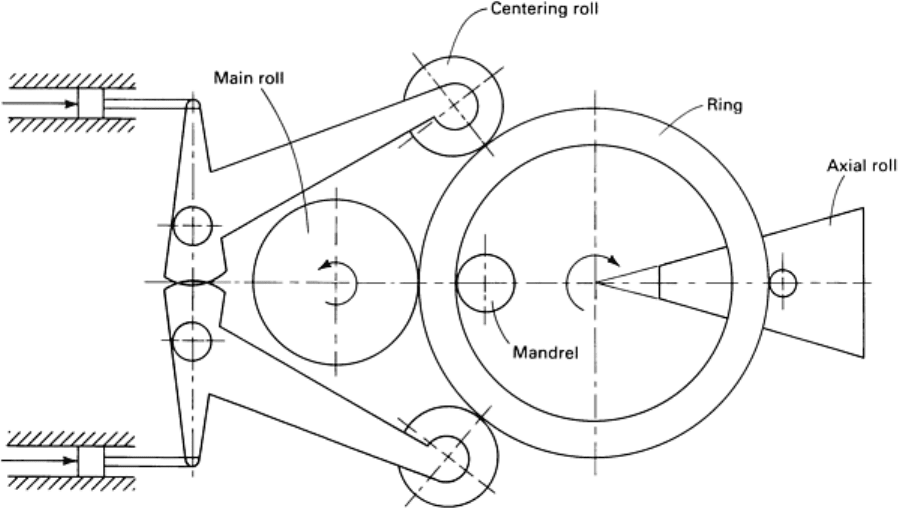
A tracer wheel mounted on slides between the axial rolls contacts the ring outer diameter. The ring diameter is monitored
through measurement of the relative displacement of the tracer wheel and the axial roll carriage.
A pair of hydraulic centering arms (Fig. 7), connected through gear segments, contact the ring outside diameter and
ensure that the ring stays round and in the correct position in relation to the longitudinal axis of the mill. Load cells in
these centering arms detect differences in force against each centering roll. Through the mill control system, the load cells
cause rapid, fine adjustment of axial roll speed to remove any force imbalance and therefore to maintain the correct
positioning of the ring during rolling. Either manually (through a potentiometer) or automatically, the centering force is
reduced as rolling progresses and the stiffness of the ring decreases.
Fig. 7 Schematic of radial-
axial mill showing centering rolls. Mounted in hydraulically controlled arms, the
centering rolls ensure that the ring does not grow out of round and re
mains in the correct position relative to
the longitudinal axis of the mill.
The relationship between radial (wall thickness) and axial (height) reduction is preselected to ensure the absence of ring
surface defects, and it is maintained by computer control. Similarly, the pattern of diameter growth is predetermined and
computer controlled. The mill operator need only set blank and finished ring dimensions at the control desk and initiate
the rolling cycle. Rolling is automatically stopped when finished outside diameter, inside diameter, or mean diameter
(chosen by the operator) is reached.
The reason for the predominance of these radial-axial mills is the wide range of capabilities provided by an individual
mill. A typical midrange machine, with 980 kN (110 tonf) horizontal and 780 kN (88 tonf) vertical force capability and
total motor power of 500 kW, can roll rings weighing less than 45 kg (100 lb) to more than 2000 kg (4400 lb), ranging in
size from 300 mm (12 in.) inside diameter to 3000 mm (10 ft) outside diameter, and from 50 to 500 mm (2 to 20 in.) in
height.
The extraordinary demands made on equipment when rolling superalloys, which have considerably higher resistance to
deformation than carbon and alloy steels, have forced developments and improvements in radial-axial mill design and
construction. These improvements have been beneficial when selectively applied to mills aimed at the less demanding
materials.
High forces are required throughout the rolling of superalloys with little opportunity for final sizing (calibration) of the
ring at reduced forces. Nevertheless, the expensive materials involved place a premium on near-net shape capability.