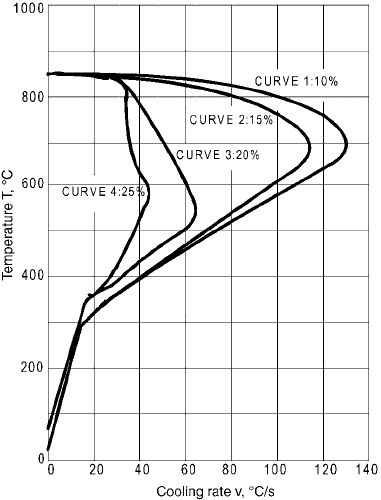
number of outlet nozzle boreholes in one, two, or
more rows at the quenching ring. The fluid flow
rate can also be regulated by pressure. Technical
literature provides data on shaping of quenching
nozzles as well as on the selection of the quen-
chant flow rate required. It is very important that
a sufficient flow rate of the quenchant is chosen
to ensure sufficient heat removal from the work-
piece surface layer during quenching.
The flow rate is also controlled by the number
of boreholes for the flow and spraying of the
quenchant, respectively. An appropriate arrange-
ment of the boreholes in the ring permits a
uniform heat removal after spray and proper
and uniform cooling. The borehole cross sec-
tions should be only 15% of the total available
ring surface and of the inductor in the single-
shot-type application, respectively. Rotation
velocities of the workpieces in surface induction
heating are relatively high and can be selected
between 800 and 1000 rotations per minute,
whereas the rotation velocity of the workpieces
during quenching is considerably lower, that is,
40 to 60 rotations per minute. Very high rotation
velocities of the workpieces are required when a
uniform and reproducible depth of hardened
layer is to be ensured, and particularly with
relatively short heating times.
Figure 44 shows the dependence of cooling
rate changes on the momentary temperature at
the workpiece surface for four different con-
centrations of polymeric water solutions (Ref
24). The selection of an appropriate concentra-
tion of the polymeric water solution for the
selected steel and the required depth of hardened
layer should ensure minimum distortion of the
workpiece, which is the final purpose of any heat
treatment. Thus, the required heat removal from
the heated surface layer of the workpiece, con-
sidering the thickness of the heated layer, should
be ensured by an appropriate quenching system.
Time Variation of Stresses and
Residual Stresses
With a certain heat treatment performed, the
required microstructural changes and an appro-
priate magnitude and variation of hardness are
obtained. It is also required that distortion of a
machine part be as small as possible so that the
final size of a machine part can be obtained with
minimum precision machining. Consequently, it
is very important that distortion be kept under
control. An appropriate machining technology
and appropriate heat treatment processes should
be selected, and internal stresses lower than the
yield stress should be ensured at any moment
and any location of a machine part during heat-
ing and/or cooling. Analytical methods provide
an insight into heat treatment conditions if the
time variation of internal stresses is monitored
and the dependence between the cooling time
and the specimen temperature at each point is
known. With regard to the specimen tempera-
ture determined in this way, the specimen yield
stress at each point can be determined as well.
Consequently, with different heat treatment con-
ditions, different values of physical quantities
can be selected. They are reflected in the chan-
ged conditions in the material, which make it
possible to study distortion of the machine part
during cooling and to determine the magnitude
of the residual stresses.
Figure 45 shows the time variation of axial
stresses at the surface and in individual depths,
that is, from 2.0 to 4.0 mm under the surface
and in the middle of a cylindrical specimen
(Ref 50).
In surface heating, tensile stresses occurred
at the surface due to thermal extension of the
Fig. 44
Polymer additive ratio effects on the cooling rate.
Source: Ref 24
452 / Failure Analysis of Heat Treated Steel Components
Name ///sr-nova/Dclabs_wip/Failure_Analysis/5113_417-501.pdf/Chap_13/ 18/8/2008 4:01PM Plate # 0 pg 452