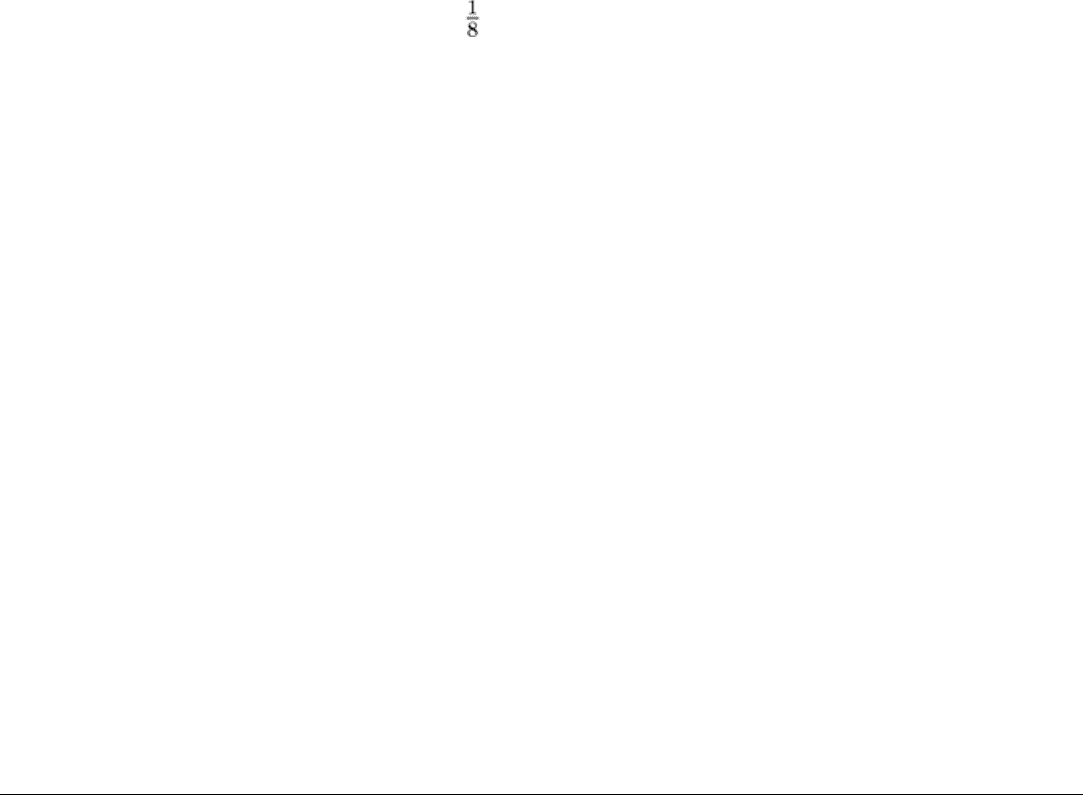
Tungsten and molybdenum must be worked at elevated temperature (900 to 1605 °C, or 1650 to 2925 °F, for
tungsten; 605 to 1425 °C, or 1125 to 2600 °F, for molybdenum) because of their low ductility at room temperature. A
tungsten ingot is usually swaged to about 3.2 mm ( in.) in diameter, although it can be swaged to a diameter of 1 mm
(0.040 in.). After this, the ingot is ductile enough to be hot drawn. The procedure for swaging molybdenum is essentially
the same as for tungsten.
Equipment for Hot Swaging. All machines employed for cold swaging can be used for hot swaging by incorporating
either a water jacket or a flushing system. A water jacket is simply a groove in the bore of the swager head in the area of
the inside ring. The groove is connected to a continuous water supply to dissipate heat.
A flushing system introduces a cooling compound at the upper rear of the head. The compound is pumped through the
machine and exits at the lower front, from which it flows by gravity through a water cooler before entering the supply
tank. This tank is equipped with a filter through which the cooling medium passes before re-entering the machine.
In addition to cooling, the flushing system removes accumulated foreign matter and lubricates the working parts of the
swager. Although flushing removes foreign substances such as scale and sludge, the method used for heating the
workpiece should produce the least possible oxidation.
Dies for hot swaging must be made of material that will resist softening at elevated temperature. High-speed steels and
cemented carbides are satisfactory materials for hot swaging dies.
A common production procedure for hot swaging is the tandem arrangement of several swagers, each of which is
equipped with a heating furnace in front of the machine and close to the dies. The furnaces are mounted so that they can
be pushed aside for quick changing of the dies. Drag rolls are mounted at the rear of each swager to pull the workpiece
through the furnace and the machine. Each drag roll mechanism is equipped with a variable-speed drive to regulate the
rate of feed into the swaging machine. Feed for this type of operation ranges from 1520 to 6000 mm/min (5 to 20 ft/min).
Lubrication. In addition to preventing seizure between the dies and the workpiece, lubricants minimize wear of the
backers, shims, dies, spindle side plates, back plates, rolls, and swager gate. However, the flow of the lubricant must be
controlled to prevent excessive cooling of the workpiece. Lubricants used for hot swaging should be free from chlorine
and sulfur.
Rotary Swaging of Bars and Tubes
Material Response
In addition to the effect of inclusions and high initial hardness on promoting fracture during swaging, the cold-swaged
products may exhibit unanticipated mechanical properties--for example, reduced hardness, reduced yield stress, and either
growth or constriction of the tube inside diameter after machining of the outside diameter. These unanticipated properties
have been attributed to the Bauschinger Effect (that is, a reduction of the yield stress following a stress reversal) and to
residual stress.
Decreasing yield stress with continued reduction, to a minimum at 20 to 30% area reduction, has been observed
during the swaging of rifle barrels. At higher reductions, the yield stress continued to increase.
Radial hardness variations have been observed after tube swaging over a mandrel. The difference between the
highest and lowest readings was 8 Rockwell C points, and the readings were typically equal to or less than the original
blank hardness. After a low-temperature stress-relief treatment (10 °C, or 50 °F, below the tempering temperature of the
steel blank), the swaged tubes had hardnesses greater than the original heat-treated blank by up to 3 Rockwell C points,
which would be expected for a 20% area reduction.
Residual stress after cold tube swaging can be controlled by tool design. For example, the same product could be
produced with either compressive or tensile residual stresses at the inside diameter or negligible residual stress throughout
the product. The significant tool design parameters affecting residual stress are ovality, die angle, blade length, reduction
in area, and secondary reductions (small, usually less than 0.05% area reductions near the start of the die exit relief),
usually on the die. Ovality (expressed as percent overgrind of the final product diameter relative to the ground die inside
diameter) in four-die tube swaging is the most significant parameter affecting residual stress, as shown in Fig. 27. The