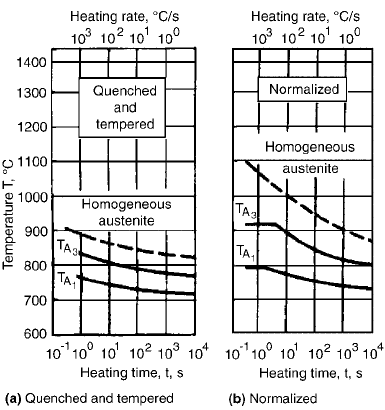
experience and knowledge to achieve the
desirable properties of the gear.
This method is also known as contour hard-
ening. It is an ideal method for heat treatment of
gears, because it increases the hardness on the
tooth surface only slightly while decreasing the
load-bearing capacity in the root of the tooth.
Gears heat treated in this way exhibit very good
behavior in operation, because compressive resi-
dual stresses are present in the root of the tooth.
Gears with induction-hardened flanks, given that
the dimensioning is carefully carried out, can
achieve the highest fatigue strength. To verify
the results of induction surface hardening, it is
necessary to take certain measures for control-
ling the quality of the hardened layer. For this
purpose, hardness and microhardness measure-
ments, supported by microstructural analysis,
are commonly used. A disadvantage of this pro-
cedure is that, due to the method of heating and
quenching (nonuniformly overheated left and
right tooth flank), slightly higher dimensional
deviations may be obtained than in the case of
simultaneous hardening of both flanks of the
same tooth (Fig. 15d) (Ref 27).
Metallurgical Aspect of Induction Surface
Heating. Prior to transformation hardening,
an operator should calculate the processing
parameters for the given power system. The pro-
cedure is as follows. Some of the processing
parameters are chosen, some calculated. The
choice is usually left to the operator and his
experience. Optimization is then based only on
the selection of power density and scan speed.
The correctly set parameters of transformation
hardening ensure the right heating rate, heating
to the right austenitizing temperature, T
A
3
, and a
sufficient austenitizing time, t
A
. Consequently,
with regard to the specified depth of the hard-
ened layer, a temperature a little higher than the
transition temperature, T
A
3
, should be ensured.
Because of a very high heating rate, the equili-
brium diagram of, for example, steel, is not
suitable; therefore, it is necessary to correct the
existing quench temperature with reference to
the heating rate. Thus, with higher heating rates,
a higher austenite transformation temperature
should be ensured in accordance with a time-
temperature-austenitizing (TTA) diagram.
The diagram in Fig. 16(a) is such a TTA
diagram for 1053 steel in the quenched and
tempered state, whereas Fig. 16(b) is for the
same steel in the normalized state (Ref 38).
Because the steel shows a pearlitic-ferritic
microstructure, a sufficiently long time should
be ensured to permit austenitizing. In fast heat-
ing, austenitizing can be accomplished only
by heating the surface and subsurface to an
elevated temperature. For example, with a
heating time, t, of 1 s, for total homogenizing,
a maximum surface temperature, T
s
, of 880
C
should be ensured in the first example and a
much higher surface temperature, 1050
C, in
the second example. This indicates that ap-
proximately 170
C higher surface temperature,
DT
s
, should be ensured in the second example
(normalized state) than in the first example
(quenched and tempered state).
Figure 17 shows a space TTA diagram
including numerous carbon steels with different
carbon contents. The TTA diagram gives par-
ticular emphasis to the characteristic steels, that
is, 1015, 1035, 1045, and 1070 steels, and their
variations of the transition temperature, T
A
3
,
with reference to the given heating rate and the
corresponding heating time (Ref 38). Such a
temperature difference ensures, with regard to
the heating and cooling conditions of the speci-
men, the time required for austenite homo-
genizing, t
A
, in the given depth.
Figure 18 shows a shift of the transformation
temperature, which ensures the formation of
inhomogeneous and homogeneous austenite
within the selected interaction times (Ref 39).
A shorter interaction time will result in a
slightly higher transformation temperature, T
A
1
,
and also a higher transformation temperature,
Fig. 16
Time-temperature-austenitizing diagram for steel
1053 in various states. Source: Ref 38
432 / Failure Analysis of Heat Treated Steel Components
Name ///sr-nova/Dclabs_wip/Failure_Analysis/5113_417-501.pdf/Chap_13/ 18/8/2008 3:59PM Plate # 0 pg 432