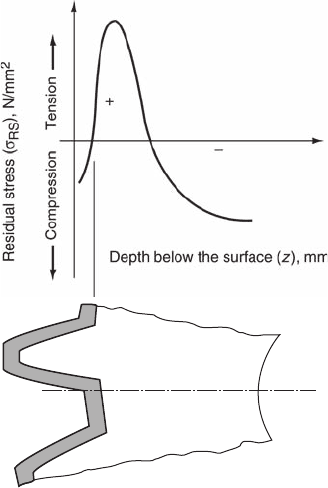
A number of authors have done research into
the effects of power density or energy input used
in heating, with the purpose of determining op-
timal induction-hardening conditions that lead
to good mechanical properties of gears. Lower
power density at the same current frequency
requires longer heating times at the same depth
of the hardened layer and results in higher com-
pressive residual stresses with a moderate tran-
sition of residual stresses from the compressive
into the tensile region.
In induction hardening of gears, it is necessary
to ensure the most uniform depth of the hardened
layer to achieve a symmetric distribution of
residual stresses in the gear tooth cross section.
Workpiece Distortion in Induction
Surface Hardening
Dimensional changes of the workpiece are
closely related to the internal stresses occurring
in heating and cooling. During heat treatment,
when internal stresses in the workpiece are
higher than the yield point, distortion of the
workpiece takes place. When the workpiece has
an axisymmetric shape, it is very important to
place the induction coil so that symmetric
heating and quenching is achieved, resulting in
uniform thickness of the hardened layer with a
martensitic microstructure.
Figure 66 shows induction surface hardening
of a cylindrical rod and tube. When the gap
between the coil and the workpiece varied from
the maximum gap, r
1
, to the minimum gap, r
2
,
that is, r
1
4r
2
, the hardened layer thickness
varied also (Ref 15, 27). This means that the side
of the workpiece with a thicker hardened layer
will suffer greater changes in volume than the
side with the thin layer. A changing thickness of
the hardened layer will result in distortion or
curvature of the cylindrical rod in the direction
of the thinner induction-hardened layer.
Figure 66(a) shows a cylindrical tube with an
induction-hardened inner surface. Asymme-
trical placement of the coil inside the tube (hole,
bore) causes differences in the gap between the
coil and the bore surface inside the workpiece.
The conditions of heating are very similar to
those mentioned earlier, and the cylindrical rod
bends in the direction of the thicker hardened
layer.
Similar distortion happens on prismatic bod-
ies where the specimen dimensions are a · h · l.
Distortion of workpieces subsequent to induc-
tion surface hardening on rectangular cross-
sectional rods, strips, plates, and similar forms is
defined or estimated with respect to the size of
the object and thickness of the hardened surface
layer (Ref 27).
In unilateral surface hardening of prismatic
bodies, the distortion will be greater with a
smaller height (h) and greater length (l). Dis-
tortion also grows with the depth of the hardened
surface layer. Figure 67 shows distortion or,
more precisely, bending of a steel rod with a
rectangular cross section, where the rod has the
same cross section a · h and the same length, l
(Ref 15). Figure 67(a) presents specimens of
equal size and shape that have been induction
hardened to different depths. For an ideal com-
parison, choose heat treatment conditions that
will compare easily, that is, equal power (P) and
frequency (f ), and change the time of heating.
Changing the induction heating time allows the
identification of different depths of the hardened
layer and very similar microhardness or micro-
structure in the transition zone. Figure 67(b)
shows the conditions in induction surface heat-
ing when the temperature transformation is not
exceeded, T
A
1
. This means that on the comple-
tion of quenching, the hardened layer has not
Fig. 65
Residual-stress distribution in the induction surface-
hardened layer of the gear tooth. Source: Ref 15, 20
466 / Failure Analysis of Heat Treated Steel Components
Name ///sr-nova/Dclabs_wip/Failure_Analysis/5113_417-501.pdf/Chap_13/ 18/8/2008 4:02PM Plate # 0 pg 466