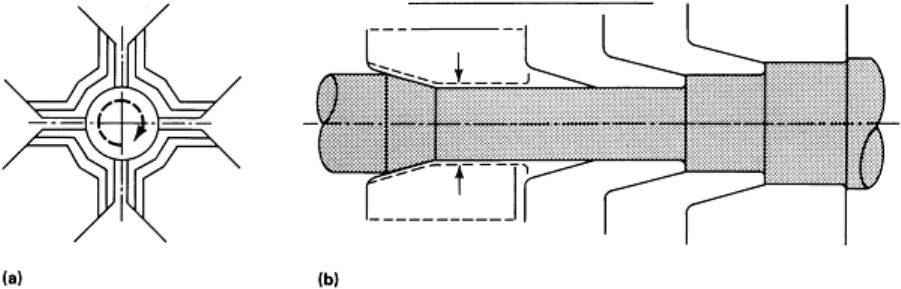
forging box. (b) Longitudinal section through forging box. 1, eccentric shaft; 2, sliding
block; 3, connecting rod;
4, adjustment housing; 5, adjusting screw; 6, hydraulic overload protection; 7, hammer adjustment drive
shafts; 8, chuckhead; 9, centering arms; 10, clutch; 11, clutch disk.
Depending on its application, the part-handling system of the machine can be equipped with either one or two workpiece
manipulators, which differ widely from conventional forging manipulators. In contrast to press or hammer forging, the
workpiece axis in radial forging is always maintained on the forging machine centerline, regardless of the diameter. The
manipulator moves only in the longitudinal direction. In order to achieve exact guidance, the chuckhead slides on a
machine bed. During the forging of round cross sections, the chuckhead rotates the workpiece in cycle with the forging
hammers; that is, the rotary movement will be stopped during the time the hammers are in contact with the workpiece.
The rotary movement of the chuckhead spindle is synchronized with the hammer blows; therefore, twisting of the
workpiece is eliminated. The indexing positions of the chuckhead spindle required for forging squares, rectangles, or
hexagons can be set automatically.
In radial forging, the entire forging process, including loading and unloading, can be performed automatically by
computer numerical control (CNC). The forging process is no longer dependent on the discretion of the operator, and an
optimal forging program is maintained in an unchanged manner. This guarantees the manufacture of uniform forged
pieces, which are trimmed to optimal machining allowances. These workpieces are well suited to subsequent machining
on CNC lathes because of their consistent dimensional accuracy.
The technology of the four-hammer forging machine differs from that of all other hot-forming methods. Conventional
presses and hammers, or even rolling mills, use only two tools per forming operation. In the radial forging machine,
however, a workpiece is formed at the same time by four hammers arranged in one plane (Fig. 3). The free spreading that
occurs between the two contacting tools in all conventional forging methods is eliminated. A radial press contacts the
circumference of the workpiece equally and puts the entire surface of the workpiece under compressive stresses. These
compressive stresses prevent the formation of surface cracks during the forging process and improve existing defects.
Fig. 3 Arrangement of hammers in a four-
hammer radial forging machine. The workpiece rotates
intermittently, and the diameter of the forged part is determined by the stroke position of the tools.
(end) view. (b) Side view
In forging between four hammers, temperature increases will occur in the work material that depend on the deformation
rate and the forming resistance of the material. The higher the forming resistance, the higher the temperature increase at
each pass. Therefore, the temperature loss of the workpiece (because of heat radiation) can be compensated for by
preselecting the correct deformation rate, and forming of the workpiece can take place in temperature ranges with the
highest material ductility. In practical terms, this means that all forming can be done in one heat from the ingot to finished
bar steel, regardless of the alloy. Chamber furnaces, pit furnaces, and hearth-type furnaces can therefore be replaced by
continuously operating furnaces. Material can be transported to and from the machine on roller conveyors, and the entire
manufacturing process--heating the ingot, radial forging, dividing and cutting the ends of formed parts, and cooling or
annealing--can be done continuously and automatically.