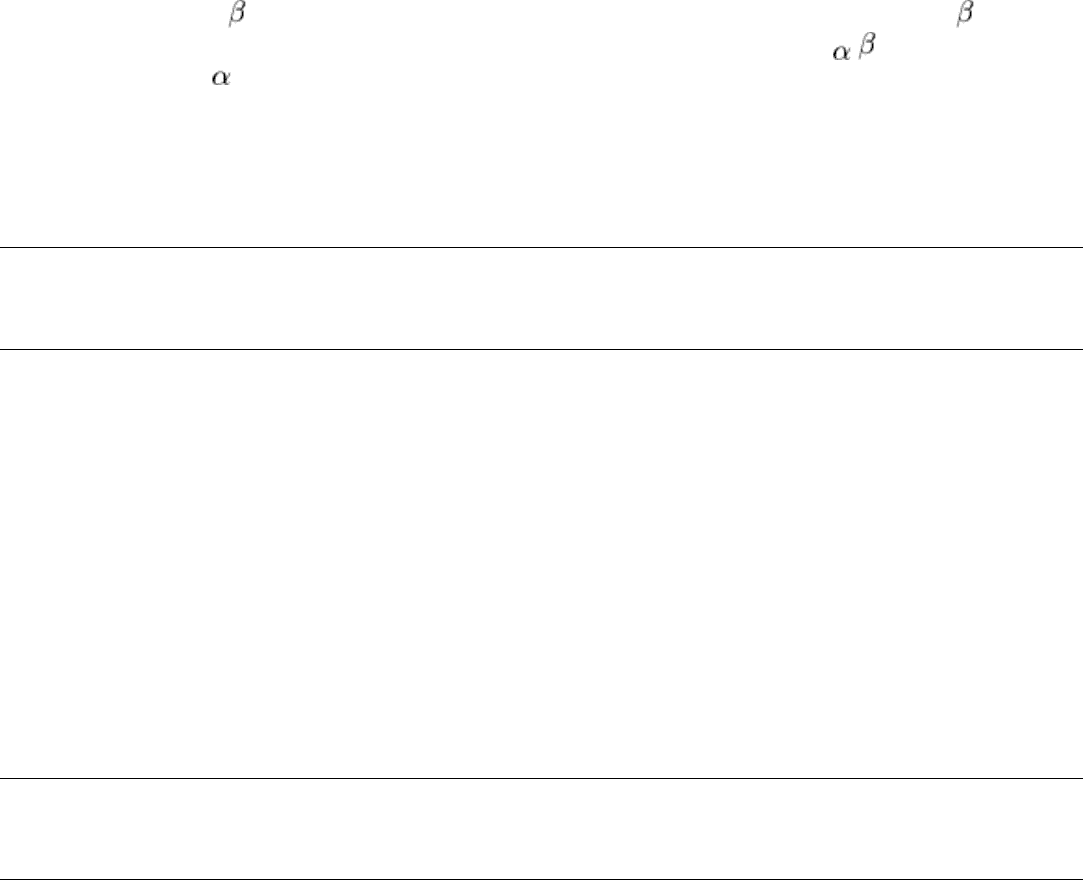
(c)
With either steel, use H12 insert at 429-448 HB.
Some copper alloys cannot be forged to any significant degree, because they will crack. Leaded copper-zinc alloys, such
as architectural bronze, which may contain more than 2.5% Pb, are seldom recommended for hot forging. Although lead
content improves metal flow, it promotes cracking in those areas of a forging, particularly deep-extruded areas, that are
not completely supported by, or enclosed in, the dies. This does not mean that the lead-containing alloys cannot be forged,
but rather that the design of the forging may have to be modified to avoid cracking.
The solubility of lead in -brass at forging temperatures is about 2% maximum, but lead is insoluble in -brass at all
temperatures. Consequently, although a lead content of up to 2.5% is permissible in Cu-40Zn - brasses, lead in excess
of 0.10% in a Cu-30Zn -brass will contribute to catastrophic cracking.
Other copper alloys, such as the copper-nickels, can be forged only with greater difficulty and at higher cost. The copper-
nickels, primarily because of their higher forging temperatures, are sometimes heated in a controlled atmosphere, thus
complicating the process. The silicon bronzes, because of their high forging temperatures and their compositions, cause
more rapid die deterioration than the common forging alloys.
Forging of Copper and Copper Alloys
Robert A. Campbell, Mueller Brass Company
Machines
Most copper alloy forgings are produced in crank-type mechanical presses. With these presses, the production rate is
high, and less operator skill is needed and less draft is required than in forging copper alloys in hammers.
Press size is normally based on the projected (plan) area of the part, including flash. The rule of thumb is 0.5 kN of
capacity per square millimeter of projected area (40 tonf/in.
2
). Therefore, a forging with a projected area of 32.2 cm
2
(5
in.
2
) will require a minimum of 1780 kN (200 tonf) capacity for forgings of up to medium severity. If the part is
complicated (for example, with deep, thin ribs), the capacity must be increased.
Speed of the press is not critical in forging copper alloys, but minimum duration of contact between the hot forging and
the die is desirable to increase die life. Detailed information on hammers and presses is available in the articles "Hammers
and Presses for Forging" and "Selection of Forging Equipment" in this Volume.
Forging of Copper and Copper Alloys
Robert A. Campbell, Mueller Brass Company
Dies
Dies designed for forging copper or copper alloys usually differ from those designed for forging the same shapes from
steel, as follows:
• The draft angle can be decreased for forging copper (3° max and often less than 3°)
• The die cavity is usually machined to dimensions that are 0.005 in./in. less than those for forging steels
• The die cavity is usually polished to a better surface finish for forging copper and copper alloys