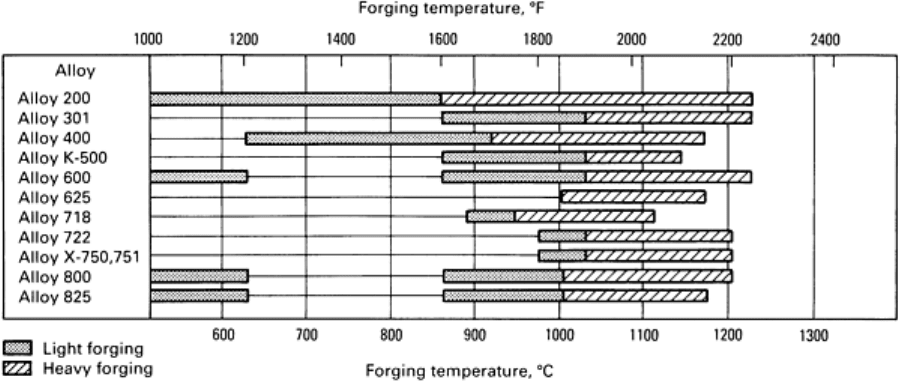
Gaseous fuels such as natural gas, manufactured gas, butane, and propane are the best fuels and should always be used if
available. They must not contain more than 2 g (30 grains) of total sulfur per 2.8 m
3
(100 ft
3
) of gas and preferably not
more than 1 g (15 grains) of total sulfur per 2.8 m
3
(100 ft
3
) of gas.
Oil is a satisfactory fuel provided it has a low sulfur content. Oil containing more than 0.5% sulfur should not be used.
Coal and coke are generally unsatisfactory, because of the difficulty in providing for proper heating conditions,
inflexibility in heat control, and excessive sulfur content.
The furnace atmosphere should be sulfur free and should be continuously maintained in a slightly reducing
condition, with 2% or more carbon monoxide. The atmosphere should not be permitted to alternate from reducing to
oxidizing. The slightly reducing condition is obtained by reducing the air supply until there is a tendency to smoke, which
indicates an excess of fuel and a reducing atmosphere. The air supply should then be increased slightly to produce a hazy
atmosphere or a soft flame. Excessive amounts of carbon monoxide or free carbon are not harmful; nickel-base alloys,
unlike steels, will not carburize under these conditions. However, a slight excess of fuel over air is all that is required, and
the closer the atmosphere is to the neutral condition, the easier it is to maintain the required temperature. The true
condition of the atmosphere is determined by analyzing gas samples taken at various points near the metal surface.
It is important that combustion take place before the mixture of fuel and air contacts the work, or the metal may be
embrittled. Proper combustion is ensured by providing ample space to burn the fuel completely before the hot gases enter
the furnace chamber.
General Guidelines for the Breakdown of Nickel-Base Alloys (Ref 1). Because of their high alloy content and
generally narrow working temperature range, nickel-base alloys must be converted from cast ingots with care. Initial
breakdown operations are generally conducted well above the γ' solvus temperature, with subsequent deformation
completed below it but still high enough to avoid excessive warm working and an unrecrystallized microstructure. The
original cast structure must be completely refined during breakdown, that is, before final forging, particularly when
substantial levels of reduction are not imposed during closed-die forging.
Good heat retention practice during ingot breakdown is an important factor in obtaining a desirable billet microstructure.
Rapid transfer of the ingot from the furnace to the forging press, as well as the use of such techniques as reheating during
breakdown, is necessary to promote sufficient recrystallization during each forging pass. In addition, it has been found
that diffusion of precipitation-hardening elements is associated with recrystallization during ingot conversion. Mechanical
factors such as cycling speed (which affects heat losses), reduction, length of pass, die design, and press capacity all
influence the degree of work penetration through the billet cross section and therefore the rate of ingot conversion.
General Guidelines for the Finish Forging of Nickel-Base Alloys. Figure 1 shows the temperature ranges for
the safe forging of 12 nickel-base alloys. Use of the lower part of the temperature range may be required for the
development of specific mechanical properties.