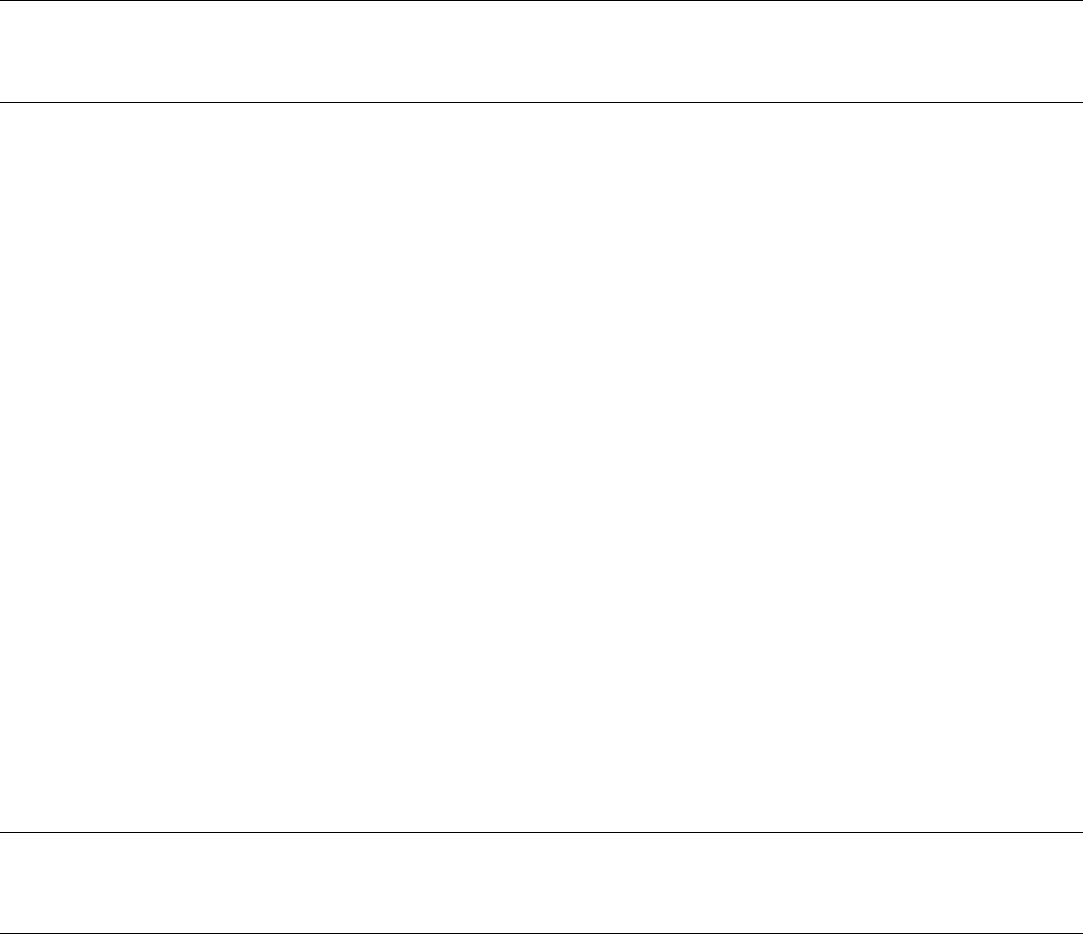
1.
A.J. DeRidder and R. Koch, in
MiCon 78: Optimization of Processing, Properties, and Service Performance
Through Microstructural Control, H. Abram et al.,
Ed., American Society for Testing and Materials, 1979, p
547
2.
T. Altan, F.W. Boulger, J.R. Becker, N. Akgerman, and H.J. Henning,
Forging Equipment, Materials, and
Practices, MCIC-HB-03, Metals and Ceramics Information Center, 1973
3.
T.G. Byrer, Ed., Forging Handbook, Forging Industry Association and American Society for Metals, 1985
4.
D.R. Muzyka, in
MiCon 78: Optimization of Processing, Properties, and Service Performance Through
Microstructural Control, H. Abrams et al., Ed., American Society for Testing and Materials, 1979, p 526
5.
L.A. Jackman, in Proceedings of the Symposium on Properties of High Temperature Alloys,
Electrochemical Society, 1976, p 42
Forging of Titanium Alloys
G.W. Kuhlman, Aluminum Company of America
Introduction
TITANIUM ALLOYS are forged into a variety of shapes and types of forgings, with a broad range of final part forging
design criteria based on the intended application. As a class of materials, titanium alloys are among the most difficult
metal alloys to forge, ranking behind only refractory metals and nickel/cobalt-base superalloys. Therefore, titanium alloy
forgings, particularly closed-die forgings, are typically produced to less highly refined final forging configurations than
are typical of aluminum alloys (although precision forgings in titanium alloys are produced to the same design and
tolerance criteria as aluminum alloys; see the section "Titanium Alloy Precision Forgings" in this article) and to
equivalent or more refined forging design sophistication than carbon or low-alloy steel forgings, because of reduced
oxidation or scaling tendencies in heating. Because of the high cost of titanium alloys in comparison to other commonly
forged materials, such as aluminum and alloy steels, final forging design criteria in titanium closed-die forgings are
typically balanced between producibility demands and cost considerations (particularly machining costs and overall metal
recovery).
In addition, the working history and forging parameters used in titanium alloy forging have a significant impact on the
final microstructure (and therefore the resultant mechanical properties) of the forged alloy--perhaps to a greater extent
than in any other commonly forged material. Therefore, the forging process in titanium alloys is used not only to create
cost-effective forging shapes but also, in combination with thermal treatments, to create unique and/or tailored
microstructures to achieve the desired final mechanical properties through thermomechanical processing (TMP)
techniques. For a given titanium alloy forging shape, the pressure requirements in forging vary over a large range,
depending primarily on the chemical composition of the alloy, the forging process being used, the forging strain rate, the
type of forging being manufactured, lubrication conditions, and die temperature. The chemical compositions,
characteristics, and typical mechanical properties of all wrought titanium alloys referred to in this article are reviewed in
the article "Wrought Titanium and Titanium Alloys" in Properties and Selection: Nonferrous Alloys and Special-Purpose
Materials, Volume 2 of the ASM Handbook.
Forging of Titanium Alloys
G.W. Kuhlman, Aluminum Company of America
Titanium Alloy Classes
Because of the strong relationship among the required forging process parameters, deformation behavior, and mechanical
properties of the various titanium alloys, it is necessary to review the classes of titanium alloys that are forged and their
typical thermomechanical processing requirements, which exert a strong influence on forging part design and forging
process selection. Titanium and its alloys exist in two allotropic forms: