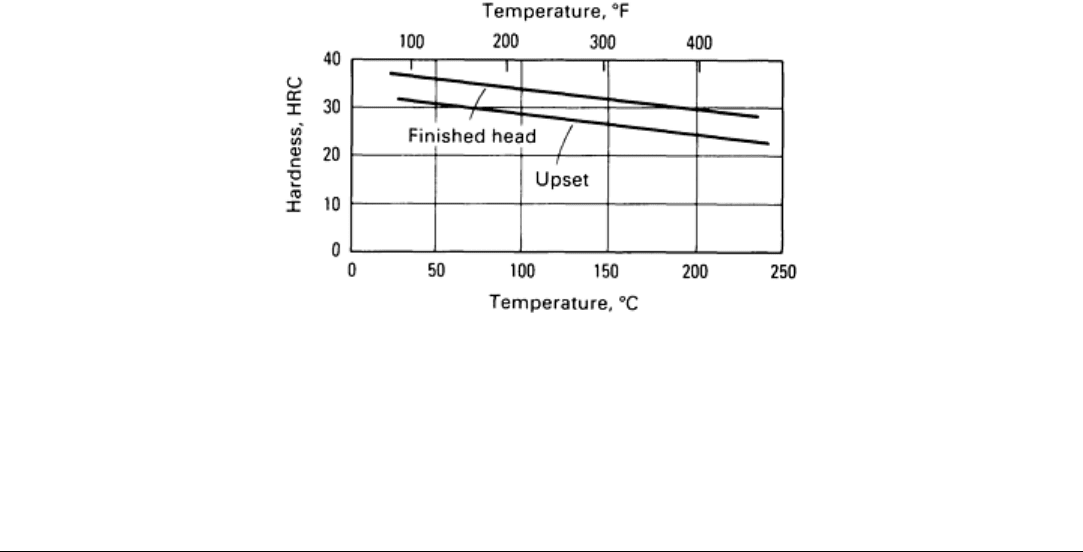
Direct resistance heating, on the other hand, has the advantages of simplicity of equipment, accuracy of control, safety
(because voltage is low), and adaptability to heating of a continuous length of work metal. The usual setup for resistance
heating employs a second feeder-roll stand similar to that already on the header. The second stand is positioned about 1.5
m (5 ft) behind the first, and the wire stock (work metal) is fed through both sets of rolls. Leads from the electrical
equipment are attached to the two sets of rolls, and the circuit is completed by the portion of the wire that passes between
them. The wire (work metal) then becomes the resistance heater in the circuit.
Tools. Whether or not the same tools can be used for warm heading as for cold heading depends entirely on the
temperature of the tools during operation. Although the tools usually operate at a temperature considerably lower than
that of the work metal, it is important that the tool temperature be known. Tool temperature can be checked with
sufficient accuracy by means of temperature-sensitive crayons. Under no circumstances should the tool be allowed to
exceed the temperature at which it was tempered after hardening. This tempering temperature is usually 150 °C (300 °F)
for carbon tool steel such as W1 or W2. Tools made from a high-alloy tool steel, such as D2, ordinarily should not be
permitted to operate above 260 °C (500 °F).
When tool temperatures exceed those discussed above, the use of tools made from a hot-work tool steel, such as H12, is
appropriate. However, the lower maximum hardness of such a steel somewhat limits its resistance to wear. A high-speed
tool steel such as M2 will provide the high hardness and the resistance to tempering needed for long tool life.
Other Advantages of Warm Heading. As the heading temperature of a work-hardenable material increases, the
resulting hardness decreases, as shown in Fig. 15. Therefore, if a material is warm headed, the hardness will remain low
enough to permit such secondary operations as thread rolling, trimming, drilling, and slotting.
Fig. 15 Effect of heading temperature on the hardness of the upset portion and finished head of t
stainless steel flat-head machine screws.
In cold heading, the upset head of a work-hardening metal is very hard, a rolled thread is moderately hard, and the
undeformed shoulder is relatively soft. These variations can be minimized by warm heading.
Cold Heading
Reference
1.
"Upsetting," technical brochure, National Machinery Company, 1971, p 11