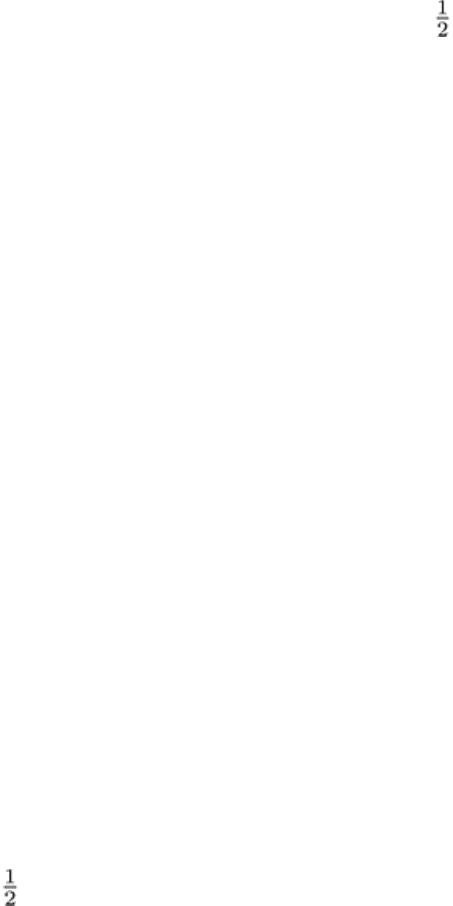
Creeping-spindle swaging (Fig. 4c) employs the principles of both standard rotary and stationary-spindle swaging.
The spindle and dies are mounted on a shaft that rotates slowly inside the rapidly rotating roller cage, thus permitting
more accurately controlled reciprocation of the dies.
Alternate-blow swaging (Fig. 4d) is accomplished by recessing alternate rolls; in this configuration, when two
opposing rolls hammer the dies, the rolls 90° away do not. This eliminates fins on the workpiece.
Die-closing swagers (Fig. 4e) are used when the dies must open more than is possible in a standard rotary swager to
permit loading. Die-closing swagers are essentially of the same construction as the standard rotary swagers described
above. Both have similar components, such as dies, rolls, roll rack, inside ring, spindle, and shims.
The main difference between die-closing and standard rotary swagers is the addition of a reciprocating wedge mechanism
that forces closure of the taper-back dies, as shown in Fig. 4(e). The wedge mechanism consists of a wedge for each die
that is positioned between the die and the backer. The rotating dies open by centrifugal force and are held open by springs
or other mechanical means when the power-actuated wedge mechanism is in the back position. Wedge control of the die
opening permits the work to be placed in the machine in a predetermined position when the dies are open. Reduction per
pass is limited to 25% of the original diameter of the workpiece, and the wedge angle of the dies should not exceed 7 °.
Swaging by Squeeze Action. The impact action common to standard rotary swagers can be slowed to produce a
squeezing action by employing a backer cam. The design of the crown and the width of the backers are such that at least
one roll is always in contact with the backer. The shape of the crown can be a single curve or two radii that approximate a
sine curve. Both of these backer designs are shown in Fig. 5. Machines that use a sine curve type backer have fewer rolls
than a standard swager.
Swaging with squeeze action is used to obtain greater reduction in area than that normally produced by impact action. It is
also used to produce intricate profiles on internal surfaces with the aid of a mandrel.
Compared to impact forming with standard swagers, squeeze forming produces less noise and vibration, requires less
maintenance of rolls and backers, and can produce greater reduction and closer tolerances. Standard rotary swagers,
however, are simpler to operate and lower in cost, require less floor space, and are faster for small reductions.
Rolls and backers used for cold swaging are made from tool steel. The grade of tool steel used varies considerably,
although many rolls and backers are made from one of the shock- or wear-resistant grades (depending on application)
hardened and tempered to 55 to 58 HRC.
Almost all rolls and backers become work hardened. The degree of work hardening depends on the severity of reduction
of the swaged workpiece, the swageability of the work metal, the material used for the rolls and backers, total operating
time, and adjustment of the machine. Rolls, backers, and dies used in cold swaging are stress relieved periodically at 175
to 230 °C (350 to 450 °F) for 2 to 3 h in order to reduce the effects of work hardening and to prolong service life. The
stress-relieving temperature used must not be higher than the original tempering temperature, or softening will result. The
frequency of stress relieving depends on the severity of swaging. Under normal conditions, steel rolls and backers should
be stress relieved after every 30 h of operation. Further improvements in tooling life and overall process costs are
achieved by using replaceable inserts in the working area of the backers as shown in Fig. 5(d). These inserts can be
carbide, and they have contoured forms that improve tool life and precision and reduce noise during swaging.
Stress relieving is usually not required for rolls and backers used for hot swaging, because some stress relief occurs each
time heat transfers from the hot workpiece to the rolls and backers. These components are also less susceptible to work
hardening than rolls and backers in cold swaging, because less force is required to form the part by hot swaging.
The rolls and roll rack of a four-die machine are subject to about 1 times as much wear as those in a two-die machine;
therefore, they must be replaced more often. Other components, such as the spindle and cap, liner plates, backers, and
dies, have about the same rate of wear in both types of machines; however, replacement cost of these components is lower
for a two-die machine.
The number of rolls in a four-die machine must be divisible by four, so that they can be placed at 90° spacing. Therefore,
a ten-roll machine is limited to using two dies.