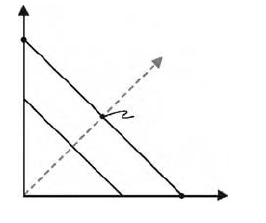
Actuators 21-13
application if it delivers the required force at one half its free deflection. High operating voltage, hysteresis,
creep, and fatigue are the main mechanical design considerations.
21.1.2.4 Efficiency
Efficiency is one of the major considerations for any energy conversion process. In most cases, the wasted
energy is converted to heat and increases the device temperature. For electromechanical actuators, heat
(temperature) is one of the most prominent performance-limiting factor as well as failure mode. As
device temperature increases, the underlying conversion efficiency will suffer and dump more energy
into heat, which further increases the device temperature. This is often referred to as thermal runaway.
Therefore, it is very important when designing electromechanical actuators to prevent thermal runaway
and guarantee that under normal operating condition the actuator system achieves thermal equilibrium.
The equilibrium temperature should be maintained below the lowest rated temperature of the compo-
nents, such as the electrical insulation for the windings. The temperature rating for electrical insulations
are listed in Table 21.1.
21.1.3 Power Amplification and Modulation—Switching Power Electronics
As described in the previous section and depicted in Figure 21.2, there are two main functions in an
extended definition of an actuator for mechatronics systems. We have introduced a few energy conversion
mechanisms and the associated actuators. In the second part of this chapter, we will focus on the power
amplification and modulation portion of the actuator. This part of the actuator is traditionally called
the power amplifier or the driver for the corresponding actuator. However, as miniaturization and system
integration become more pervasive, power electrics are being embedded into either the controller (infor-
mation processing unit) or the actuator. It is also the portion where intelligence and additional func-
tionality/feature can be incorporated. For electromechanical actuators, the unmodulated energy source
is electricity. The power amplifier acts as a buffer between the low energy part of the system, where
actuation command is given in low energy electrical signals, and the high energy density electrical signal
that will be converted.
Power amplification can roughly be categorized into two methods, linear and switching. The main
advantage of linear power amplification is the “cleanness” of the signal as compared to the switching
amplifiers. The main drawback is in efficiency, where linear amplifiers tend to run hotter than similar
sized switching amplifiers. However, as with any engineering design, this is only a rule-of-thumb; the
designer needs to analyze the application and select or design the appropriate driver.
Switching amplifiers are made of semiconductor components such as diodes and transistors. These
semiconductor devices either function as a switching element that controls the current flow to the energy
conversion element such as a winding coil, or as an amplification element that modulates the amount of
current flowing into the winding coil. Another advantage of using switching type power amplifiers is that,
with switching, the amplifier stage can be directly controlled by a digital signal from an information
processing device (see Figure 21.1) such as a microcontroller or a microprocessor. This eliminates the need
FIGURE 21.18 Static performance curve of a typical
piezoelectric actuator. (Courtesy of Piezo Systems, Inc.)
Direction of
increasing
voltage
Force
V
max
Deflection
F
b
X
f
V
V
1
V
1
Operating point
optimized produce
maximum work
9258_C021_Sect001.fm Page 13 Wednesday, October 10, 2007 7:09 PM