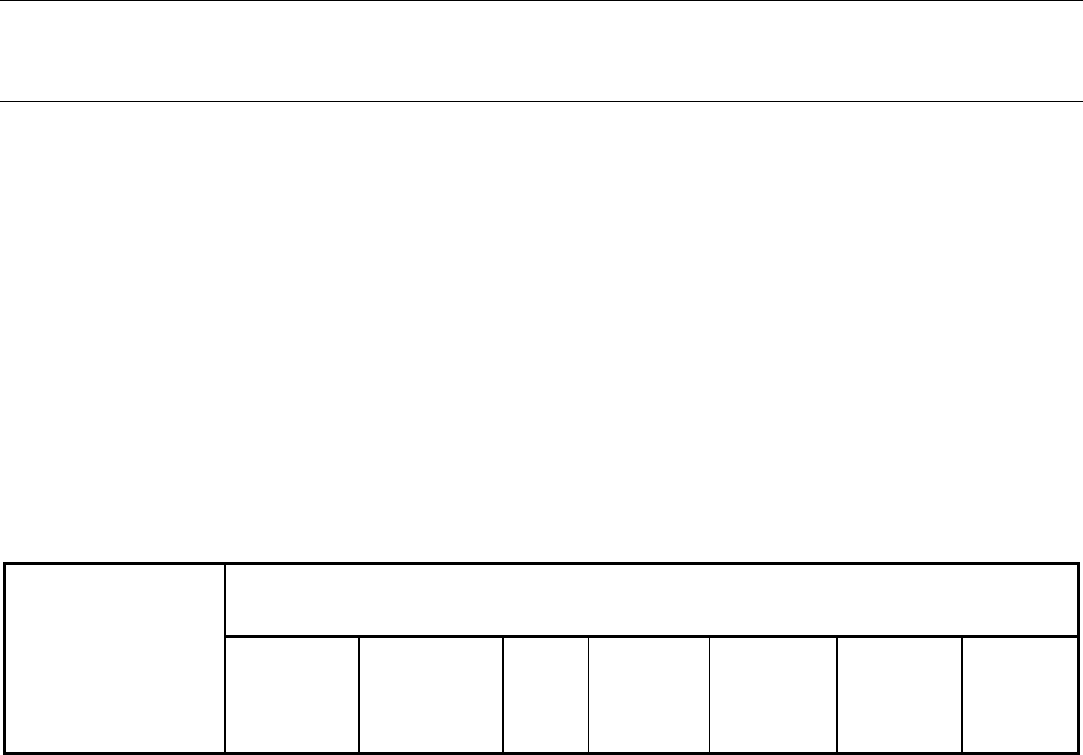
Proper selection of die material for a given application depends on the operating temperature, forging pressure
requirements, and anticipated die life. As shown in Fig. 9, TZM is the most practical die material for the isothermal
forging of nickel-base alloys (which are forged at 1040 °C, or 1900 °F, or higher), while Alloy 100 and Astroloy are
better suited to the hot-die and isothermal forging of α-β titanium alloys, such as Ti-6Al-4V, forged at 925 to 980 °C
(1700 to 1800 °F). For β-forged titanium alloys such as Ti-10V-2Fe-3Al, which can be forged at 815 °C (1500 °F) or
lower, Alloy 718 or Alloy 713LC dies at 650 to 705 °C (1200 to 1300 °F) may provide a satisfactory cost-effective
alternative. Astroloy or Alloy 718 dies have also been successfully used for forging of superalloys such as Alloy 718 at
650 to 760 °C (1200 to 1400 °F). When large quantities of parts are to be produced, die life becomes an important
consideration, and the cost of die material becomes a secondary issue.
Die Manufacturing. The die materials used for hot-die and isothermal forging are more difficult to machine than
conventional die steels. Most dies manufactured for axisymmetric forgings are turned on a lathe, but dies for asymmetric
parts may have to be milled, which can be very expensive. Two approaches have been used in these cases to reduce the
cost of die manufacturing. Several early attempts with smaller die sizes and simple geometries used precision cast dies.
The more widely used technique is to produce these dies for structural shapes by electrical discharge machining using a
precision-machined graphite electrode. The tolerances on die sinking are held to better than ±0.1 mm (±0.005 in.).
Because most of the die materials are not weld repairable, accuracy is critical in the machining of the dies.
Atmospheric Control. When TZM is used as a die material, a special atmospheric control with either vacuum or inert
gases is necessary because of the tendency of molybdenum alloys to oxidize severely at temperatures greater than 425 °C
(800 °F). This necessitates the introduction of a special enclosure in the press around the die system and associated
enclosures for heating of multiples and material handling. Therefore, processes using TZM dies (mostly isothermal
forgings) have dedicated equipment. On the other hand, most nickel-base alloys can be heated in a normal atmosphere;
therefore, most hot-die forging operations that use these die materials are performed in conventional presses, with the
only additional requirement being the introduction of the die stack and/or the die heating system described earlier. These
presses do not have to be dedicated, and they can be used interchangeably for conventional forging as well as hot-die
forging.
Isothermal and Hot-Die Forging
Sanjay Shah, Wyman-Gordon Company
Forging Design Guidelines
The principal criterion in designing hot-die and isothermal forgings is to design the forging as close as possible to the
machined part with a potential of using as-forged surfaces if feasible. Beyond this, it is difficult to establish one set of
guidelines for a variety of parts that may be considered for near-net shape applications. Each part family must be
considered individually in order to ensure the optimal, most cost-effective design. There are, however, some general
guidelines that can be used in designing these parts.
Guidelines for forging design parameters, such as minimum web and rib thicknesses, corner and fillet radii, draft angle,
and design cover, are presented in Table 2 for various alloys and geometries. These values indicate the current industry
capabilities, and a significant amount of research and development effort is being applied to improve them, including an
increased size capability, geometries that are closer to the finished part, and the ability to provide negative draft and
contour capabilities through the use of split dies.
Table 2 Typical near-net shape forging design parameter
Parameters
Material
Miximum
plan
view area
Forging
envelope
Draft
angle,
degrees
Minimum
corner
radius
Minimum
fillet
radius
Minimum
web
thickness
Minimum
rib
width