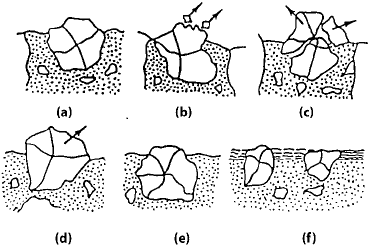
very complex physical and chemical processes
take place on the microlevel. For an accurate
description of the conditions in the contact zone
for machining a given material, it is necessary to
consider the grinding method as well as the kind
of material from which the grinding wheel is
made, its structure, and the grinding conditions.
The heat conditions in grinding are a result of the
contact conditions between the individual grind-
ing grains and the workpiece material as well as
deformation work in chip formation in the shear
zone. The amount of generated heat is strongly
dependent on the chosen machining conditions
and is abducted mainly through the chip, while a
smaller part of the generated heat is transferred
through heat transfer into the thin surface layer
of the workpiece. Heating of the chip does not
cause any particular difficulties, but heating of
the thin surface layer of the workpiece creates
the conditions for different mechanical and
thermokinetic processes, which cause micro-
chemical changes. Heating up the thin surface
layer of the workpiece can leave certain unde-
sirable effects that change the properties of the
part surface layer and thus harm its operational
abilities. The generated friction heat is trans-
ferred through the heat-transfer phenomenon
from the contact between the grinding grain and
the workpiece into the grinding grain.
The increased amount of heat on the grinding
grain or grinding wheel intensifies the wear
processes and damage of particular grinding
grains, which follow very different and complex
mechanisms and, in the final phase, affect the
serviceability and operational life of the tool.
The grinding tool consists of grinding grains,
each representing a process. Grinding grains are
interconnected with an appropriate binder,
which is defined by different degrees of porosity
of the grinding wheel structure. Therefore, it is
necessary to also know the force needed to break
the grinding grain from a given structure, ex-
pressed by the grinding wheel hardness. Simul-
taneous changes in volume proportions of the
grinding grains and binder can create different
structures on the grinding wheel that do not be-
have in the same way. This means that by
changing the kind of material for the grinding
wheel and the binder, it is possible to achieve
equal effects by changing the structure of the
grinding wheel. It follows that by a suitable
combination of influential parameters, it is pos-
sible to achieve a longer life and wear resistance
of the wheel in equal kinematic conditions of the
wheel and the workpiece. The wear of the
grinding grains is a result of mechanical and
thermal effects, which are reflected in reduced
cuttability. Figure 75 shows the basic forms of
wear and damage on the grinding wheel grains,
expressed by characteristic changes on the
grinding grains (Ref 15, 64). Due to mechanical
loads on particular grinding grains, short-lived
but intensive heat effects are created in the con-
tact or on the friction surfaces with the work-
piece. In these cases, blunting of the grinding
grains (Fig. 75a), breaking off of the grind-
ing grains (Fig. 75b), or splitting of the grinding
grains (Fig. 75c) may happen. Requirements are
often set that a worn-out grain should fall from
the grinding wheel at a certain moment. A worn-
out grain typically has an increased contact
surface, which causes the forces on the grinding
grain during the cutting process to be higher than
the binding forces between the grains, and there-
fore, the grain falls out (Fig. 75d). It is expected
that the manufacturing engineer will carefully
choose all the parameters of the process so that
the worn-down grains fall out. This ensures
more efficient machining and reduced thermo-
mechanical effects in the thin surface layer of the
workpiece material. To create a suitable quality
of the workpiece surface and surface layer, it
is necessary to ensure that grinding grains will
fall out, and that the activation of new, sharp
grinding grains is made possible.
It is very important to choose a cutting con-
dition that would make the grains fall out only
when their cuttability is reduced. Figure 75(e)
illustrates characteristic blunting of the grinding
grain due to chemical reactions at high tem-
peratures. Chemical reactions at high tempera-
tures are frequently followed by filling the pores
with overheated, highly plastic chips of the
workpiece material (Fig. 75f). When the pores
Fig. 75
Basic forms of wear and damage on the grinding
wheel grain. Source: Ref 15, 64
Induction Hardening / 473
Name ///sr-nova/Dclabs_wip/Failure_Analysis/5113_417-501.pdf/Chap_13/ 18/8/2008 4:03PM Plate # 0 pg 473