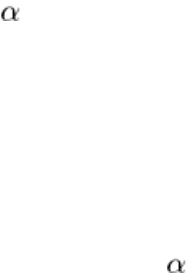
The required metal removal and the pickling times achieved in acid pickling are dictated by several factors, including
depth of α case to be removed, pickle tank operating conditions, process specification requirements, and potential for
hydrogen pickup by the workpiece. Acid pickling presents the potential for excessive hydrogen pickup in titanium alloys;
therefore, this process must be carefully controlled. Metal removal rates in acid pickling are usually 0.03 mm/min (0.001
in./min) or more, although the metal removal rate is heavily influenced by such factors as the alloy, acid concentrations,
bath temperature, and contained titanium. Metal removal levels of 0.25 to 0.38 mm (0.010 to 0.015 in.) per surface are
usually sufficient to remove the αcase; however, greater or lesser amounts of metal removal may be necessary, depending
on the alloy and the specific conditions present for the forging in question.
Metal removal is monitored by witness pads on the forging (using an appropriate maskant), by test panels processed with
the forgings, by actual forging measurement, or by other process control techniques. In addition, some process and/or
materials specifications for titanium alloy forgings require verification of α case removal on the final forgings. The
techniques used on representative samples of the lot of forgings include metallographic examination and/or
microhardness measurements.
As a guide only, hydrogen pickup in acid pickling may be up to 10 ppm of hydrogen for each 0.03 mm (0.001 in.) of
surface metal removal, depending upon specific pickling solution and concentration and temperature conditions. In acid
pickling, alloys tend to absorb less hydrogen than α-β alloys, which in turn tend to pick up less hydrogen than β alloys.
Current process and/or material specifications for titanium alloy forgings always require measurement of final hydrogen
content on each lot of forgings using either vacuum fusion or vacuum extraction techniques (typical specifications require
maximum hydrogen contents in forgings of 125 to 150 ppm). Therefore, acid pickling parameters must be controlled--
often to individual forging shapes and/or specific alloys--to avoid final hydrogen contents in excess of specification
requirements, which can be corrected only by vacuum annealing. The potential for hydrogen pickup in acid pickling is
significantly increased by decreased rates of metal removal (due to increased titanium content of the solution), higher bath
temperatures (for example, bath temperatures higher than 60 °C, or 140 °F), and higher surface-area-to-volume
relationships in the workpieces. Generally, the speed of metal removal through solution concentration and temperature
must exceed the rate of hydrogen diffusion. With appropriate controls, acid pickling is used to remove precise amounts of
material in order to remove case and/or to assist in obtaining the required forging dimensions (for example, in titanium
precision forgings) without an undue increase in hydrogen content. Additional information on the cleaning of titanium
alloys is available in the article "Surface Engineering of Titanium and Titanium Alloys" in Surface Engineering, Volume
5 of the ASM Handbook.
Heat Treatment. Most titanium alloy forgings are thermally treated after forging, with heat treatment processes
ranging from simple stress-relief annealing to multiple-step processes of solution treating, quenching, aging, and/or
annealing designed to modify the microstructure of the alloy to meet specific mechanical property criteria. Selection of
the heat treatment for titanium alloy forgings is based on the alloy, forging configuration, and mechanical property
objectives. The furnaces used to thermally treat titanium alloy forgings are either continuous or batch gas-fired, electric,
fluidized-bed, vacuum, or other specially designed equipment. Titanium alloy forgings that are heat treated in other than
vacuum furnaces can be processed with or without ceramic precoats for protection from reaction during the thermal
processes, depending on such factors as the alloy, the specific heat-treating equipment, the forging type (that is,
conventional versus precision), and process/material specification requirements. The thermal treatments used for titanium
alloys in forgings and other product forms are also discussed in Ref 4 and in the article "Heat Treating of Titanium and
Titanium Alloys" in Heat Treating, Volume 4 of the ASM Handbook.
Annealing is used on forgings of most types of titanium alloys in order to remove the deformation and/or thermal
stresses imparted as a result of forging hot-working processes and/or postforging cooling rates. Annealing is generally
done in the temperature range of 595 to 925 °C (1100 to 1700 °F), depending on the specific alloy. It does not cause
significant microstructural modification and is applied to conventional titanium alloy forgings primarily to facilitate the
subsequent fabrication of the forgings, including machining.
Multiple-Step Heat Treatments. To modify the microstructure and resultant mechanical properties (such as strength,
ductility, fatigue, creep, and fracture toughness) of many forged titanium alloys, multiple-step heat treatments (such as
solution treatment plus aging/annealing, recrystallization annealing, duplex annealing, and so on) are often used. The
terminology for these treatments is frequently borrowed from aluminum alloys; however, the metallurgical effects
obtained are actually changes in allotropic phase relationships or phase morphology. As with the solution treatment of
aluminum alloy forgings, if such multiple-step thermal treatment processes are applied to titanium alloy forgings, then
racking procedures, quench rates, quench media, and so on, are the subject of forged titanium alloy heat treatment process
specification and process control. Furthermore, as previously discussed, when preheating for forging, precoats, furnace