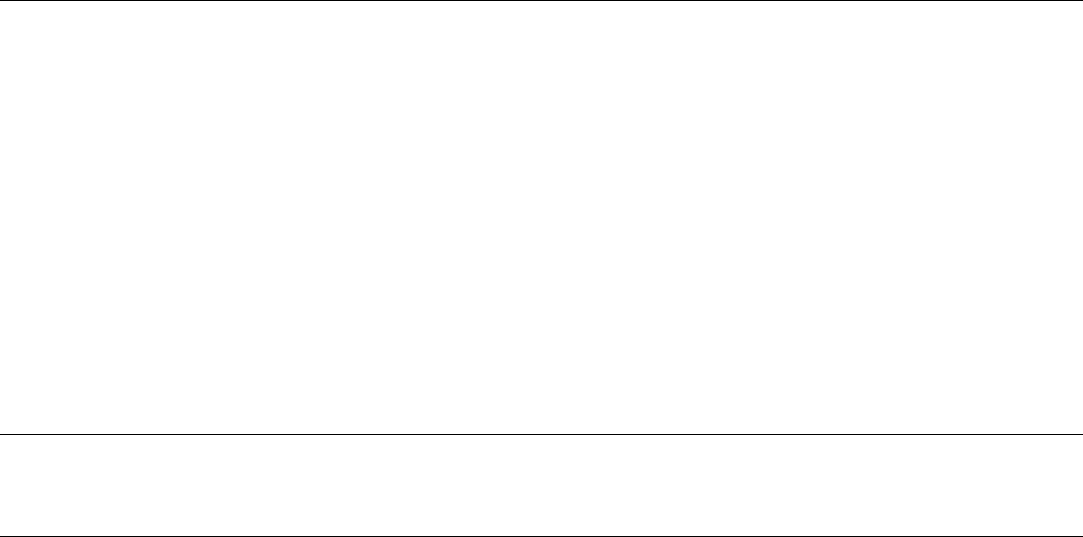
In practice, circumferential speeds to 3.6 m/s (12 ft/s) are used on smaller mills, and 1 to 1.6 m/s (3 to 5 ft/s) on larger
mills. Diameter growth rates to 35 mm/s (1.4 in./s) are usually achieved during the main ring expansion phase; growth
rates of 1 mm/s (0.4 in./s) are reached during the rounding or calibration phase.
References cited in this section
1.
K.H. Weber, Stahl Eisen, Vol 79, 1959, p 1912-1923
2.
R.H. Potter, Aircraft Prod., Vol 22, 1960, p 468-474
3.
W. Johnson and G. Needham, Plastic Hinges in Ring Indentation in Relation to Ring Rolling,
Sci., Vol 10, 1968, p 487-490
4.
G. Vieregge, "Papers on the Technology of Ring Rolling (unpublished)," Wagner Dortmund
5.
J.B. Hawkyard and G. Moussa, "Studies in Profile Development and Roll Force in Profile Ri
Paper presented at the Ninth International Forging Congress, Kyoto, Japan, 1983
6.
H. Wiegels, U. Koppers, P. Dreinoff, and R. Kopp, Methods Applied to Reduce Material and Energy
Expenditures in Ring Rolling, Stahl Eisen, Vol 106, 1986, p 789-795
7.
Y. Toya and T. Ozawa, "Analysis of Simulation in Ring Rolling," Paper presented at the Ninth International
Forging Congress, Kyoto, Japan, 1983
Ring Rolling
C.R. Keeton, Ajax Rolled Ring Company
Blank Preparation
The manufacture of seamless rolled rings consists of two basic processes: the production of a preform or blank, and the
expansion of that blank on a ring mill. Blank preparation can be carried out adjacent to the ring mill with no reheating
before ring rolling, or--as is often the case in older plants--blank forming can be done separately (even in separate
buildings) on several different pieces of equipment. These blanks are then gathered together in logical groups to be
reheated prior to rolling.
The separate blanking approach is quite often found where aircraft ring materials are involved. This is because rolling
cycle time is usually only a fraction of blank preparation time and because cold inspection and rectification of blank
defects may be necessary before rolling.
Because many ring rolling operations are an outgrowth of conventional forge shops, the equipment and methods
previously used to produce totally forged rings are often employed in more limited fashion to prepare blanks. Open-die
hammers and presses, with highly skilled operators and using a wide variety of loose tooling pieces (for example,
punches, saddles, and bars), can often produce practically all required blank sizes and shapes. Hammers are especially
versatile and have the advantage of much lower initial cost than the equivalent press. However, environmental noise
problems have tended to limit new installations. Hammers and general-purpose presses tend to be labor intensive and
have relatively low output rates compared with presses designed specifically for producing blanks.
The trend with most installations in recent years, particularly when the more easily worked materials (for example,
carbon, alloy, and some stainless steels) are involved, has been for the blanking press to be integrated with the ring mill
into a ring production unit. In these installations, the capabilities of the blanking press are matched to those of the specific
ring mill.
Theoretical considerations regarding blank dimensions were explained in the section "Product and Process Technology"
in this article, and the importance of starting with the correct blank-height-to-wall thickness relationship was stressed.
Beyond this, it is important that the methods used to form the blank do not create quality problems (for example, off-
center or ragged punching) at the rolling stage.