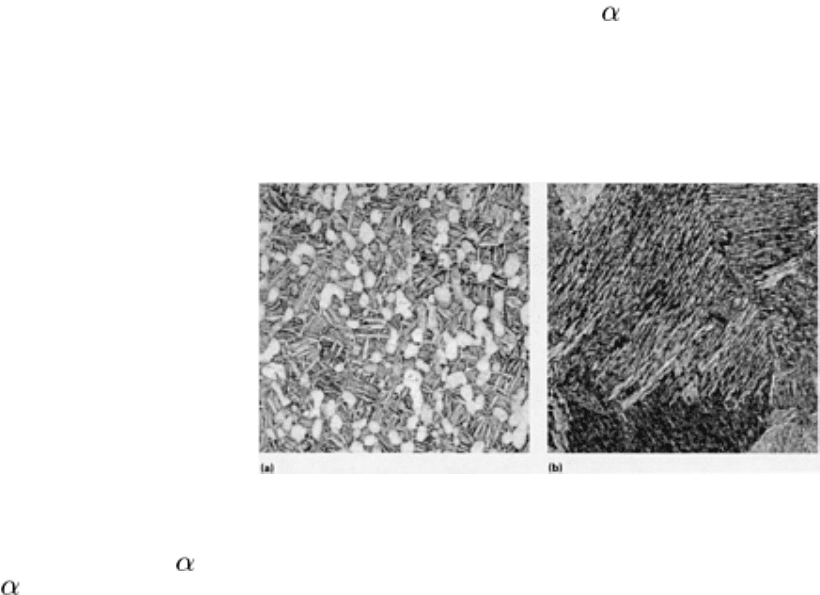
Conventional (α-β) forging of titanium alloys, in addition to implying the use of die temperatures of 540 °C (1000
°F) or less, is the term used to describe a forging process in which most or all of the forging deformation is conducted at
temperatures below the β
t
of the alloy. For α, α-β, and metastable β alloys, this forging technique involves working the
material at temperatures where both α and βphases are present, with the relative amounts of each phase being dictated by
the composition of the alloy and the actual temperature used. With this forging technique, the resultant as-forged
microstructure is characterized by deformed or equiaxed primary in a transformed β matrix; the volume fraction of
primary α is dictated by the alloy composition and the actual working history and temperature (Fig. 5a). Alpha-Beta
forging is typically used to develop optimal strength/ductility combinations and optimal high/low-cycle fatigue properties.
With conventional α-β forging, the effects of working on microstructure, particularly αmorphology changes, are
cumulative; therefore, each successive α/β working operation adds to the structural changes achieved in earlier operations.
Fig. 5 Typical microstructure of forged titanium alloys. (a) α -β forging/heat treatment of alloy Ti-6Al-
Equiaxed primary in transformed β. 200×. (b) β forging of alloy Ti-6Al-4V.
Widmanstätten or acicular primary
in transformed β. 200×.
Example 1: Conventional α-β Forging of a Compressor Disk in Three Operations.
A 660 mm (26 in.) diam compressor disk, with a rim 44.5 mm (1.75 in.) thick and a web 19 mm (0.75 in.) thick was α-β
forged from Ti-6Al-4V in three operations, as follows:
• Upset forged in a 160 kN
(35,000 lbf) hammer, using a starting stock temperature of 980 °C (1800 °F)
to reduce the stock height from 250 to 75 mm (10 to 3 in.)
•
Blocked in a 160 kN (35,000 lbf) hammer to a rough contour, using a starting temperature of 955 °C
(1750 °F), reducing rim thickness to 50 mm (2 in.) and web thickness to 25 mm (1 in.)
•
Finish forged in a 160 kN (35,000 lbf) hammer to the final outline, starting at 955 °C (1750 °F),
reducing rim thickness to 44.5 mm (1.75 in.) and web thickness to 19 mm (0.75 in.)
Beta forging, as the term implies, is a forging technique for α, α-β, and metastable β alloys in which most or all of the
forging work is done at temperatures above the β
t
of the alloy. In commercial practice, β forging techniques typically
involve supertransus forging in the early and/or intermediate stages with controlled amounts of final deformation below
the β
t
of the alloy. Actual final subtransus working criteria are dependent on the alloy, the forging design, and the
mechanical property combinations sought.
In β forging, the working influences on microstructure are not fully cumulative; with each working-cooling-reheating
sequence above the β
t
, the effects of the prior working operations are at least partially lost because of recrystallization
from the transformation upon heating above the β
t
of the alloy. Beta forging techniques are used to develop
microstructures characterized by Widmanstätten or acicular primary α morphology in a transformed β matrix (Fig. 5b).
This forging process is typically used to enhance fracture-related properties, such as fracture toughness and fatigue crack
propagation resistance, and to enhance the creep resistance of α and α-β alloys. In fact, several recently developed α
alloys (such as IMI 829 and 834) are designed to be β forged to develop the desired final mechanical properties. There is
often a loss in strength and ductility with β forging as compared to α-β forging. Beta forging, particularly of α and α-β
alloys, has the advantages of significant reduction in forging unit pressures and reduced cracking tendency, but it must be