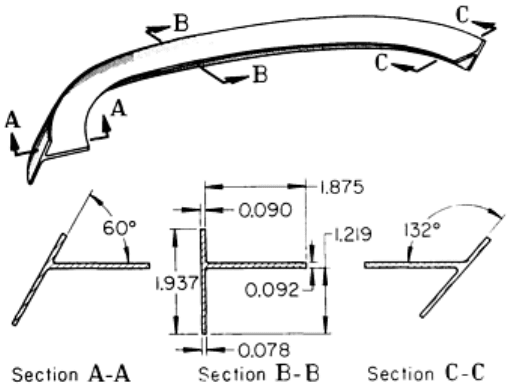
Tools. The materials used for the form block or die depend on the production quantities required, the severity of local
stress and wear on the die, and the thickness and wear properties of the alloy to be formed. Materials include wood,
plastics, faced concrete, cast zinc alloys, aluminum tool and jig plate, cast iron, and (rarely) steel or chromium-plated
steel.
Lubricants are recommended in the stretch forming of aluminum alloys. Water-soluble oils are commonly used, with
viscosity dependent on the severity of forming. Calcium-base greases, paraffin, beeswax, and commercial waxes also are
used. The application of too much lubricant can result in buckling of the workpiece.
Sometimes a layer of sheet rubber, glass cloth, or plastic between die and workpiece serves as a lubricant. Because of
their inherent lubricity, zinc alloy dies require only a minimum of lubrication. Smooth-surface plastic dies may require no
lubrication, because of their low coefficient of friction against aluminum.
Applications. The various stretch-forming techniques (including stretch drawing, stretch wrapping, and compression
and radial drawing) are used extensively in the aerospace industry. Typical parts produced include wing-skin and fuselage
panels, engine cowlings, window and door frames, and trim panels used in aerospace, automotive, architectural, and
appliance industries.
Stretch draw forming of aluminum is done using both the matched-die and form block techniques. The matched-die
method uses a single-action hydraulic press equipped with a means of closing and moving the jaws that grip each end of
the blank. The punch is attached to the bed of the press, and the die is attached to the ram.
The alternate method uses a form block that is attached to a stationary bed or a hydraulic cylinder. With this method, the
blank is gripped with jaws that hold it in tension or draw it over the form block.
Stretch wrapping uses a form block that is bolted to a rotary table. One end of the blank is clamped to the form block
or to a table-mounted gripper. A hydraulic cylinder or a gripper applies tension to the other end of the blank while the
form block revolves into it with the turning of the table.
Shaped form blocks that match the contour of extruded or rolled sections are used for support during forming. Filler
strips, either segmented or made of low-melting alloys or strips of aluminum, are used to prevent the collapse of sections.
Radial-draw forming is a combination of stretch wrapping and compression forming. The workpiece is pressed
against the form block by a roller or shoe while being wrapped around the turning form block. This method can be used,
for example, to form a flange to a compound curvature while forming a leg, as in the part shown in Fig. 11.
Fig. 11 Aluminum alloy 7075-O radial draw formed T-
section with radical changes in angle between leg and
flange. Dimensions given in inches