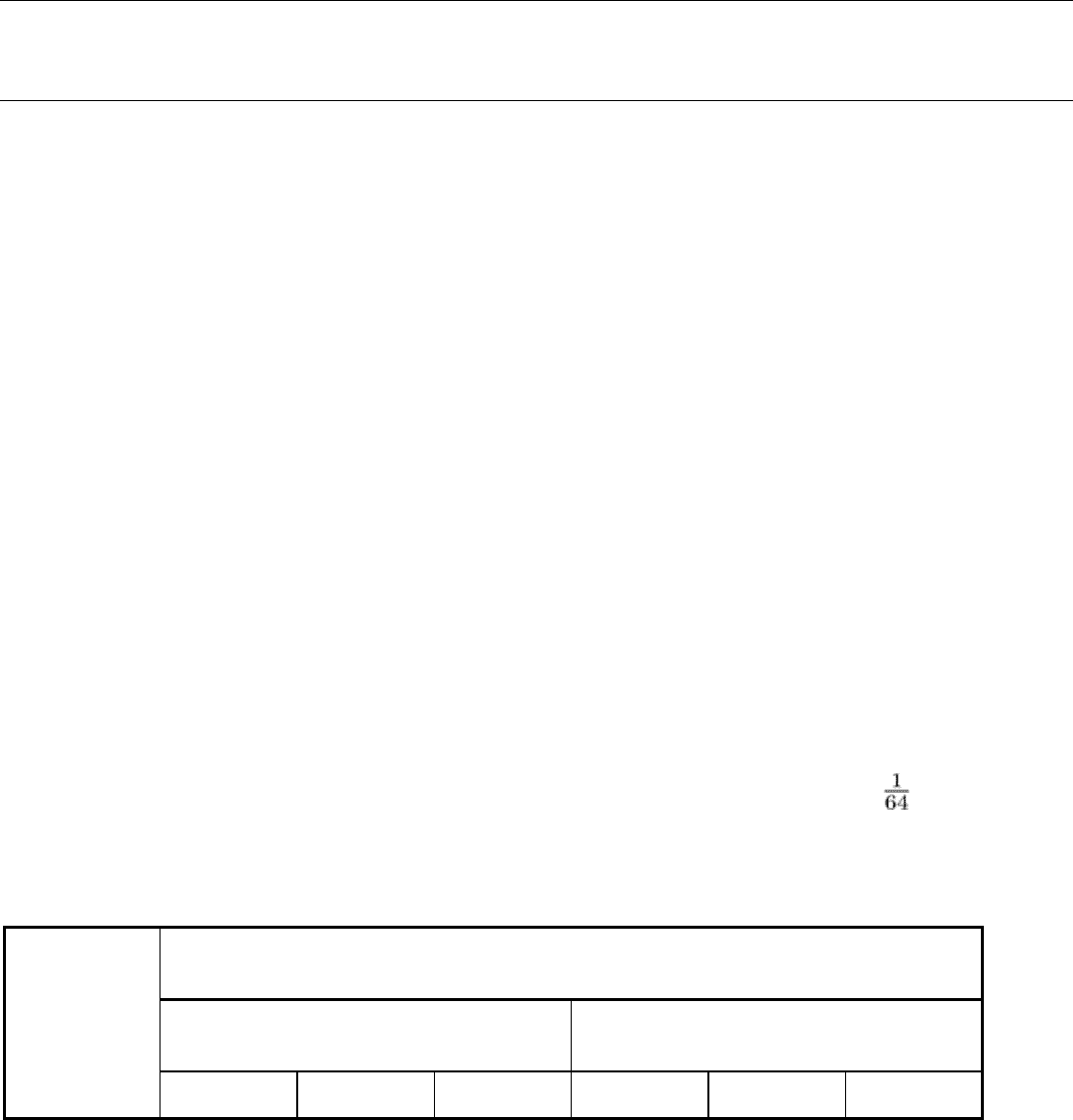
strip depend on the equipment and manufacturing expertise. The shear-to-break characteristics of strip depend on strip
composition and temper.
Effects of Alloy Composition and Temper. The quality of blanked edges--shear to break, rollover, breakout angle,
burr height, and so on--is determined by both die clearance and material characteristics. Burr-free and distortion-free parts
can be cut from annealed copper alloy strip at die clearances to about 5% of strip thickness. Unalloyed coppers, such as
C10100 and C10200, require smaller clearances (usually <5%) and less latitude in actual values to produce burr-free
edges, even in rolled tempers. Copper alloys that contain second-phase particles (for example, C19400), that have high
solute additions (such as C26000 or C51000), and/or that are cold rolled more than 50% generally exhibit high-quality
blanked edges at die clearances in the range of 3 to 12%. Low-lead additions to brass and other copper alloys will
decrease burrs and the shear-to-break ratio in blanking operations--but at some cost to formability in almost all types of
forming.
Forming of Copper and Copper Alloys
Frank Mandigo and Jack Crane, Olin Corporation
Bending
Nature of the Operation. Many connectors, terminals, and spring-like components are fabricated by simple bending
operations. Bending is an operation in which a blanked coupon is wrapped, wiped, or formed over a die to a specified
radius and bend angle. Bend formability is usually expressed as minimum bend radius R in terms of strip thickness t (R/t).
Minimum bend radius is defined as the smallest radius around which a specimen can be bent without cracks being
observed on the outer fiber (tension) surface. Bend deformation is highly localized and is confined to the region of the
workpiece in contact with the bending die. Workpiece thickness is not substantially reduced unless the bend radius is less
than 1.0t or the part is coined during bending. A detailed review of bend testing is provided in the Section "Bend Testing"
in Mechanical Testing, Volume 8 of ASM Handbook, formerly 9th Edition Metals Handbook.
Materials Characteristics. Ductility is the principal materials factor that determines bend formability. The ductility
factor of first order importance is the ability of a material to distribute strain in a highly localized region, that is, necking
strain. The necking strain available depends on alloy composition and temper. As strength is increased by cold work, the
ability of an alloy to distribute necking strain decreases. The extent to which bend formability is decreased with
increasing strength is dependent on the alloy composition and the strengthening mechanism. Conventional tensile
elongation cannot be used to predict bend formability, because it does not adequately account for the contribution of
necking strain. However, if the tensile specimen gage length were decreased to define an area of deformation equal to that
deformed during bending, comparable ductility values would be obtained.
Effect of Alloy Composition, Temper, and Orientation. Bend data for a wide range of copper alloys are
summarized in Table 6. Strength-to-bend formability characteristics are dependent on alloy composition, temper, and
orientation. The principal strengthening mechanism is through solute additions to increase the work-hardening rate. For
example, additions of 15 and 30% Zn to copper increase the tensile-strength-to-bend properties by 220 and 290 MPa (32
and 42 ksi), respectively, for 0.25 mm (0.010 in.) thick good-way bends at a bend radius of 0.4 mm ( in.). Precipitation
strengthening is also an important mechanism employed to improve the strength-to-bend performance of copper alloy
strip, particularly if the part is bent in a softer temper and subsequently aged to a higher strength.
Table 6 Maximum strengths required to make the indicated bends in various copper alloys
Maximum strength required to make bend of indicated radius in material of indicated thickness, MPa (ksi)
Good-way bend
Bad-way bend
UNS designation
0.25 (0.010)
(a)
0.50 (0.020)
(a)
0.76 (0.030)
(a)
0.25 (0.010)
(a)
0.50 (0.020)
(a)
0.76 (0.030)
(a)