of replicas of the same region of the
specimen during a test allows the investigator to subse-
quently study in detail the evolution of features which
only become known to be of particular interest at the
end of the test sequence.
Control experiments can be valuable in providing
assurance that the observations on the specimen are not
associated with artefacts introduced by the method of
specimen preparation.
In some cases, examination of the surface of a sam-
ple does not provide sufficient information about the
processes involved in wear, and the subsurface material,
very close to the worn surface, must be studied. It may
also be valuable to measure mechanical properties by
micro- or nanoindentation in this region. Cross-sections
of samples can be prepared for microscopy by conven-
tional metallographic or ceramographic techniques, but
since the regions of interest in the tribological context
will be at or very close to the surface, special attention
must be paid to retaining features in this region, and
to avoiding the introduction of damage during prepara-
tion. The surface can be protected by applying metallic
coatings (such as electroplated nickel) to metal spec-
imens, or by using a hard embedding resin, preferably
containing a hard filler (such as carbon or glass fibers, or
ceramic particles), before the sample is cut perpendicu-
larly to the worn surface and then ground and polished.
Similar grinding and polishing rates should be aimed for
in the protective material and in the worn sample itself,
to achieve a perfectly plane cross-sectional surface for
examination. Ceramics are particularly difficult to pro-
tect in this way, but edge protection may be achieved
by clamping two samples of the same ceramic together,
with the worn surface at the interface, before embedding
and sectioning the composite sample.
Taper sectioning may also be used to study near-
surface microstructure and reduce the effect of pol-
ishing artefacts close to the surface. This technique
involves the examination of a section cut and polished
at a shallow angle to the surface. For example, on a sec-
tion cut at an angle of 5.7
◦
to the surface, a distance
of 10 μm normal to the edge of the sample corresponds
to a depth beneath the surface of only 1 μm (since tan
(5.7
◦
) ≈0.1).
Focused ion beam (FIB) milling provides a powerful
technique to make cuts perpendicular to a worn surface,
either for subsequent examination of the near-surface
regions by SEM, or as a first step in the production of
a sample for TEM. Since it is carried out on a fine scale
and in regions which can be examined in detail by SEM
before the milling takes place, it is possible to study
the subsurface features associated with specific surface
areas of interest.
13.6.2 Microscopy, Profilometry
and Microanalysis
Worn surfaces are often imaged in order to characterize
their surface topography and provide information about
the wear mechanism. In many cases, accurate diagnosis
of wear mechanism may not be possible from imaging
alone, since information on the local chemical composi-
Part D 13.6