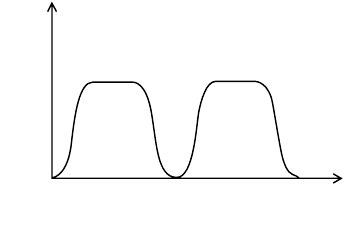
21-34 Mechatronic Systems, Sensors, and Actuators
coil is constrained to rotate, these forces will generate a torque, which will tend to make the coil turn in
the anti-clockwise direction. The function of the commutator is to ensure that the flow of electrons is
always in the correct direction as each side of the coil passes the respective poles of the magnet. The
commutator incorporates brass segments, separated by insulating mica strips. The carbon brushes make
sliding contact with the commutator.
When the coil lies in the horizontal direction, there is maximum magnetic flux linking the coil but a
minimum rate of change of flux linkages. On the other hand, when the coil is in the vertical plane, there
is zero flux linking the coil but the rate of change of flux linkages is a maximum. The resultant change
in torque acting on the coil through one revolution is as shown in Figure 21.57.
If two coils physically displaced by 90° are used in conjunction with two separate magnets, also
displaced by 90°, then the output torque is virtually constant. With the introduction of a second coil,
the commutator needs to have four separate segments. In a typical DC machine there may be as many
as 36 coils, which would require a 72-segment commutator.
The simple DC motor of Figure 21.56 can be improved in perhaps three obvious ways. Firstly, the
number of coils can be increased, the number of turns in each coil can be increased, and finally the
number of magnetic poles can be increased. A typical DC machine would therefore normally incorporate
four poles, wired in such a way that each consecutive pole has the opposite magnetic polarity to each of
its immediate neighboring poles. If the torque generated in the armature coils are to assist one another
then while one side of the coil is passing under a north pole, the other side must be passing under a
south pole. With a two-pole machine the armature coils are wound with one side of the coil diametrically
opposite the other. In a four-pole machine the coils are wound such that one side of the coil is displaced
90° from the other. The size of the machine will generally determine how many coils and the number
of turns on each coil which can be accommodated.
21.2.2 Armature Electromotive Force (emf)
If a conductor cuts a magnetic flux, a voltage of 1 V will be induced in the conductor if the flux is cut
at the rate of 1 Wb/s. Denoting the flux per pole as Φ and the speed (in rev/s), as N, for a single turn
coil and two-pole machine, the emf induced in the coil is given as
(21.15)
For a machine having Z
s
armature conductors connected in series, i.e., Z
s
/2 turns, and 2p magnetic
poles, the total induced emf is
(21.16)
FIGURE 21.57 Torque variation through one revolution.
orque
0 180 360
An
le of rotation [de
rees]
E
coil
flux per pole
time for half rev
--------------------------------------
Φ
1/2N
------------
2NΦ===
E
2NΦZ
s
2p
2
------------------------ 2NΦZ
s
p==
9258_C021_Sect002-005.fm Page 34 Wednesday, October 10, 2007 7:10 PM